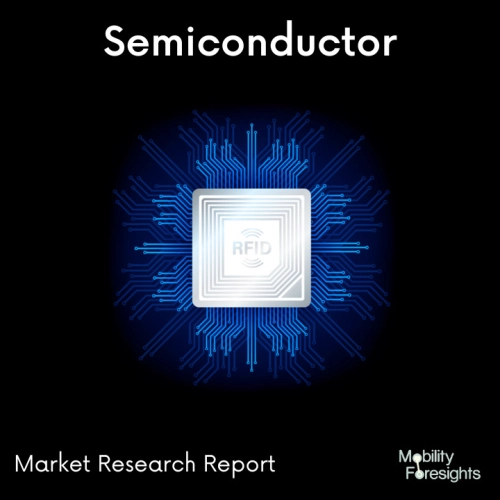
- Get in Touch with Us
Last Updated: Apr 25, 2025 | Study Period: 2024-2030
Rapid Thermal Processing or Rapid Thermal Annealing (RTP/RTA) is a method for producing semiconductors that enables the quick heating of samples to high temperatures for quick operations that can be completed in a matter of minutes at most.
High intensity lights (such near-infrared light sources tungsten-halogen lamps perform such quick heating rates) under the control of pyrometers and thermocouples that gauge the sample temperature. To avoid dislocations and sample breakage, cooling must also be precisely controlled.
RTP creates better silicide's and oxides and decreases the thermal budget/integral of temperature and time, it is more effective than standard furnace annealing. Low manufacturing costs, simple process development, fast throughput, and process homogeneity are other benefits of RTP.
Typically, silicon wafers are processed using an RTP system to create semiconductors for high-speed computing devices and applications.
For large wafer sizes, single wafer processing results in the best consistency. Thermal fabrication processes like chemical vapour deposition, the production of thin dielectric films, and annealing are carried out by RTP systems.Through thermally stimulated diffusion, contaminants are added to the semiconductor during annealing.
The requirements for wafer temperature uniformity vary as a function of operating conditions, hence an RTP system must be able to alter the spatial energy flux distribution radiating to the wafer in order to maintain temperature uniformity in various processing situations.
This requirement can be met by an RTP system, such as the Stanford rapid thermal multiprocessor (RTM), that has many independently controlled concentric circular rings of bulbs.
The power to each of the three lamp zones in the Stanford RTM is controlled automatically in order to maintain a constant temperature over the wafer under both transient and steady-state conditions.
Real-time temperature distribution measurement is provided by the control method using a multi-point sensor reading.
The Global Rapid Thermal Processing System market accountedfor $XX Billion in 2023 and is anticipated to reach $XX Billion by 2030, registering a CAGR of XX% from 2024 to 2030.
Rapid thermal processing (RTP) is a technique that combines wafer annealing with fast ramp rates and quick processing durations to activate dopants with little redistribution.
Rapid thermal annealing (RTA), rapid thermal oxidation (RTO), rapid thermal chemical vapour deposition (RTCVD), and rapid thermal nitration are only a few of the methods that utilise RTP during the production of semiconductor devices (RTN).
Three steps make up a typical RTP operating cycle: a rapid heating phase to quickly reach the desired operating temperature, a constant-temperature processing phase, and a rapid cooling phase to quickly return to room temperature.
For RTP, precise temperature control is essential, but there are a number of issues that need to be solved. One of them is keeping the temperature distribution over the wafer uniform at all times while maintaining rapid temperature trajectories.
The majority of current RTP systems, on the other hand, are not developed with careful consideration of the light flux distributions of the heating sources, and their effects on wafer temperature patterns are not taken into account.
These methods require the RTP system to be built and tested using temperature measurements before the design optimization can be completed.
In order to ensure temperature homogeneity on the wafer, a predictive design strategy for heating sources (a tungsten-halogen lamp array) is preferred.
The relationship between the configuration of tungsten-halogen lamps and the uniformity of the effective irradiance received by the wafer is investigated in this work, and a concentric array of optimized tungsten-halogen lamps is created. The wafer's temperature homogeneity is to be determined using a relative standard deviation-based criterion.
Rapid Thermal Processing was initially created for the annealing of ion implants, but it has since expanded to include oxidation, silicide formation, chemical vapor deposition, and more complex applications like altering the crystallographic phase of elements, compounds, or alloys to improve properties, lattice interface, or stress relaxation.
Sl no | Topic |
1 | Market Segmentation |
2 | Scope of the report |
3 | Abbreviations |
4 | Research Methodology |
5 | Executive Summary |
6 | Introduction |
7 | Insights from Industry stakeholders |
8 | Cost breakdown of Product by sub-components and average profit margin |
9 | Disruptive innovation in the Industry |
10 | Technology trends in the Industry |
11 | Consumer trends in the industry |
12 | Recent Production Milestones |
13 | Component Manufacturing in US, EU and China |
14 | COVID-19 impact on overall market |
15 | COVID-19 impact on Production of components |
16 | COVID-19 impact on Point of sale |
17 | Market Segmentation, Dynamics and Forecast by Geography, 2024-2030 |
18 | Market Segmentation, Dynamics and Forecast by Product Type, 2024-2030 |
19 | Market Segmentation, Dynamics and Forecast by Application, 2024-2030 |
20 | Market Segmentation, Dynamics and Forecast by End use, 2024-2030 |
21 | Product installation rate by OEM, 2023 |
22 | Incline/Decline in Average B-2-B selling price in past 5 years |
23 | Competition from substitute products |
24 | Gross margin and average profitability of suppliers |
25 | New product development in past 12 months |
26 | M&A in past 12 months |
27 | Growth strategy of leading players |
28 | Market share of vendors, 2023 |
29 | Company Profiles |
30 | Unmet needs and opportunity for new suppliers |
31 | Conclusion |
32 | Appendix |