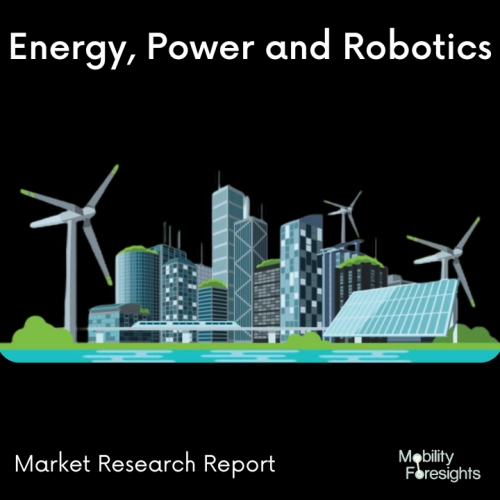
- Get in Touch with Us
Last Updated: Apr 25, 2025 | Study Period: 2023-2030
Robot calibration is the process of locating the precise geometrical parameters that make up an industrial robot's kinematic structure, such as the relative location of its joint linkages. Robot calibration increases the accuracy of robots that are offline-programmed.
Robots, like other mechanical devices, can experience minor changes or drifts owing to wear of parts, dimensional drifts, tolerances, and component replacement. Calibration can reduce the likelihood that minor changes will need changing application programmes.
A calibration sensor is a component of a robot calibration system that indicates when a first reference point, which is fixed in relation to the robot base, is a fixed distance away from a second reference point, which is situated on the robot arm.
Robot joint position information is calculated each time the fixed distance between the two reference points is reached as the robot arm is moved through a variety of orientations.
The preferred calibration sensor consists of a thread that connects the two reference sites and triggers a signal generator whenever the string is pulled taut due to the robot arm's orientation. The generated signal indicates that there is a definite distance separating the two reference sites.
At the most fundamental level, there are two categories for calibrating. Model-based non-parametric calibration and parametric calibration based on models.
The majority of research on model-based parametric calibration has focused on kinematic calibration, also known as model-based calibration or kinematic calibration in this work.
The purpose of this study is to present an overview of robot calibration, to point out the utility of robot calibration, and to identify some of the associated research questions.
This is accomplished by classifying robot calibration into two categories. The sequential steps, modelling, measurement, identification, and compensation are discussed for each kind, and pertinent studies are evaluated.
The Global Robot calibration system market accountedfor $XX Billion in 2022 and is anticipated to reach $XX Billion by 2030, registering a CAGR of XX% from 2023 to 2030.
TwinTool, a piece of software from RoboDK, provides industrial robots with fully automated robot tool calibration. TwinTool is a quick, simple, and affordable way to increase the accuracy of the tool in a variety of manufacturing applications. It is a cost-effective substitute for the pricey and intricate robot calibration services now offered in the market.
For high-accuracy production activities like assembly, soldering, and machining, industrial robots are used more and more. However, new users are occasionally dissatisfied with the seeming lack of precision of their robots and purchase pricey robot calibration equipment in an effort to increase robot accuracy.
With RoboDK, robot calibration may be completed.The offline programming tools provided by RoboDK make it simple to create robot programmes offline once. Software calibration is used to improve robot positioning accuracy rather by altering the robot's mechanical configuration or design.
Sl no | Topic |
1 | Market Segmentation |
2 | Scope of the report |
3 | Abbreviations |
4 | Research Methodology |
5 | Executive Summary |
6 | Introduction |
7 | Insights from Industry stakeholders |
8 | Cost breakdown of Product by sub-components and average profit margin |
9 | Disruptive innovation in the Industry |
10 | Technology trends in the Industry |
11 | Consumer trends in the industry |
12 | Recent Production Milestones |
13 | Component Manufacturing in US, EU and China |
14 | COVID-19 impact on overall market |
15 | COVID-19 impact on Production of components |
16 | COVID-19 impact on Point of sale |
17 | Market Segmentation, Dynamics and Forecast by Geography, 2023-2030 |
18 | Market Segmentation, Dynamics and Forecast by Product Type, 2023-2030 |
19 | Market Segmentation, Dynamics and Forecast by Application, 2023-2030 |
20 | Market Segmentation, Dynamics and Forecast by End use, 2023-2030 |
21 | Product installation rate by OEM, 2023 |
22 | Incline/Decline in Average B-2-B selling price in past 5 years |
23 | Competition from substitute products |
24 | Gross margin and average profitability of suppliers |
25 | New product development in past 12 months |
26 | M&A in past 12 months |
27 | Growth strategy of leading players |
28 | Market share of vendors, 2023 |
29 | Company Profiles |
30 | Unmet needs and opportunity for new suppliers |
31 | Conclusion |
32 | Appendix |