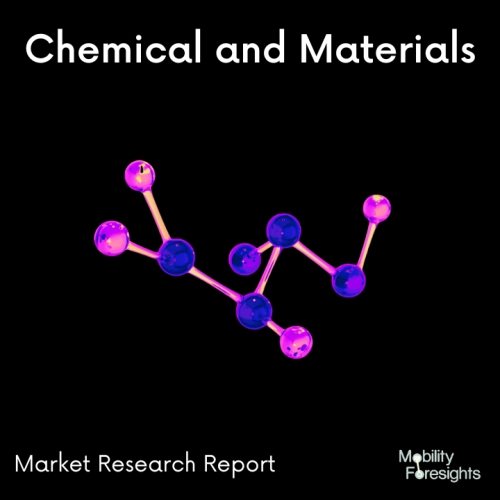
- Get in Touch with Us
Last Updated: Apr 25, 2025 | Study Period: 2024-2030
The thin-film coating technique known as physical vapor deposition (PVD) results in coatings made of pure metals, metallic alloys, and ceramics with a typical thickness of one to ten micrometers.
As its name suggests, physical vapor deposition entails physically depositing atoms, ions, or molecules of a coating species on a substrate.
There are three main types of PVD, all of which are carried out in a controlled atmosphere at a lower pressure in a chamber:
Thermal evaporation, sputtering, and ion plating Heat is used to create a vapor that condenses on a substrate to form the coating in thermal evaporation.
Hot filament, electrical resistance, electron or laser beam, and electric arc are all methods of heating.
The coating species and the substrate create an electrical plasma during sputtering. Sputtering and thermal evaporation are basically combined in ion plating.
Coatings made by PVD can be used for many different things; Ceramic resistors and aluminium tracks for electronic circuitry are two examples.
Against intelligent ceramic coatings for optics; decorative plastic coatings; gas turbine blades with coatings that resist corrosion; and coatings for press and machine tools that prevent wear.
TheGlobal PVD (Physical Vapor Deposition) ceramic coating market accounted for $XX Billion in 2023 and is anticipated to reach $XX Billion by 2030, registering a CAGR of XX% from 2024 to 2030.
The advanced coating architectures of ENDURA coatings offer a variety of PVD (Physical Vapor Deposition) surface characteristics that are not possible just with standard coating treatments.
Full coverage of complex, intricate tooling geometries is made possible through the use of specialised equipment, low-pressure plasma treatments, and sputtering techniques are used.
PVD coatings' primary surface enhancements include exceptional wear and hardness resistance, as well as non-wetting, dry lubrication, low friction, corrosion protection, heat transfer, and thermal oxidation resistance.
Sl no | Topic |
1 | Market Segmentation |
2 | Scope of the report |
3 | Abbreviations |
4 | Research Methodology |
5 | Executive Summary |
6 | Introduction |
7 | Insights from Industry stakeholders |
8 | Cost breakdown of Product by sub-components and average profit margin |
9 | Disruptive innovation in the Industry |
10 | Technology trends in the Industry |
11 | Consumer trends in the industry |
12 | Recent Production Milestones |
13 | Component Manufacturing in US, EU and China |
14 | COVID-19 impact on overall market |
15 | COVID-19 impact on Production of components |
16 | COVID-19 impact on Point of sale |
17 | Market Segmentation, Dynamics and Forecast by Geography, 2024-2030 |
18 | Market Segmentation, Dynamics and Forecast by Product Type, 2024-2030 |
19 | Market Segmentation, Dynamics and Forecast by Application, 2024-2030 |
20 | Market Segmentation, Dynamics and Forecast by End use, 2024-2030 |
21 | Product installation rate by OEM, 2023 |
22 | Incline/Decline in Average B-2-B selling price in past 5 years |
23 | Competition from substitute products |
24 | Gross margin and average profitability of suppliers |
25 | New product development in past 12 months |
26 | M&A in past 12 months |
27 | Growth strategy of leading players |
28 | Market share of vendors, 2023 |
29 | Company Profiles |
30 | Unmet needs and opportunity for new suppliers |
31 | Conclusion |
32 | Appendix |