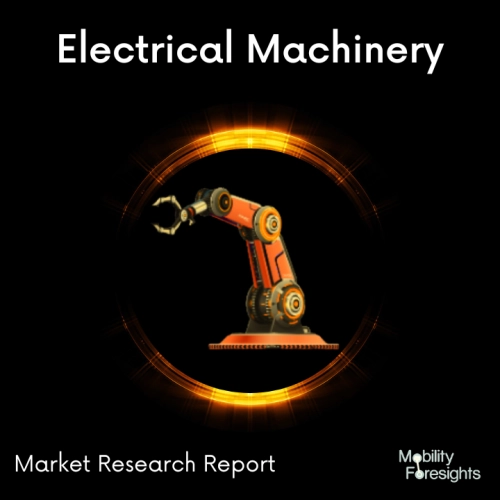
- Get in Touch with Us
Last Updated: Apr 25, 2025 | Study Period: 2023-2030
Grinding removes only a small amount of metal, usually 0.25 to 0.50 mm in depth, and is used to finish workpieces that require a high level of surface quality and precise form and dimension. There are many different sizes, styles, and types of grinder wheels available for use with grinding machines.
A grinding machine is a tool used to alter the shape or size of a hard, typically metallic, body by rotating an abrasive wheel. A grinding wheel consisting of silicon carbide or aluminium oxide is used in all of the various types of grinding machines.
The workpieces are finished with an exceedingly high grade of surface finish and accuracy of shape and dimension using the grinding process. One of the most popular finishing processes is grinding since it produces very fine chips that range in size from 0.25 to 0.50 mm.
A machine called a quartz grinder turns the crystal quartz into a fine powder or paste. Glass, ceramics, and other industrial minerals are frequently made with it. A grinding wheel, a grinding chamber, and a motor that turns the grinding wheel are the typical components of the machine. Depending on the intended use and desired end result, the machine's size and kind may change.
The Global Quartz Grinding Machine market accounted for $XX Billion in 2022 and is anticipated to reach $XX Billion by 2030, registering a CAGR of XX% from 2023 to 2030.
Numerous glass and quartz materials can be ground by Spectrocell to your precise specifications for size, shape, and finishing. They grind materials including black quartz, optical glass, and fused silica using various techniques, including jig and spherical grinding. They are capable of producing pieces with precise tolerances up to a 12" diameter.
They employ surface grinders, jig grinders, OD/ID grinders, and machines for lapping and polishing. For clients in a number of industries, including electronics, medicine, and government, they have created unique glass components.
Sl no | Topic |
1 | Market Segmentation |
2 | Scope of the report |
3 | Abbreviations |
4 | Research Methodology |
5 | Executive Summary |
6 | Introduction |
7 | Insights from Industry stakeholders |
8 | Cost breakdown of Product by sub-components and average profit margin |
9 | Disruptive innovation in the Industry |
10 | Technology trends in the Industry |
11 | Consumer trends in the industry |
12 | Recent Production Milestones |
13 | Component Manufacturing in US, EU and China |
14 | COVID-19 impact on overall market |
15 | COVID-19 impact on Production of components |
16 | COVID-19 impact on Point of sale |
17 | Market Segmentation, Dynamics and Forecast by Geography, 2023-2030 |
18 | Market Segmentation, Dynamics and Forecast by Product Type, 2023-2030 |
19 | Market Segmentation, Dynamics and Forecast by Application, 2023-2030 |
20 | Market Segmentation, Dynamics and Forecast by End use, 2023-2030 |
21 | Product installation rate by OEM, 2023 |
22 | Incline/Decline in Average B-2-B selling price in past 5 years |
23 | Competition from substitute products |
24 | Gross margin and average profitability of suppliers |
25 | New product development in past 12 months |
26 | M&A in past 12 months |
27 | Growth strategy of leading players |
28 | Market share of vendors, 2023 |
29 | Company Profiles |
30 | Unmet needs and opportunity for new suppliers |
31 | Conclusion |
32 | Appendix |