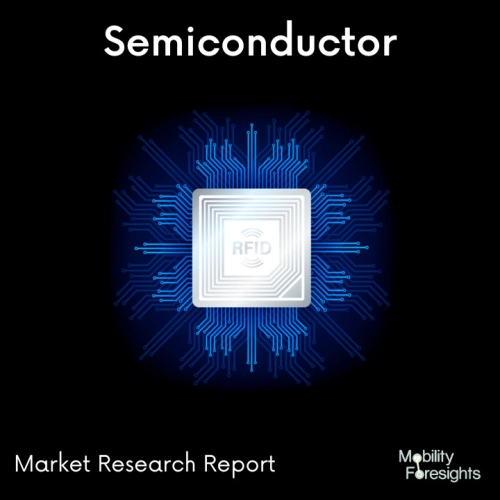
- Get in Touch with Us
Last Updated: Apr 25, 2025 | Study Period: 2024-2030
In order to replace or alter the naturally occurring film of aluminium oxide, the pretreatment can be either a chemical or an electrolytic procedure. The chemical method is more common, with several iterations for uses in architecture or transportation as well as food packaging (to satisfy laws).
Performance is therefore influenced by both the chemistry and the structure of the pretreatment layer. The success or failure of the finished product may depend on achieving the proper structure.
A minor but crucial piece in a multibillion-dollar industry, aluminium pretreatment is. However, the demands on pretreatment surfaces have increased significantly in the twenty-first century due to industry standards for failure minimization and control, as well as increased competitiveness and faster production rates.
After the metal has been cleaned of any film, oil, etc., the pretreatment solution is next applied. Aluminum may be protected from corrosion and has its surface ready for coatings after pretreatment. This preparation will improve any subsequent paint or powder coating and aid in their greater aluminium adhesion.
TheGlobal pretreated aluminum marketaccounted for $XX Billion in 2023 and is anticipated to reach $XX Billion by 2030, registering a CAGR of XX% from 2024 to 2030.
aluminium before treatment
The cleaning of the strip that comes before and the coating that comes after are frequently linked with the preparation of the aluminium.
In order to replace or alter the naturally occurring film of aluminium oxide, the pretreatment can be either a chemical or an electrolytic procedure. The chemical method is more common, with several iterations for uses in architecture or transportation as well as food packaging (to satisfy laws).
Historically, formulations based on chromium (VI) offered excellent performance as pretreatments for coil-coated aluminum. But because chromium (VI) is toxic, significant effort has been made to create more environmentally and health-friendly alternative pre-treatments.
The pretreatment is typically a no-rinse chrome chemical type and is roller coated onto both sides of the strip. Pretreatment typically amounts to 120 mg/m2 dry coating weight. Drying the pretreatment typically involves heating the strip in a hot air oven until the metal reaches a temperature of between 40 and 60 °C.
Effective anodizing in a hot electrolyte using liquid contacts is a different electrolytic pretreatment method. A cell is divided into two or more compartments, with electrodes in each compartment, and contains an electrolyte (for example, 20% sulfuric acid).
Sl no | Topic |
1 | Market Segmentation |
2 | Scope of the report |
3 | Abbreviations |
4 | Research Methodology |
5 | Executive Summary |
6 | Introduction |
7 | Insights from Industry stakeholders |
8 | Cost breakdown of Product by sub-components and average profit margin |
9 | Disruptive innovation in the Industry |
10 | Technology trends in the Industry |
11 | Consumer trends in the industry |
12 | Recent Production Milestones |
13 | Component Manufacturing in US, EU and China |
14 | COVID-19 impact on overall market |
15 | COVID-19 impact on Production of components |
16 | COVID-19 impact on Point of sale |
17 | Market Segmentation, Dynamics and Forecast by Geography, 2024-2030 |
18 | Market Segmentation, Dynamics and Forecast by Product Type, 2024-2030 |
19 | Market Segmentation, Dynamics and Forecast by Application, 2024-2030 |
20 | Market Segmentation, Dynamics and Forecast by End use, 2024-2030 |
21 | Product installation rate by OEM, 2023 |
22 | Incline/Decline in Average B-2-B selling price in past 5 years |
23 | Competition from substitute products |
24 | Gross margin and average profitability of suppliers |
25 | New product development in past 12 months |
26 | M&A in past 12 months |
27 | Growth strategy of leading players |
28 | Market share of vendors, 2023 |
29 | Company Profiles |
30 | Unmet needs and opportunity for new suppliers |
31 | Conclusion |
32 | Appendix |