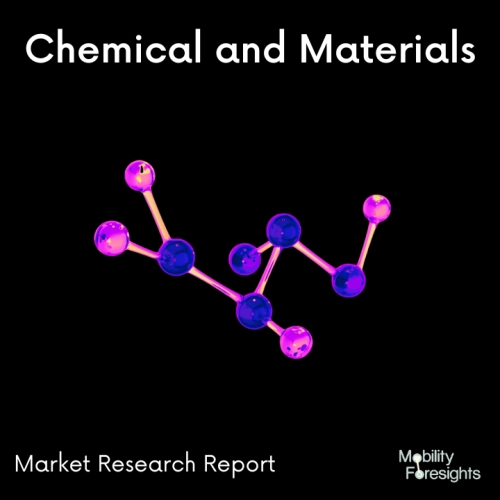
- Get in Touch with Us
Last Updated: Apr 25, 2025 | Study Period: 2023-2030
Precision medical injection molding is a process used to manufacture medical parts and components with high accuracy and repeatability.This process is commonly used for components such as syringes, needles, catheters, and other medical devices. Injection molding is a cost-effective and efficient way to produce a variety of medical parts.
The injection molding process involves pushing molten plastic into a mold to form the desired shape. A mold is created with a design that is specific to the desired medical device.
The process begins with pellets of plastic resin being heated in a barrel and then forced into the mold under pressure. The plastic is then cooled and the part is ejected from the mold. This process is highly repeatable and can produce a large number of parts with an extremely high level of precision.
The advantages of precision medical injection molding are numerous. It is a cost-effective way to produce a large number of parts with exact specifications. The process is also very repeatable, meaning that parts can be precisely reproduced time after time.
In addition, injection molding is a fast process, allowing for a high production rate with minimal labor. The disadvantages of precision medical injection molding include the cost of the molds, which can be expensive.
The Global precision medical injection molding machine market accounted for $XX Billion in 2022 and is anticipated to reach $XX Billion by 2030, registering a CAGR of XX% from 2023 to 2030.
Nissei's All-Electric Injection Molding Machines provide high-precision, high-performance, high-speed injection molding solutions.
Their machines incorporate advanced technologies such as hybrid servo control, nozzle-touch clamping, and active mold temperature control, allowing them to produce sophisticated products with exceptional accuracy and repeatability.
Additionally, Their machines are designed for high-speed operation and easy maintenance, providing a seamless, total solution for your production needs.
The Nissei Plastic Industrial Co., Ltd. precision medical injection molding machine is a high-performance, energy-efficient injection molding machine that is specifically designed for the medical industry.
It features an advanced injection unit design that provides superior injection performance and improved cycle times. The injection unit also features a high-precision mold clamping mechanism that reduces the time required for mold clamping and increases the accuracy of the molding process.
The machine is equipped with an integrated automation system that provides fast, efficient production with minimal operator intervention. The medical injection molding machine is also equipped with safety features that ensure the safety of the operators and the quality of the parts produced.
Medical injection molding machines play a critical role in the healthcare industry, enabling the production of essential medical devices and components with precision and efficiency. In recent times, several partnerships have emerged that highlight the collaborative efforts to advance medical injection molding technology.
Husky Injection Molding Systems and Cavity Eye: Husky Injection Molding Systems, a leading provider of injection molding equipment and services, partnered with Cavity Eye, a medical device technology company.
This collaboration aims to enhance quality control and automation in medical injection molding. Cavity Eye's innovative cavity pressure-based inspection system integrates with Husky's machines to monitor and analyze the injection molding process in real-time.
By detecting defects and variations during production, the partnership ensures the production of high-quality medical components, reducing waste and improving patient safety.
Engel Austria and Hack Formenbau: Engel Austria, a pioneer in injection molding machinery, joined forces with Hack Formenbau, a specialist in mold making. This partnership focuses on advancing mold technology for medical applications.
By combining Engel's expertise in machinery with Hack Formenbau's mold design capabilities, the partnership aims to develop molds that cater to the complex and intricate requirements of medical device manufacturing.
This collaboration contributes to the production of intricate and precise medical components, such as microfluidic devices and surgical instruments.Milacron and Kumovis: Milacron, a global leader in plastics technology and processing, partnered with Kumovis, a startup specializing in 3D printing of medical implants.
This collaboration seeks to integrate 3D printing and injection molding technologies to produce personalized medical implants and devices. By combining Milacron's injection molding machines with Kumovis' 3D printing expertise, the partnership aims to create a hybrid manufacturing approach.
This approach allows for the production of patient-specific implants with the benefits of both additive manufacturing and injection molding, revolutionizing the field of medical implantology.
Sumitomo (SHI) Demag and RJG: Sumitomo (SHI) Demag, a global manufacturer of injection molding machinery, partnered with RJG, a company specializing in injection molding process monitoring and control systems.
This collaboration focuses on advancing the smart manufacturing capabilities of medical injection molding machines. By integrating RJG's sensor technology and process control systems into Sumitomo (SHI) Demag's machines, the partnership enables real-time monitoring and optimization of the injection molding process.
This results in improved product quality, reduced cycle times, and enhanced efficiency, making it particularly beneficial for the production of high-precision medical components.
Sl no | Topic |
1 | Market Segmentation |
2 | Scope of the report |
3 | Abbreviations |
4 | Research Methodology |
5 | Executive Summary |
6 | Introduction |
7 | Insights from Industry stakeholders |
8 | Cost breakdown of Product by sub-components and average profit margin |
9 | Disruptive innovation in the Industry |
10 | Technology trends in the Industry |
11 | Consumer trends in the industry |
12 | Recent Production Milestones |
13 | Component Manufacturing in US, EU and China |
14 | COVID-19 impact on overall market |
15 | COVID-19 impact on Production of components |
16 | COVID-19 impact on Point of sale |
17 | Market Segmentation, Dynamics and Forecast by Geography, 2023-2030 |
18 | Market Segmentation, Dynamics and Forecast by Product Type, 2023-2030 |
19 | Market Segmentation, Dynamics and Forecast by Application, 2023-2030 |
20 | Market Segmentation, Dynamics and Forecast by End use, 2023-2030 |
21 | Product installation rate by OEM, 2023 |
22 | Incline/Decline in Average B-2-B selling price in past 5 years |
23 | Competition from substitute products |
24 | Gross margin and average profitability of suppliers |
25 | New product development in past 12 months |
26 | M&A in past 12 months |
27 | Growth strategy of leading players |
28 | Market share of vendors, 2023 |
29 | Company Profiles |
30 | Unmet needs and opportunity for new suppliers |
31 | Conclusion |
32 | Appendix |