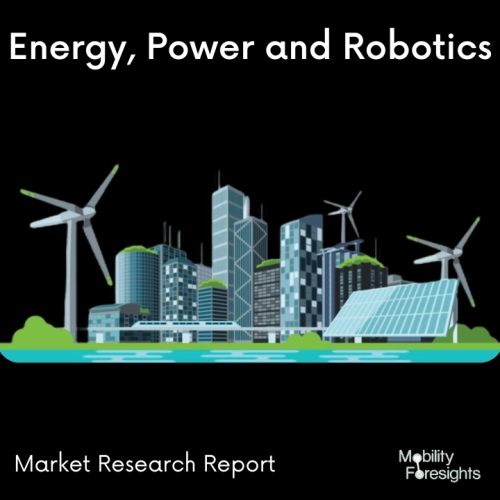
- Get in Touch with Us
Last Updated: Apr 26, 2025 | Study Period: 2023-2030
A power plant inspection system is an automated system used by plant operators, supervisors, and safety engineers to help ensure that all power plant equipment is functioning properly and safely.
This system can be used to identify potential problems, monitor and control the operation of the plant, and provide feedback on the condition of the plant.
The power plant inspection system is designed to detect any signs of wear and tear that may lead to safety risks or malfunctions in the power plant.
By using sensors and advanced monitoring technology, the system can detect mechanical and electrical faults in the plant and alert the operators if something is wrong.
With the help of this system, the operators can respond quickly and take the necessary actions to ensure the safety of the plant and the people who work around it.
The power plant inspection system also helps to ensure that all safety protocols are followed correctly. It can monitor the operation of the plant and alert the operator if any safety regulations are not being followed.
This helps to ensure that the plant is operating safely and that the workers are not exposed to any unnecessary risks.
The power plant inspection system is a valuable tool for plant operators and safety engineers. It can help to identify potential problems, monitor the operation of the plant, and provide feedback on the condition of the plant.
By using this system, operators can ensure that the plant is operating safely and that the people who work around it are not exposed to any unnecessary risks.
The Global Power plant inspection system market accounted for $XX Billion in 2022 and is anticipated to reach $XX Billion by 2030, registering a CAGR of XX% from 2023 to 2030.
Toshiba Energy Systems & Solutions Corporation, also known as Toshiba ESS, declared that it is launching its inspection robot services for turbine generatorsâwhich are used in power plantsâon a large scale.After making advancements, the company now provides a range of two types of inspection robots:
"ultra-thin robots," which are suitable for both small and medium-to-big generators, and "multi-functional robots," which are able to get past baffles and perform a variety of inspections for both domestic and foreign power plants.
The multi-functional robots will perform inspection services in Japan, while the ultra-thin robots, which have previously been utilised on a full-scale basis at a few foreign nuclear power plants, will do so as well.
In order to perform precise inspections of the turbine generators, specialised inspectors used to remove the rotors from the stators every four years. However, in order to increase the power plants' operating rates, it is now necessary to shorten the inspection periods and extend the generators' inspection cycles, as well as to perform high-precision inspections quickly.
Robotic inspection methods have been developed recently for generators; nevertheless, baffles attached to stators have made robotic examinations of generators with them difficult.
Due to their three arms extending from the stator side and their ability to run by pushing against the rotor, these multifunctional robots have made it possible to conduct robot inspections of generators with baffles.
With the help of these robots, Toshiba ESS hopes to increase customer profits by expanding its thermal and nuclear power plant maintenance service business and fortifying its maintenance service business for already-existing power plants throughout the world, including Europe, North America, Southeast Asia, and Japan
.Inspections of small generators, which were previously challenging to inspect, are now possible thanks to a thin-type inspection robot created by Toshiba ESS. The incredibly thin robots can be used with generators without baffles and move via magnetic attraction on the stator core's surface. With a frame thickness of 10 mm (not including protrusions), these very thin robots are among the thinnest in the industry.
Sl no | Topic |
1 | Market Segmentation |
2 | Scope of the report |
3 | Abbreviations |
4 | Research Methodology |
5 | Executive Summary |
6 | Introduction |
7 | Insights from Industry stakeholders |
8 | Cost breakdown of Product by sub-components and average profit margin |
9 | Disruptive innovation in the Industry |
10 | Technology trends in the Industry |
11 | Consumer trends in the industry |
12 | Recent Production Milestones |
13 | Component Manufacturing in US, EU and China |
14 | COVID-19 impact on overall market |
15 | COVID-19 impact on Production of components |
16 | COVID-19 impact on Point of sale |
17 | Market Segmentation, Dynamics and Forecast by Geography, 2023-2030 |
18 | Market Segmentation, Dynamics and Forecast by Product Type, 2023-2030 |
19 | Market Segmentation, Dynamics and Forecast by Application, 2023-2030 |
20 | Market Segmentation, Dynamics and Forecast by End use, 2023-2030 |
21 | Product installation rate by OEM, 2023 |
22 | Incline/Decline in Average B-2-B selling price in past 5 years |
23 | Competition from substitute products |
24 | Gross margin and average profitability of suppliers |
25 | New product development in past 12 months |
26 | M&A in past 12 months |
27 | Growth strategy of leading players |
28 | Market share of vendors, 2023 |
29 | Company Profiles |
30 | Unmet needs and opportunity for new suppliers |
31 | Conclusion |
32 | Appendix |