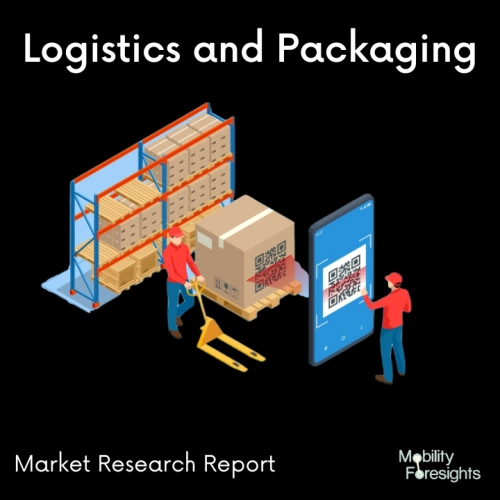
- Get in Touch with Us
Last Updated: Apr 25, 2025 | Study Period: 2024-2030
Reverse logistics is the supply chain activity in moving the goods from consumer or customer to the upstream of supply chain, the objectives of reverse logistics include: Maintenance, Reuse, Refurbish or Recycle of the product.
Reverse logistics helps businesses in efficiently reducing costs, improve asset utilization and help in reduce the waste that reaches landfills. It plays a crucial role in realizing a circular economy, which helps in maximizing the recapture of material and reduces the material that ends up in landfills.
SI.no | Timeline | Developments |
1 | Q4-2021 | The Phoenix Group company received its patent from the United States Patent and Trademark Office for its software as a service product called Midas which is used for reverse logistics operations. |
2 | Q4-2021 | OPEX Logistics from Germany started using automation solutions to manage reverse logistics operations and to manage warehouses. |
3 | Q1-2021 | Amazon introduced its new policy for its customers to deal with reverse logistics issues, which is a returnless refunds service where customers can get a refund for the product but no need to return certain products. |
4 | Q2-2021 | G2 Reverse Logistics built a software to increase efficiency and revenue of returns by analysing the data in artificial intelligence and machine learning. |
5 | Q4-2021 | FedEx entered the Indian market by investing $100 million Delhivery to assist its operations with a long term agreement. FedEx operates international logistics operations from India and Delhivery will assist FedEx by providing services in pickup, deliveries and return of products in India |
6 | Q2-2021 | XPO Logistics provides reverse logistics solutions for France based fashion e-commerce customers to manage return products by automating the warehouse. |
7 | Q2-2021 | Narvar and Cycleon partnered to provide reverse logistics return solutions, Narvar provided technology driven solutions for customers and Cycleon operates full service in return management solutions. |
Some key drivers in reverse logistics market are:
With the ongoing growth of e-commerce, the volume of returned inventory continues to rise for logistics managers in a variety of industry sectors. But arguably, itâs U.S. retailers who have felt the greatest impact in recent years with over $400 billion in goods are returned in any given 12-month time frame.e-commerce sales had a much higher return rate than those of brick-and-mortar storesâbetween 15% and 30%. Look for reverse logistics to be the main reason shippers will continue to search for class B industrial warehouse space in particular.
As of October 2020, in United States in real estate space, 3PLs accounted for 27.1% of the transaction volume for deals of 100,000 sq. ft. or more, compared with 22% for e-commerce occupiers.Key challenge for fashion apparel industry in e-commerce is that, reverse logistics include product value depreciation and time sensitivity. As the overall return rate continues to grow by 10% annually, a higher amount of inventory is subject to depreciation.Apparel depreciates by 20% to 50% of its value within 8 to 16 weeks, creating urgency to get inventory back into circulation and ready for resale.
Most of the companies are inclined to outsource their returns management to third-party logistics (3PL) providers in order to free up space for forward logistics. This has created a significant amount of opportunity for the 3PLs specializing in the reverse loop, including XPO Logistics, Ryder and NFI.Social media impulse purchases are another factor to increase the returns as many companies are increasing their returns policy from 28 days to 45 days to attract more customers.
In US big retail players do use algorithms to decide on the returned items, algorithms suggest them if item sells for new, what it sells for on the secondary market and what generation technology an item is or has.Retailers can then decide if they want to sell it new at full price, sell it at a deep discount, resell it to a discounter, recycle it or liquidate it.
