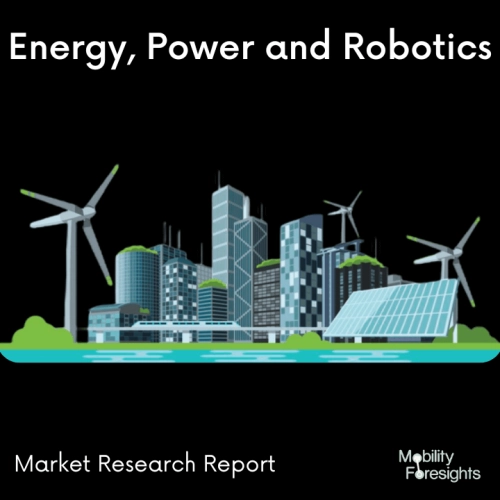
- Get in Touch with Us
Last Updated: Apr 25, 2025 | Study Period: 2024-2030
An energy battery management system is indeed a bit of engineering that is truly committed to the supervision of a battery system, which would be an accumulation of battery packs electrostatically organised in a row x-column composite arrangement to empower transmission of targeted values of voltage and power flow for a period of time against expected load instances.
The battery management system (BMS) is required to monitor the battery state and maintain operational safety. The various BMS architectures have been examined, and the benefits of each have been demonstrated based on the size of the battery system.
Furthermore, typical BMS functions have been defined, with specific emphasis on state of charge estimation. There are certain advantages to using a centralised BMS. For starters, it is more compact.
Second, because there are fewer moving parts, the centralised BMS system is the most cost-effective. The downsides of centralised BMS, on the other hand, are evident.
Because all of the battery packs should indeed be intrinsically related to the BMS, each BMS requires a large number of ports to connect with all of the pack modules. Battery verification, an RTC, storage, and a daisy network are some of the many BMS functioning pieces.
The RTC and storage are utilised for black-box operations, in which the RTC serves as a timestamp as well as the storage stores information, allowing players to understand the battery pack's behaviour prior to a catastrophic occurrence.
Lithium-ion recharging batteries offer the highest energy density and are the preferred choice for battery cells in a wide range of consumer items, from netbooks to electric cars. While they function admirably, they can be harsh if used outside of a typically tight safe.
S No | Overview of Development | Development Detailing | Region of Development | Possible Future Outcomes |
1 | Brill Power launches battery management system capable of increasing life spans by 60% | The BrillMS B62 Premium battery management system can enhance storage capacity by up to 129%, increasing systems uptime. As an âintelligentâ battery system, it can support both passive balancing or active balancing options. | Global Scale | This would enhance better Technologies and production |
The impact of increased utilisation of battery technology (EVs) and plug-in hybrids (HEVs), as well as an increase in industry predilection for rechargeable batteries, encourage investment in the battery management system industry.
Furthermore, the increasing usage of rechargeable batteries across a variety of end-use industries promotes Power Battery Management System market expansion. Nevertheless, the installation of a battery management system raises the entire price of devices, impeding business expansion.
Furthermore, increased use of cloud-connected battery technology, increased penetration of renewables, and increased demand for e-bikes and e-scooters create significant potential prospects for Power Battery Management System market participants.
Furthermore, numerous suppliers functioning in the supply chain are experiencing raw material shortages, which is affecting the industry, and there is a scarcity of raw resources. If somehow the current scenario persists, there is an increasing likelihood of an input materials scarcity.
To minimize Greenhouse Gas (GHG) emissions, governments and organizations have enacted strict rules and policies, such as the Kyoto Protocol. Furthermore, increased awareness of the negative environmental consequences of gasoline and diesel-powered automobiles has resulted in automotive industry advancements such as electric and hybrid vehicles.
Furthermore, rising customer demand for increased vehicle economy and lower fuel prices has resulted in constant technological breakthroughs in electric and hybrid electric cars.
Because batteries in electric cars may only be used under certain circumstances, a battery management system (BMS) is required to monitor battery state and assure the safety of operations.
The Global Power Battery Management System Market can be segmented into following categories for further analysis.
The Battery Management System is composed of the much more complicated fast - acting Power Management that must communicate with some other onboard technologies including performance tuning, climate regulation, telecommunications, and warning systems.
The adoption of an intelligent charging strategy that enhances the connection between both the batteries and the chargers can extend the longevity of recharging NiCad and Nickel Metal Hydride batteries, which are often used in tools and equipment.
The battery gives more information about its own specifications, present state, and bandwidth utilization, which is utilised by the charger to select the best charging strategy or, depending on the application, to manage its utilization.
The primary goal of the charger/battery combo is to allow for the inclusion of a broader range of Protection Circuits that prevent overloads or destruction towards the batteries, hence extending its life.
The system should ensure components that may disrupt or adjust charging based on the set of regulations, which can then be found in either the battery or the charger.
Conversely, energy depletion can indeed be regulated by the platform's battery or demand management circuits. The Fully automated Management System is a tried-and-true innovation wherein the battery transmits messages about its own present configuration to the power adapter, that equates this to the desired position and actually creates an impulse response that is used to initiate control strategies to introduce the existing situation back to normal.
These control signals are part of a Feedback Mechanism, which offers automated correction to keep the battery running within its own specified limits.
Many OEMs rely on dependable Battery Management Systems to ensure that electrical applications run safely and without failure (BMS).
