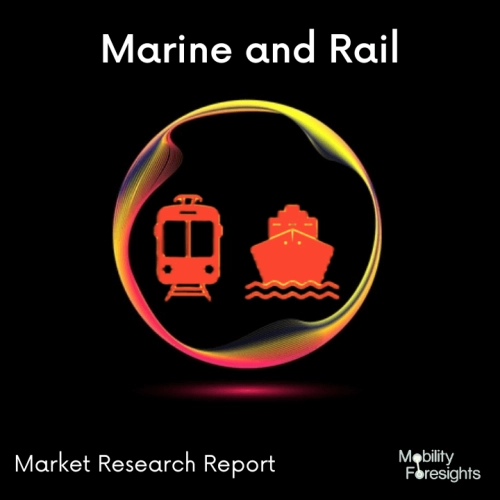
- Get in Touch with Us
Last Updated: Apr 25, 2025 | Study Period: 2024-2030
Railway insulators have very poor conductivity and a very high resistance. Their atoms' electrons are tightly bonded and don't truly move through the substance. Since the electrons are never moving and never wandering freely, no current can flow through it.
By simply focusing the flow of the current, insulators not only prevent the loss of a current but also increase the efficiency of the electric current. The insulators used in railway traction applications must have very high performance, safety, and strength standards.
These types of insulators are often produced in compliance with the requirements and standards established by RDSO, the primary governing organisation.The most basic part of a train track are the rails. They are in charge of dispersing the weight of the cars to the sleepers and are located at the front of the train.
It should have minimal friction and be continuously smooth. Currently, each pair of rails acts as both a signal line for the track circuits and a loop line for locomotive traction in automatic block zones and on electrified trains. As a result, insulation of the rails is necessary to stop interference from stray current. In most cases, insulators and insulated rail joints are used on rail lines.
Thanks to the insulators, the ductile iron shoulder is shielded from wear brought on by direct contact with the rail. They are frequently positioned between the sole plate and the rail. Insulators are subjected to mechanical shocks as a result of vibrations brought on by the frequent movement of trains on the railway lines. Additionally, pantograph action continuously exposes railway insulators to shocks.
The integrity of the insulators is therefore essential to the reliable and safe operation of any overhead electric traction system. On the expanding electrified network of the Indian Railways, there is a growing responsibility to ensure not only the availability but also the dependability of power supply for traction load. When porcelain insulators malfunction for a variety of causes, such as mechanical fracture or flashover, traffic can be disrupted.
The Global Railway Insulator materials market accountedfor $XX Billion in 2023 and is anticipated to reach $XX Billion by 2030, registering a CAGR of XX% from 2024 to 2030.
In order to modify rail gauge and electrically insulate railroad rails, rail clips, and rail bolts from the inside of a concrete sleeper, a rail insulator also known as a railroad insulator, rail insulation, or rail nylon insulator is put between steel rail and tie plate.
Although it is thicker than a rail pad, it serves the same purpose. It is an essential rail fastener for trains travelling at high speeds or carrying heavy loads. In comparison to normal insulators, those used in railway traction applications must meet incredibly demanding performance and safety standards.
Modern insulators have established benchmarks for insulator design, production, testing, and supply for use in railway traction.We produce several different types of 25kV railway insulators to meet every requirement for the electrification of rail lines. These insulators were primarily created to satisfy and even surpass the requirements set by RDSO, the principal regulatory authority for the use of electrical traction insulators.
The manufactured insulator is submitted to acceptability testing as well as normal RDSO tests. The sample size has been expanded primarily to demonstrate the constancy of the product's performance.
Sl no | Topic |
1 | Market Segmentation |
2 | Scope of the report |
3 | Abbreviations |
4 | Research Methodology |
5 | Executive Summary |
6 | Introduction |
7 | Insights from Industry stakeholders |
8 | Cost breakdown of Product by sub-components and average profit margin |
9 | Disruptive innovation in the Industry |
10 | Technology trends in the Industry |
11 | Consumer trends in the industry |
12 | Recent Production Milestones |
13 | Component Manufacturing in US, EU and China |
14 | COVID-19 impact on overall market |
15 | COVID-19 impact on Production of components |
16 | COVID-19 impact on Point of sale |
17 | Market Segmentation, Dynamics and Forecast by Geography, 2024-2030 |
18 | Market Segmentation, Dynamics and Forecast by Product Type, 2024-2030 |
19 | Market Segmentation, Dynamics and Forecast by Application, 2024-2030 |
20 | Market Segmentation, Dynamics and Forecast by End use, 2024-2030 |
21 | Product installation rate by OEM, 2023 |
22 | Incline/Decline in Average B-2-B selling price in past 5 years |
23 | Competition from substitute products |
24 | Gross margin and average profitability of suppliers |
25 | New product development in past 12 months |
26 | M&A in past 12 months |
27 | Growth strategy of leading players |
28 | Market share of vendors, 2023 |
29 | Company Profiles |
30 | Unmet needs and opportunity for new suppliers |
31 | Conclusion |
32 | Appendix |