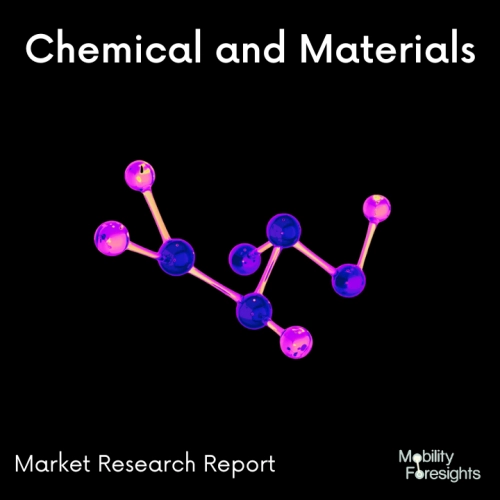
- Get in Touch with Us
Last Updated: Apr 25, 2025 | Study Period: 2024-2030
Recyclable polypropylene foam is a type of foam that is made from polypropylene, a thermoplastic polymer that is used in a variety of applications.It is a lightweight, yet strong material that is also highly resistant to chemicals and temperature extremes. In addition, polypropylene foam is known for its excellent insulation properties and is often used in insulation and cushioning materials.
Unlike other foam materials, polypropylene foam can be recycled. This makes it a great choice for companies that are looking to reduce their environmental footprint and maximise the use of their resources.
The recycling process involves breaking down the foam into small pieces and then reprocessing it into pellets or beads. These pellets or beads can then be used to create new polypropylene foam products.
In addition to its recyclability, polypropylene foam is also a highly versatile material. It can be used in a variety of applications, from insulation to cushioning to packaging.
It is also an economical material, making it an attractive choice for companies looking to save money.Overall, polypropylene foam is an ideal choice for companies looking for a lightweight, strong, and recyclable material.It is versatile, economical, and environmentally friendly, making it an attractive option for a wide range of applications.
The Global recyclable polypropylene foam market accounted for $XX Billion in 2023 and is anticipated to reach $XX Billion by 2030, registering a CAGR of XX% from 2024 to 2030.
With the introduction of foam polypropylene (FPP) food trays, Tekni-Plex Consumer Products is increasing the packaging options available to packers of fresh meat and produce. After a year of development, the trays provide a reusable substitute for the foam polystyrene trays that are commonly used to package fresh commodities like meat.
According to the business, the first customer to employ the FPP trays for meat at retail is a sizable wholesale company. The foam polystyrene (FPS) trays can be easily replaced with foam polypropylene (PP) trays, which are specifically made for fresh food products like meat, chicken, pork, fruits, and vegetables. However, the FPP trays are easily recyclable, in contrast to FPS, which has a weak or nonexistent recycling infrastructure.
Their new FPP trays can be recycled by any curbside or municipal recycling program me that can currently handle PP packaging. FPP will be sorted by the standard PP sorting procedures at materials recovery facilities (MRFs), much like conventional PP resin.
Over the last ten years, there has been an increase in the recycling of polypropylene (PP), despite being the third most popular plastic used for packaging, after HDPE and PET. Being at the forefront of the push to offer novel, substitute material options and goods approved for curbside and municipal recycling program me excites people.
Though Tekni-Plex offers a range of colors for the FPP trays, natural resin or white are the best options as they increase recyclability at MRFs. FPP provides food packers with the advantages of durability, light weight, and heat resistance in addition to enhancing sustainability.
Because PS and PP are such unlike resins, they had to use all of the material science knowledge to modify the production procedure in order to handle this material.
Furthermore, they wanted to provide an FPP processor tray that is just as robust and effective as the FPS trays without requiring any modifications to the clients' equipment. By doing this, they were in a position to provide a substitute for FPS that is in line with sustainability objectives.
Sl no | Topic |
1 | Market Segmentation |
2 | Scope of the report |
3 | Abbreviations |
4 | Research Methodology |
5 | Executive Summary |
6 | Introduction |
7 | Insights from Industry stakeholders |
8 | Cost breakdown of Product by sub-components and average profit margin |
9 | Disruptive innovation in the Industry |
10 | Technology trends in the Industry |
11 | Consumer trends in the industry |
12 | Recent Production Milestones |
13 | Component Manufacturing in US, EU and China |
14 | COVID-19 impact on overall market |
15 | COVID-19 impact on Production of components |
16 | COVID-19 impact on Point of sale |
17 | Market Segmentation, Dynamics and Forecast by Geography, 2024-2030 |
18 | Market Segmentation, Dynamics and Forecast by Product Type, 2024-2030 |
19 | Market Segmentation, Dynamics and Forecast by Application, 2024-2030 |
20 | Market Segmentation, Dynamics and Forecast by End use, 2024-2030 |
21 | Product installation rate by OEM, 2023 |
22 | Incline/Decline in Average B-2-B selling price in past 5 years |
23 | Competition from substitute products |
24 | Gross margin and average profitability of suppliers |
25 | New product development in past 12 months |
26 | M&A in past 12 months |
27 | Growth strategy of leading players |
28 | Market share of vendors, 2023 |
29 | Company Profiles |
30 | Unmet needs and opportunity for new suppliers |
31 | Conclusion |
32 | Appendix |