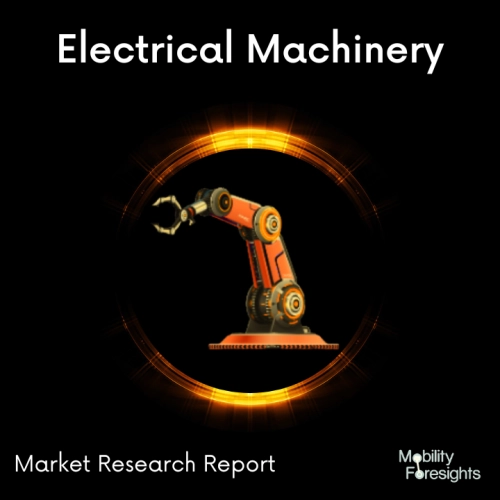
- Get in Touch with Us
Last Updated: Apr 25, 2025 | Study Period: 2024-2030
The Power module soldering inspection system must guarantee maximum heat transfer from the soldered die to the heat sink in order to guarantee the reliability and durability of the power modules. The required thermal coupling can be achieved with low thermal resistivity, but voids in solder connections significantly reduce this coupling.
It is difficult to avoid the formation of enclosed gases, especially in large-scale solder joints that may cover an area of up to 25 cm2. Within this connection, there are frequently voids of varying sizes and positions. They may result in the module's malfunction or even destruction in operation mode due to thermal coupling.
There aren't many ways to find voids after soldering with the technology we have today. The selection of test technologies is even limited by a 100 percent test within the production cycle. Due to the length of time required for image capture and evaluation, acoustic microscopy and computer tomography using an X-ray analysis system are inefficient.
The Global Power module soldering inspection system market accounted for $XX Billion in 2023 and is anticipated to reach $XX Billion by 2030, registering a CAGR of XX% from 2024 to 2030.
The new full nitrogen tunnel wave solder machine from ERSA, the POWERFLOW N2, was made to handle lead-free! The POWERFLOW N2 is an ERSA Power module soldering inspection system that can cut operating costs for lead-free wave solder by as much as 90%! The machine features a 16-inch board width, plug-and-play pre-heat (Medium IR, Convection, Short IR, and now with the new topside Convection), and 1.8 meters of preheat standard.
If necessary, additional pre-heating can be added of up to 2.4 meters. Reduced solder defects result from a new nozzle configuration that brings the chip wave closer to the laminar wave. In the fluxer and pre-heater, this machine has a pin-and-chain transport system that feeds into a finger conveyor in the machine's wave section.
The new fluxer has a bar code scanner that lets you selectively flux and program "keep out areas" for board cutouts, areas of the board where the fluxer won't spray.
Similar to Reflow machines, the POWERFLOW N2 machine has a process gas cleaning system that also controls the Auto Tunnel Temperature Compensation. The machine is ideal for demanding customers who require a 400 mm or 16" tunnel wave due to its low profile of 1.57 m.
Sl no | Topic |
1 | Market Segmentation |
2 | Scope of the report |
3 | Abbreviations |
4 | Research Methodology |
5 | Executive Summary |
6 | Introduction |
7 | Insights from Industry stakeholders |
8 | Cost breakdown of Product by sub-components and average profit margin |
9 | Disruptive innovation in the Industry |
10 | Technology trends in the Industry |
11 | Consumer trends in the industry |
12 | Recent Production Milestones |
13 | Component Manufacturing in US, EU and China |
14 | COVID-19 impact on overall market |
15 | COVID-19 impact on Production of components |
16 | COVID-19 impact on Point of sale |
17 | Market Segmentation, Dynamics and Forecast by Geography, 2024-2030 |
18 | Market Segmentation, Dynamics and Forecast by Product Type, 2024-2030 |
19 | Market Segmentation, Dynamics and Forecast by Application, 2024-2030 |
20 | Market Segmentation, Dynamics and Forecast by End use, 2024-2030 |
21 | Product installation rate by OEM, 2023 |
22 | Incline/Decline in Average B-2-B selling price in past 5 years |
23 | Competition from substitute products |
24 | Gross margin and average profitability of suppliers |
25 | New product development in past 12 months |
26 | M&A in past 12 months |
27 | Growth strategy of leading players |
28 | Market share of vendors, 2023 |
29 | Company Profiles |
30 | Unmet needs and opportunity for new suppliers |
31 | Conclusion |
32 | Appendix |