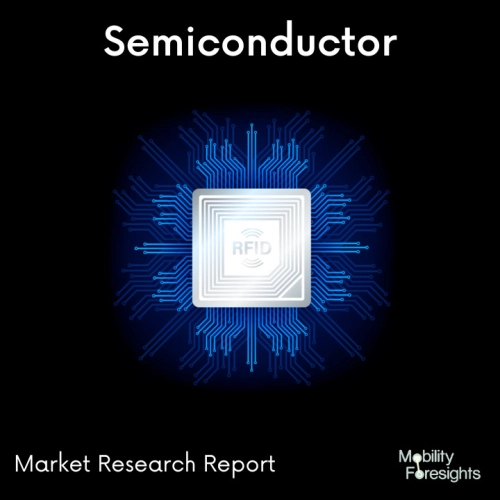
- Get in Touch with Us
Last Updated: May 20, 2025 | Study Period: 2023-2030
A sort of inspection system used in the semiconductor industry to find flaws on photomasks or reticles is called a reticle defect inspection system. On silicon wafers, integrated circuits are created using these master templates.The reticle defect inspection system scans the reticle's surface using cutting-edge optical technology to look for any flaws or imperfections that might impair the final product's quality. The system is capable of identifying flaws including scratches, particles, and pattern distortions.
A high-resolution microscope is often used in the system to take pictures of the reticle surface. A software algorithm then analyses the photographs to find any flaws and classify them based on their seriousness. The operator can then go over the data and photos to see if any adjustments are required.Systems for checking for reticle defects are essential for maintaining the dependability and quality of integrated circuits. Without such technologies, even minor reticle flaws could cause major production problems and yield reductions.
Global reticle defect inspection system market accounted for $XX Billion in 2022 and is anticipated to reach $XX Billion by 2030, registering a CAGR of XX% from 2023 to 2030.
The Teron 640, Teron SL655, and Reticle Decision Center are three cutting-edge reticle inspection systems that KLA-Tencor Corporation unveiled.
The ability to identify lithographically significant and severe yield-damaging errors more quickly allows mask shops and IC fabs to more effectively produce both current and next-generation mask designs.
The Teron 640 inspection system, which makes use of cutting-edge Dual Imaging technology, provides the sensitivity required for mask makers to precisely qualify modern optical masks.
The Teron SL655 inspection system features revolutionary STARlightGold technology, assisting IC makers in evaluating the quality of incoming reticle input, tracking reticle deterioration, and identifying yield-critical reticle flaws. RDC supports the thorough reticle quality measurements generated by the Teron inspectors.
A system for managing and analysing data that offers a wide range of capabilities to drive automated decisions about how to handle defects, speed up production, and lessen yield-reducing patterning errors caused by reticle issues.
Sl no | Topic |
1 | Market Segmentation |
2 | Scope of the report |
3 | Abbreviations |
4 | Research Methodology |
5 | Executive Summary |
6 | Introduction |
7 | Insights from Industry stakeholders |
8 | Cost breakdown of Product by sub-components and average profit margin |
9 | Disruptive innovation in the Industry |
10 | Technology trends in the Industry |
11 | Consumer trends in the industry |
12 | Recent Production Milestones |
13 | Component Manufacturing in US, EU and China |
14 | COVID-19 impact on overall market |
15 | COVID-19 impact on Production of components |
16 | COVID-19 impact on Point of sale |
17 | Market Segmentation, Dynamics and Forecast by Geography, 2023-2030 |
18 | Market Segmentation, Dynamics and Forecast by Product Type, 2023-2030 |
19 | Market Segmentation, Dynamics and Forecast by Application, 2023-2030 |
20 | Market Segmentation, Dynamics and Forecast by End use, 2023-2030 |
21 | Product installation rate by OEM, 2023 |
22 | Incline/Decline in Average B-2-B selling price in past 5 years |
23 | Competition from substitute products |
24 | Gross margin and average profitability of suppliers |
25 | New product development in past 12 months |
26 | M&A in past 12 months |
27 | Growth strategy of leading players |
28 | Market share of vendors, 2023 |
29 | Company Profiles |
30 | Unmet needs and opportunity for new suppliers |
31 | Conclusion |
32 | Appendix |