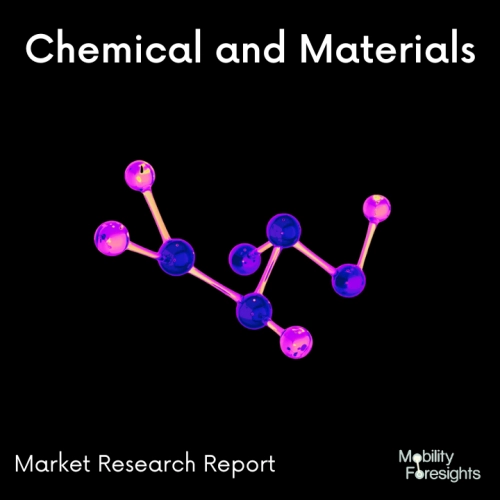
- Get in Touch with Us
Last Updated: Apr 25, 2025 | Study Period: 2024-2030
High-performance engineering thermoplastic polyphenylene sulphone (PPS) is distinguished by an uncommon mix of characteristics. These characteristics include outstanding electrical insulating qualities, dimensional stability, and high-temperature performance.
Motor insulation keeps the windings and the winding to earth from connecting. It's crucial to comprehend how insulation works and how it's used in real life while looking at motors. Currently, electrical motor insulation falls into one of four categories: A, B, F, or H. (although there are also classes N, R and S).
B, F, and H are the two most frequently used among these four. Following the rewinding of an electric motor, insulation is a required step.
The motor windings are shielded from electrical shorts and pollution by this insulation, which also strengthens and secures the windings mechanically. Insulation also dissipates the heat produced by the windings.
Excellent electrical insulating qualities can be found in PPS. After being exposed to high-humidity settings, the high-volume resistivity and insulation resistance are both still present. It may easily be doped to obtain high conductivity and has a less obvious O2 sensitivity.
A semi-crystalline, high-temperature engineering thermoplastic is polyphenylene sulphone (PPS). It has a high melting point (280°C), is stiff, and is opaque.
It may compete favorably in terms of characteristics with PTFE, PEEK, and even PI (Polyimide). It is a nice compromise between PTFE and PEEK in terms of price because it falls between the two.
The global PPS Motor insulator market accounted for $XX Billion in 2023 and is anticipated to reach $XX Billion by 2030, registering a CAGR of XX% from 2024 to 2030.
According to Toray Industries (Tokyo), a Japanese resin supplier, the average gasoline-powered motor vehicle produced in Japan uses 1-2 kg of polyphenylene sulphone (PPS), whereas the utilization of PPS for electric vehicles (EVs) soars to more than 5 kg.
In contrast, hybrid electric vehicles (HEVs) typically use between 4-5 kg of PPS. In drive train parts including inverters, condensers, and motor insulation, PPS is frequently used. PPS resin is in high demand for drive-train applications in Japanese hybrid automobiles.
Sl no | Topic |
1 | Market Segmentation |
2 | Scope of the report |
3 | Abbreviations |
4 | Research Methodology |
5 | Executive Summary |
6 | Introduction |
7 | Insights from Industry stakeholders |
8 | Cost breakdown of Product by sub-components and average profit margin |
9 | Disruptive innovation in the Industry |
10 | Technology trends in the Industry |
11 | Consumer trends in the industry |
12 | Recent Production Milestones |
13 | Component Manufacturing in US, EU and China |
14 | COVID-19 impact on overall market |
15 | COVID-19 impact on Production of components |
16 | COVID-19 impact on Point of sale |
17 | Market Segmentation, Dynamics and Forecast by Geography, 2024-2030 |
18 | Market Segmentation, Dynamics and Forecast by Product Type, 2024-2030 |
19 | Market Segmentation, Dynamics and Forecast by Application, 2024-2030 |
20 | Market Segmentation, Dynamics and Forecast by End use, 2024-2030 |
21 | Product installation rate by OEM, 2023 |
22 | Incline/Decline in Average B-2-B selling price in past 5 years |
23 | Competition from substitute products |
24 | Gross margin and average profitability of suppliers |
25 | New product development in past 12 months |
26 | M&A in past 12 months |
27 | Growth strategy of leading players |
28 | Market share of vendors, 2023 |
29 | Company Profiles |
30 | Unmet needs and opportunity for new suppliers |
31 | Conclusion |
32 | Appendix |