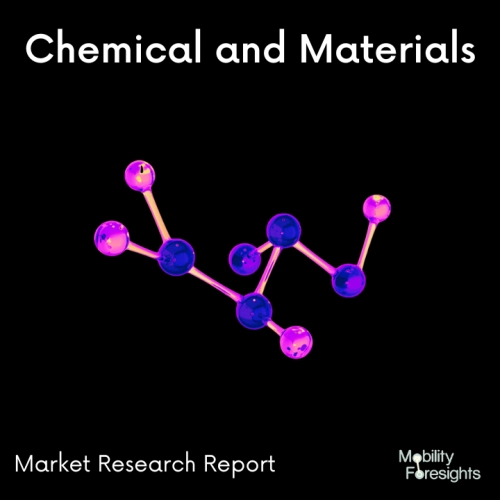
- Get in Touch with Us
Last Updated: Apr 25, 2025 | Study Period: 2024-2030
Quenching is the quick cooling of a workpiece in water, oil, polymer, air, or other fluids to get certain material characteristics in materials science. Quenching, a kind of heat treatment, prevents undesirable low-temperature reactions such as phase transitions from happening.
This is accomplished by narrowing the time frame during which these undesirable events are both thermodynamically favorable and kinetically accessible; for example, quenching can lower the crystal grain size of both metallic and polymeric materials, increasing their hardness.
Quenching is most typically used in metallurgy to harden steel by inducing a martensite transition, in which the steel must be rapidly cooled past the eutectoid point, the temperature at which austenite becomes unstable.
Steel alloyed with metals such as nickel and manganese has a substantially lower eutectoid temperature, but the kinetic barriers to phase change remain the same. This permits quenching to begin at a lower temperature, greatly simplifying the process.
High-speed steel also contains tungsten, which raises kinetic barriers, giving material qualities (hardness and abrasion resistance) as though the workpiece had been cooled faster than it actually was.
Even slowly cooling such alloys in air achieves most of the needed quenching effects; high-speed steel weakens significantly less from heat cycling due to high-speed cutting.
Extremely quick cooling can prevent all crystal structure from forming, resulting in amorphous metal or metallic glass.
Quench hardening is a mechanical process that strengthens and hardens steel and cast iron alloys. These metals are made up of ferrous metals and alloys. This is accomplished by heating the material to a specific temperature, which varies depending on the substance.
This generates a tougher material by either surface hardening or through-hardening, depending on the rate of cooling. The material is then often tempered to decrease brittleness caused by the quench hardening process.
Gears, shafts, and wear blocks are examples of items that can be quenched.Soaking is the second step in the quenching process. Workpieces can be immersed in air, a liquid bath, or a vacuum.
Inert gasses, such as nitrogen and noble gasses, can also be used to quench. Nitrogen is routinely utilized at pressures higher than air, up to bar absolute. Helium is also utilized because it has a higher thermal capacity than nitrogen.
Argon can also be utilized, but its density takes substantially more energy to move and its thermal capacity is lower than the alternatives.
Long cylindrical workpieces are quenched vertically to minimize distortion; flat work pieces are quenched on edge; and thick parts should enter the water first. The bath is stirred to prevent steam bubbles.
Because of an excess of martensite, an iron or steel alloy will frequently be abnormally hard and brittle after quenching. Another heat treatment procedure is used in these circumstances.
Tempering is generally done after hardening to reduce some of the extra hardness. It is done by heating the metal to a temperature below the critical point for a set amount of time, then cooling it in still air.
A quench press is a mechanism that employs focused pressures to retain a quenched item. These sorts of quench facilities are utilized to keep huge gears and other circular parts round. They are also used to maintain the flatness of saw blades and other flat or plate-shaped items.
Because of the particular construction of the clamps that hold the component, quench presses may quench it while it is being held. Clamps have slots.
The Global Quenching Fluids & Salts Market accounted for $XX Billion in 2022 and is anticipated to reach $XX Billion by 2030, registering a CAGR of XX% from 2024 to 2030.
Salts are the generic term for the substances used in salt bath heat treatment. Actual salts and other required composition components become liquid when heated continually. This type of heat treatment is known as salt bath heat treatment. Salt bath heat treatment has a long history of being utilized to efficiently bring out certain characteristics in metal products.
Metal heat treatment is used in the manufacturing of automobiles, electrical appliances, office appliances, precision machines, airplanes, and atomic energy equipment and components.
Furthermore, due to their various features, salts are frequently used as heat exchange media and chemical reaction media, as well as in optical glass processes, fuel cells, novel energy related materials, and other applications.
Parker Netsushori Kogyo is Japan's leading producer of heat treatment salts, addressing client demands with the technology and development skills it has developed over the years.
The global need for quenching fluids and salts will be driven by rising residential and commercial building activity. In recent years, demand for building materials such as metals and associated components has increased in tandem with the fast expanding construction and real-estate sectors.
Quenching is a key characteristic in metal heat treatment since it helps to provide the necessary metallurgical properties.
The construction industry's expansion will have a beneficial influence on the quenching fluids and salts market in the near future.The North American market for quenching fluids and salts is estimated to be worth millions of dollars. The region's quenching fluids and salts market is being driven by the region's expanding automotive and aerospace industries.