This space is rapidly growing with 3PL competing very hard to grab the reverse logistics market with recent acquisition of Pittsburgh-based GENCO, a third-party logistics (3PL) services provider specializing in product lifecycle and reverse logistics by FedEx shows the focus by 3PLs.
SI.no | Timeline | Company | Developments |
1 | Q3-2021 | FedEx | Walmart partnered with FedEx to pick up its returned items from customers for service called âCarrier Pickup by FedExâ. |
2 | Q4-2021 | Delhivery | Indian based Delhivery startup offers a full suite of logistics services like warehousing, end to end supply chain services, reverse logistics and many more services and also collaborated with FedEx to expand its business. |
3 | Q1-2021 | Kohl | US based retail network Kohl is partnered with Amazon to accept its returned items at its stores without any return cost to the customers. |
4 | Q4-2021 | Returnmates | Returnmates startup from Los Angeles started its services in picking up the return orders from online orders and packages it in a warehouse before handing it to the courier. |
5 | Q3-2021 | United Parcel Services | Stericycle is partnered with United Parcel Services to deal with its medical waste in a reverse logistics process. |
6 | Q3-2021 | GEODIS | GEODIS provides reverse logistics services by using ShopRunBack, a French based startupâs platform to manage returns from consumers. |
It's no longer possible to think about reverse logistics as a stand-alone capacity. As a standard process, it should be effortlessly integrated into the end-to-end supply chain.Reverse logistics encompasses many areas across the organisation, including returns management, sales, finance, warehousing, logistics, recycling management, and environmental compliance, and ranges from product returns to refurbishment and repairs to recycling of packaged materials and disposing of end-of-life products. It's also an important part of the customer experience.
Shippers want efficient reverse logistics to recover value from returned and damaged goods while simultaneously satisfying demands from all stakeholders to reduce environmental impact. Shippers require a revolutionary approach to reverse logistics that includes analytics, process optimization, and changes to the operating model, and that extends across the entire supply chain so that reverse logistics is included into core operations.
In a word, businesses must figure out how to make the returns process more customer-friendly while also considering the total cost of returns and the impact on the environment. Improving data will result in more useful insights. With limited data and analytics capabilities, many shippers have made headway in improving reverse logistics by fine-tuning policy and enhancing process efficiency.
However, in order to get full value, they'll require strong data management and analytics skills to completely change and modernise operations that are now highly manual for most shippers. Furthermore, acquiring and integrating a diverse range of data types from many business domains is a significant problem.Instead of only analysing expenses, new data analytics can assist uncover consumer fraud, reduce the cost-to-serve of returns, and boost the earnings effect of returns.
While many shippers are still focusing on developing internal analytics capabilities and organisations for their core businesses, inventory management, sales, and pricing, third-party solutions can provide tracking and dispositioning capabilities that help unlock reverse logistics value more quickly.The operating model should be updated. Many reverse logistics initiatives fail because shippers fail to consider the operational model adjustments required to enable and sustain effective reverse logistics management. Reverse logistics is inherently cross-functional, involving sales, marketing, merchandising, financing, distribution, and customer service, just as forward logistics does.
Reverse Logistics Technologies created the cutting-edge software program Loop Track to streamline and improve reverse logistics processes. Businesses are realizing the value of successfully managing the reverse flow of products and resources as sustainability and resource efficiency become more and more important.With the entire tool and feature set that Loop Track provides, businesses can improve operational effectiveness, cut costs, and have a minimal negative impact on the environment while addressing the complex difficulties of reverse logistics.
Fundamentally, Loop Track uses automation and smart data analytics to provide users complete insight and control over the whole reverse logistics process. The program seamlessly interfaces with current enterprise systems, allowing firms to quickly handle product recalls, track and trace returned goods, manage processes for repairs and refurbishments, and track and trace returned goods.
Reverse logistics processes are centralized and digitalized via Loop Track, which also speeds up processing and decreases processing times.Its powerful tracking and tracing capabilities are one of Loop Track's standout qualities. A product is given a special identification number when it is returned, allowing for real-time tracking of the product's movement through the reverse logistics pipeline. This enables organizations to precisely trace each returned item's status from the time it enters the system until it is dealt with. Businesses may proactively identify bottlenecks, manage resource allocation, and guarantee prompt customer issue response with this degree of awareness.
