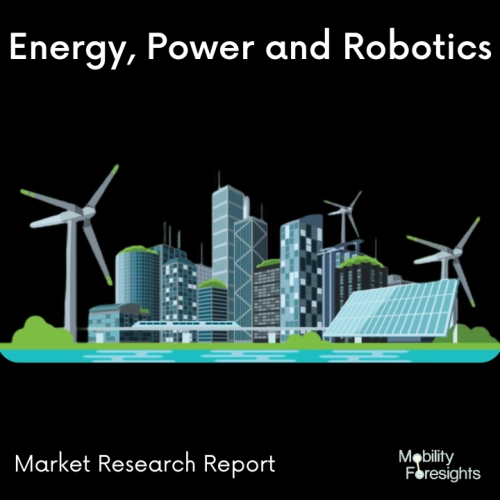
- Get in Touch with Us
Last Updated: Apr 25, 2025 | Study Period: 2024-2030
Precision cutting tools are used to remove materials from a workpiece and are sometimes referred to as cutting tools or simply cutters. A single-point or multi-point tool is used to cut things.
Shape-making, planning, and turning are all done with single-point cutting tools. Drilling and milling are both done with multi-point cutting instruments.
Cutting tools should be constructed from a substance that is more durable and robust than the workpiece that will be cut. Precision tools must also be able to withstand the intense heat produced during the metal-cutting operation.
This is crucial to make sure that the cutting edge can easily engage with the workpiece and contribute to cutting efficiency, making it possible to remove the material from the workpiece with ease.
Precision cutting tools are classified into two categories: rotary precision cutting tools and Linear precision cutting tools.
High-precision linear modules from Bosch Rexroth's R4100 series are created with a focus on providing outstanding performance in applications with constrained space.
These small modules combine rigidity and low weight construction with an integrated ball screw drive and a strong aluminum design.
Precision and speed are excellently delivered by the R4100 series without sacrificing performance.
The R4100 series is the perfect option for applications where installation space is constrained or needs to be maximized because to its compact form.
Manufacturers can effectively use existing space while still attaining high-precision linear motion by reducing the linear module's footprint. Greater flexibility in system design and integration is made possible by its compactness.
The integrated ball screw drive is one of the distinguishing characteristics of the R4100 series. By turning rotational motion into linear motion, the ball screw drive mechanism produces accurate and effective linear motion.
This drive system is appropriate for applications that call for high degrees of precision because it ensures smooth and precise placement. The total complexity of the system is decreased and installation is made simpler by the incorporation of the ball screw drive within the linear module.
The R4100 series is built with a sturdy aluminum profile, which has a number of benefits. Excellent structural integrity is provided by aluminum while still keeping a lightweight design.
This stiffness and light weight combination enables high-speed operation without compromising accuracy
The linear module will last a long time and be reliable in a variety of situations thanks to the aluminum profile's strong corrosion resistance.
High-quality linear guides are a feature of the R4100 series, enabling precise and fluid movement. These linear guides have been meticulously designed to reduce friction and offer the best load-carrying capacity.
The linear module may now achieve precise positioning and repetition thanks to improved performance and precision.
The R4100 series also provides a variety of options and configurations to satisfy the needs of varied application requirements.
Users can adapt the linear module to their needs by choosing from a variety of stroke lengths, load capacities, and motor mounting options. The R4100 series may be readily incorporated into a variety of automation and motion control systems thanks to its flexibility.
It is simple to integrate the R4100 series with other parts, including motors, controllers, and position measuring systems.
This makes it possible for manufacturers to provide thorough motion control solutions that are customized for each individual application.
It is possible to precisely and effectively regulate linear motion thanks to the interoperability with several motor options, including servo and stepper motors.
The R4100 series can be used for a variety of high-precision jobs, such as pick-and-place procedures, laboratory automation, and tiny assembly systems.
The R4100 series' small size and outstanding dynamic performance allow for precise and effective operation in these demanding applications.
The R4100 series of high-precision linear modules from Bosch Rexroth features an integrated ball screw drive, a sturdy aluminum construction, and a compact design.
These modules offer outstanding speed and precision, making them suitable for applications with constrained space.
The R4100 series is a fantastic option for manufacturers wishing to achieve dependable and accurate linear motion in a small form factor thanks to their adaptability and high-performance characteristics.
The global precision cutting tools market accounted for $XX Billion in 2022 and is anticipated to reach $XX Billion by 2030, registering a CAGR of XX% from 2024 to 2030.