Eberspaecher Vecture offers a comprehensive range of BMS for industrial use-cases under the tagline "Electrify the world": BMS for medical, motive, UPS, storage, and backup applications are included in the portfolio of over 500 designs, which range from simple 1S Protectors to feature-rich basic and large format boards with up to 400 cells in series.
Eberspaecher Vecture creates a wide range of systems, subsystems, and related components for use in BMS applications. Several devices in the large format distributed BMS family are specifically developed for use in storage, UPS, and motive solutions.
The systems include high redundancy, MWh system capabilities, and a variety of unique features like as built-in ground fault detection (GFI), voltage temperature and current redundancies, dual core ASIL D approved processors, and the ability to manage up to 18 contactors.
A precisely focused development for the desired application is achievable thanks to the modular design of the big format BMS, which ranges from 10 kwh to multiple MWh. The integrated BMS series of products is designed to give the end customer with more capability and features in terms of battery management.Connectivity, IoT capabilities, maximum continuous current draw, flexibility, modularity, high redundancy, high safety, and risk reduction are all priorities.
They offer feature-rich capabilities when integrated in portable applications such as robotics, logistics, or storage. The V04265 4S to 16S MOSFET-based high-performance BMS is an example of the product family. It protects 4 to 16 cells in any chemistry and is rated to 95A continuous operation free air (with an industry-leading heat increase of 15C).
With proper heatsinking (passive/active), high current operation of up to 200A is conceivable.Similarly, the V04263 5S to 24S high-performance BMS can accommodate several battery chemistries, with four external contactors and two CAN communication lines capable of driving 400-500A.
Small integrated 1S to 4S BMS are high-performance but low-cost solutions. These have become increasingly common in the medical, consumer, and industrial sectors, where they support equipment like oxygen concentrators, insulin pumps, and ventilators, among other things.For example, the V04278 comes preprogrammed with the specifications listed in the data table, which are compatible from 1S to 4S and support 7A continuous and 10A peak discharge current with high speed short circuit, making it suitable for a wide range of NMC chemical applications.
Over the last several years, nations in growing emerging markets in Asia have also seen a growth in the use of electronic devices such as garden tools, power tools, portable battery packs, and handheld healthcare equipment.
Furthermore, the battery management system checks the status of individual cells in a battery pack.
As a result, using a battery management system could indeed lead to a significant increase in the concluding price of a product or implementation, which might also result in lower consumption from cost-sensitive clients, discouraging manufacturers and retailers from being used battery management systems despite their documented effectiveness.
Nuvation Engineering has been part of the striding development towards better and enhanced technological integrations with better levels of compliance to multiple sector operability.
The High-Voltage BMS controls battery stacks up to 1250 VDC somewhere at cellular as well as stacking levels. Every stacking is managed by one Stacked Switchgear module, which links it to the power storage platform's DC bus.
Every stack's Cellular Interface modules connect directly to lithium batteries to detect cell voltages and temperature levels and to offer cell rebalancing.
Every stack's UL 1973 Accredited BMS components assure safe batteries performance and considerably decrease the work required to pursue UL 1973 and UL 9540 validation of the power storage solutions.
This connects and disengages the batteries stack from the ESS's DC Bus in response to system controller commands. The Cell Connections are intrinsically linked to the battery cells and are used to monitor voltage and temperature as well as execute cell rebalancing.
CyberPower is a consolidated developer of the battery management systems operating in the current market focused on better monitoring and operational control for the software programming systems.
The CyberPower BM100 is a component of a charge controller that also includes a Battery Management and Battery Instrumentation. The system would take a strategy to manage and monitor the battery system, reducing the chance of downtime by ensuring the UPS batteries are fully recharged as well as prepared for use.
The technology may detect a faulty battery early on, reducing the chance of harm to the external battery strings and thereby prolonging battery performance and lowering operational costs.
The battery management system can monitor up to many strings of battery packs and equalise the voltage of each battery, improving power efficiency.
The battery management system can accommodate environmental sensors as well as programming that can be upgraded by the operator. The battery management system is completely Ethernet TCP/IP compliant and has a built - in web server.
Sl no | Topic |
1 | Market Segmentation |
2 | Scope of the report |
3 | Abbreviations |
4 | Research Methodology |
5 | Executive Summary |
6 | Introduction |
7 | Insights from Industry stakeholders |
8 | Cost breakdown of Product by sub-components and average profit margin |
9 | Disruptive innovation in theIndustry |
10 | Technology trends in the Industry |
11 | Consumer trends in the industry |
12 | Recent Production Milestones |
13 | Component Manufacturing in US, EU and China |
14 | COVID-19 impact on overall market |
15 | COVID-19 impact on Production of components |
16 | COVID-19 impact on Point of sale |
17 | Market Segmentation, Dynamics and Forecast by Geography, 2022-2027 |
18 | Market Segmentation, Dynamics and Forecast by Product Type, 2022-2027 |
19 | Market Segmentation, Dynamics and Forecast by Application, 2022-2027 |
20 | Market Segmentation, Dynamics and Forecast by End use, 2022-2027 |
21 | Product installation rate by OEM, 2022 |
22 | Incline/Decline in Average B-2-B selling price in past 5 years |
23 | Competition from substitute products |
24 | Gross margin and average profitability of suppliers |
25 | New product development in past 12 months |
26 | M&A in past 12 months |
27 | Growth strategy of leading players |
28 | Market share of vendors, 2022 |
29 | Company Profiles |
30 | Unmet needs and opportunity for new suppliers |
31 | Conclusion |
32 | Appendix |