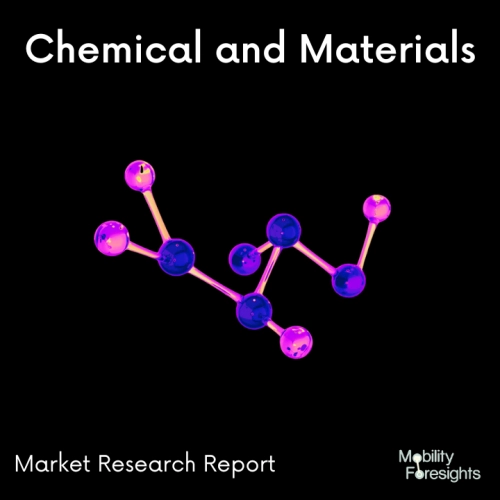
- Get in Touch with Us
Last Updated: Apr 25, 2025 | Study Period: 2024-2030
The term polyvinylidene fluoride, often known as PVF2, is abbreviated as PVDF. This polymer belongs to the group of substances known as fluorocarbons or fluoropolymers, which exhibit strong chemical resistance and high thermal stability.
One of the most popular commercial and industrial coatings on the market is polyvinylidene fluoride (PVDF). An extremely stable and inert fluoropolymer resin known as PVDF offers exceptional protection against metal deterioration over time.
A resin-based coating method is used in PVDF coatings. As a material for paint, PVDF (polyvinylidene difluoride) is a thermoplastic fluoropolymer. Paint made with PVDF resin typically needs to be baked at a high temperature, creating a coating with a rather low gloss.
The Global PVDF resin architectural coatings market accounted for $XX Billion in 2023 and is anticipated to reach $XX Billion by 2030, registering a CAGR of XX% from 2024 to 2030.
Polyvinylidene fluoride (PVDF) resin-based coatings from The Valspar Corporation have been used by building owners, architects, contractors, product manufacturers, and finishers in North America for 50 years. "Although the PVDF resins used in architectural coatings from various manufacturers are similar, the coating systems' performance can differ greatly.
This is a result of each coating manufacturer's unique compositions. Unfortunately, distinguishing between the producers of resins and those of coatings can be difficult for anyone outside the coatings sector.
Although any paint company is theoretically capable of producing a PVDF coating with a 70 percent coverage rate, the knowledge and skill of the paint maker determines the remaining 30% of the pigment and binder.
The new technical analysis, which shares its knowledge in architectural coatings, explains how PVDF resin-based coatings are paired with acrylic's hardness to provide long-lasting, high-performance paint systems that survive the test of time and the elements.
End-uses for architectural coatings made of PVDF resin include providing high-performance durability for things like metal roofing and wall panel systems, curtain wall, window, skylight, and entrance systems, as well as grilles and louvres, soffits, fascia, mullions, and column covers, among other things.
Since their introduction in 1965, Valspar's Fluropon external coatings, which are 70% PVDF resin-based and feature a wide range of colours, have become the industry standard for aluminium extrusion and metal coil coating.
In monumental high-rise constructions and pre-engineered buildings with outside architectural components made of aluminium, galvanised steel and Galvalume coils, and aluminium extrusions, fluropon coatings are best suited for long-life, external use.
Several recent partnerships have emerged within the PVDF resin industry, fostering collaboration and propelling the growth of this versatile material. Arkema, a global specialty chemicals company, and Chang Chun Petrochemical Co. Ltd, a leading chemical manufacturer, entered into a strategic partnership to jointly develop and market PVDF resins.
The collaboration aims to leverage the technological expertise and manufacturing capabilities of both companies to meet the increasing demand for PVDF resins across various industries, including automotive, electronics, and construction.
Solvay, a prominent chemical company, and Kureha Corporation, a Japan-based specialty chemical manufacturer, announced a partnership focused on the development of high-performance PVDF resin solutions.
The collaboration aims to combine Solvay's advanced materials portfolio and technical expertise with Kureha's strong presence in the Asian market. This partnership will enable the companies to offer innovative PVDF resin products tailored to the specific needs of customers in the region.
Daikin Industries, a global leader in air conditioning and refrigeration solutions, partnered with AGC Inc., a leading manufacturer of glass and chemicals, to enhance their respective PVDF resin businesses.
The collaboration aims to leverage Daikin's extensive experience in PVDF production and AGC's strong customer base and global presence to develop advanced PVDF resin solutions for applications such as lithium-ion batteries, industrial coatings, and membranes for water treatment.
Solvay and PolyOne Corporation, a provider of specialized polymer materials and services, formed a strategic partnership to expand the availability of Solvay's PVDF resin products in North America.
The collaboration combines PolyOne's extensive distribution network and market knowledge with Solvay's high-performance materials to meet the growing demand for PVDF resins in various industrial sectors, including oil and gas, chemical processing, and electrical insulation.
Arkema partnered with Kingfa Sci. & Tech. Co., Ltd, a leading Chinese manufacturer of high-performance plastics, to develop and market PVDF resin solutions in China and other Asian markets.
The collaboration aims to combine Arkema's expertise in PVDF technology and Kingfa's strong presence in the Asian market to offer customized PVDF resin products that meet the specific requirements of local customers in industries such as automotive, electrical, and water treatment.
Sl no | Topic |
1 | Market Segmentation |
2 | Scope of the report |
3 | Abbreviations |
4 | Research Methodology |
5 | Executive Summary |
6 | Introduction |
7 | Insights from Industry stakeholders |
8 | Cost breakdown of Product by sub-components and average profit margin |
9 | Disruptive Innovation in the Industry |
10 | Technology Trends in the Industry |
11 | Consumer trends in the industry |
12 | Recent Production Milestones |
13 | Component Manufacturing in the US, EU and China |
14 | COVID-19 impact on overall market |
15 | COVID-19 impact on Production of components |
16 | COVID-19 impact on the point of sale |
17 | Market Segmentation, Dynamics and Forecast by Geography, 2024-2030 |
18 | Market Segmentation, Dynamics and Forecast by Product Type, 2024-2030 |
19 | Market Segmentation, Dynamics and Forecast by Application, 2024-2030 |
20 | Market Segmentation, Dynamics and Forecast by End Use, 2024-2030 |
21 | Product installation rate by OEM, 2023 |
22 | Incline/Decline in Average B-2-B selling price in the past 5 years |
23 | Competition from substitute products |
24 | Gross margin and average profitability of suppliers |
25 | New product development in the past 12 months |
26 | M&A in the past 12 months |
27 | Growth strategy of leading players |
28 | Market share of vendors, 2023 |
29 | Company Profiles |
30 | Unmet needs and opportunities for new suppliers |
31 | Conclusion |
32 | Appendix |