Two new microdrill families from Sandvik Coromant have been introduced, both of which are intended for precision machining. Industries that require the production of small parts are supported by the CoroDrill 462 with -XM geometry and the CoroDrill 862 with -GM geometry.
The CBN grade WBH30 from Walter has been developed for hard turning in interrupted cuts.
The new Tri-Bore multipurpose hole saw from Ideal Industries has three sets of tungsten carbide teeth for extremely forceful cutting operation.
Sensor-Based Control of Cutting Tools, Machine Tools Moves From Drawing Board to Mainstream.The proliferation of more and better sensors in machining centres, and even in cutting tools, is a critical success factor for Industry 4.0 and IIoT (Industrial Internet of Things) programs.
These sensors provide the data and connectivity that form the basis of the "factory of the future."But a variety of "smart sensors" are already in use; they collect data and inform operators on the condition of their machines and the metal-cutting procedure, so they are far from futuristic.
The progression is accomplished by increasing the precision with which the part's location, the finished part's geometrical form, and the setup and management of the process's tools are measured.
A variety of industry experts were consulted by Manufacturing Engineering to evaluate the state of sensor-based cutting control systems now and to look into the future to assist spot potential prospects.A boring tool that automatically adjusts for cutting edge wear is one of these innovations.
No matter how advanced a CNC machine tool is, it cannot automatically make up for a boring tool's cutting edge wear. The ActiveEdge tool automates the in-process scaling of boring tool cutting edges. It is battery-operated.
It optimises process performance and does it without requiring human participation by using wireless technology to remotely modify numerous cutting edge diameters on a single tool.
The assembly and software system for the BadAxe Smart Tool is breaking new ground in the milling industry. According to the startup, BadAxe uses physics instead of trial and error to launch a machine into its "sweet spot" right away.
The company's unique algorithms and analytics determine the ideal stability zone for the machine to operate in using measurements of the resident vibration frequency patterns for a particular configuration of machine, spindle, toolholder, and tool.
The outcome is a toolholder and tool that are off-the-shelf, pre-balanced, and assembled, as well as a software interface tailored for particular machines.
Everyone is aware that vibration and chatter are significant machining limitations.The ideal feed, speed, cut breadth, and cut depth are typically discovered by trial and error by operators.
In many instances, they believe they have reached the performance limit when, in fact, chatter-free operation would be found in a system that goes against logic and has significantly greater metal removal rates.
In spite of step-over, complete slot cutting, or corners, the gadget defines that setup from the moment it starts operating. Organisations like Boeing Phantom Works, the US Department of Defense, and others have established that the underlying technology greatly raises a job's return on investment (ROI).
A sizable database for various machine and assembly combinations is being built by BadAxe. A one-time test can be performed to ascertain the setup dynamics of a customer's computer if it is not included in the database.
With the release of its SilentTools+ intelligent cutting tools, Sandvik Coromant is transitioning from in-process to in-tool sensors. Damped tooling solutions like SilentTools+ offer tremendous insight into long-overhang machining processes, when operators are often operating in the dark.
1 | Market Segmentation |
2 | Scope of the report |
3 | Abbreviations |
4 | Research Methodology |
5 | Executive Summary |
6 | Introduction |
7 | Insights from Industry stakeholders |
8 | Cost breakdown of Product by sub-components and average profit margin |
9 | Disruptive innovation in theIndustry |
10 | Technology trends in the Industry |
11 | Consumer trends in the industry |
12 | Recent Production Milestones |
13 | Component Manufacturing in US, EU and China |
14 | COVID-19 impact on overall market |
15 | COVID-19 impact on Production of components |
16 | COVID-19 impact on Point of sale |
17 | Market Segmentation, Dynamics and Forecast by Geography, 2024-2030 |
18 | Market Segmentation, Dynamics and Forecast by Product Type, 2024-2030 |
19 | Market Segmentation, Dynamics and Forecast by Application, 2024-2030 |
20 | Market Segmentation, Dynamics and Forecast by End use, 2024-2030 |
21 | Product installation rate by OEM, 2023 |
22 | Incline/Decline in Average B-2-B selling price in past 5 years |
23 | Competition from substitute products |
24 | Gross margin and average profitability of suppliers |
25 | New product development in past 12 months |
26 | M&A in past 12 months |
27 | Growth strategy of leading players |
28 | Market share of vendors, 2023 |
29 | Company Profiles |
30 | Unmet needs and opportunity for new suppliers |
31 | Conclusion |
32 | Appendix |