Loop Track provides extensive analytics and reporting capabilities in addition to tracking. Businesses can learn important information about the quality of their products, how customers behave, and how well their operations are performing by studying the data gathered during the reverse logistics process.These data-driven insights help firms discover areas for improvement, manage inventories more effectively, and increase the effectiveness of their supply chains as a whole.
Loop Track also includes cutting-edge automation capabilities that let firms automate labor-intensive procedures and minimize human involvement. The program automates crucial processes including product classification, disposition, and sorting, saving logistics staff time and effort. Businesses can reduce operating expenses related to reverse logistics, increase efficiency, and minimize errors by automating these procedures.The integration of Loop Track with workflows for repairs and renovations is another noteworthy feature. The software enables companies to effectively manage the refurbishing and repair of returned goods, ensuring that they are returned to the supply chain in top shape.
Loop Track keeps track of each item's status as it is being repaired, monitors the inventory of replacement parts, and offers real-time visibility into the development of refurbishment activities. Businesses can cut turnaround times, increase product value recovery, and lessen the need for new product manufacturing by optimizing repair procedures.In order to assist product recalls and returns brought on by regulatory compliance or quality issues, Loop Track was also built. Businesses can manage consumer communications, identify impacted products immediately, and streamline the return and replacement process thanks to the software.
Loop Track aids companies in risk mitigation, brand protection, and regulatory compliance by offering a seamless and effective recall management system.Last but not least, Loop Track was developed with sustainability in mind. Businesses may limit waste generation, save shipping costs, and lengthen the lifecycle of items by improving reverse logistics procedures. Loop Track makes it easier for businesses to adopt ethical and sustainable practices by facilitating the application of circular economy ideas.
SI.no | Timeline | Company | Developments |
1 | Q4-2021 | Kohl | Kohl made $1.9 billion in sales revenue in its third quarter with 15% rise from its previous quarter. |
2 | Q1-2021 | ReverseLogix | ReverseLogix startup raised $20 million funding Cambridge Capital in its first round of funding, the company provides its services in e-commerce firms by automating the reverse logistics in cloud based platform. |
3 | Q4-2021 | NFI Industries | NFI Industries is a third party logistics provider announces its third quarters revenue of $492 million. |
4 | Q4-2021 | GXO Logistics | GXO Logistics announced $2 billion earnings in its third quarter results with a rise of 20% from last year's same period. |
5 | Q3-2021 | Delhivery | Delhivery acquired bengaluru based Spoton Logistics for $300 million to maximize its logistics operations across the country. |
Sl no | Topic |
1 | Market Segmentation |
2 | Scope of the report |
3 | Abbreviations |
4 | Research Methodology |
5 | Executive Summary |
6 | Introduction |
7 | Insights from Industry stakeholders |
8 | Cost breakdown of Product by sub-components and average profit margin |
9 | Disruptive innovation in the Industry |
10 | Technology trends in the Industry |
11 | Consumer trends in the industry |
12 | Recent Production Milestones |
13 | Component Manufacturing in US, EU and China |
14 | COVID-19 impact on overall market |
15 | COVID-19 impact on Production of components |
16 | COVID-19 impact on Point of sale |
17 | Market Segmentation, Dynamics and Forecast by Geography, 2024-2030 |
18 | Market Segmentation, Dynamics and Forecast by Product Type, 2024-2030 |
19 | Market Segmentation, Dynamics and Forecast by Application, 2024-2030 |
20 | Market Segmentation, Dynamics and Forecast by End use, 2024-2030 |
21 | Product installation rate by OEM, 2023 |
22 | Incline/Decline in Average B-2-B selling price in past 5 years |
23 | Competition from substitute products |
24 | Gross margin and average profitability of suppliers |
25 | New product development in past 12 months |
26 | M&A in past 12 months |
27 | Growth strategy of leading players |
28 | Market share of vendors, 2023 |
29 | Company Profiles |
30 | Unmet needs and opportunity for new suppliers |
31 | Conclusion |
32 | Appendix |