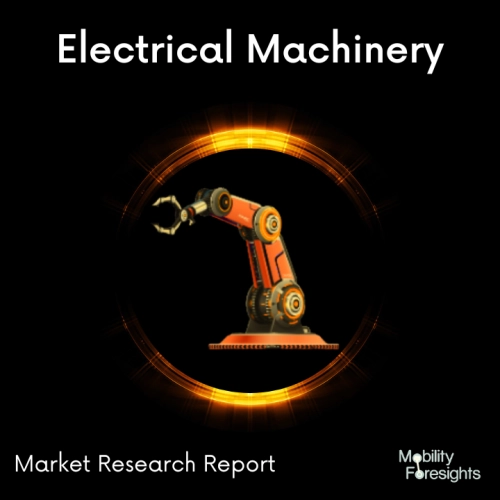
- Get in Touch with Us
Last Updated: Apr 25, 2025 | Study Period: 2024-2030
The counter rotation of two pumping parts (rotors) inside a chamber (rotor case) produces the pumping action of the Rotary Lobe Pump mechanism. The shafts on which the rotors are placed, as well as the timing gears, are supported by bearings and mounted inside an external gearbox.
The timing gears synchronize the rotors so that they spin independently of one another by transferring energy from the drive shaft to the driven shaft. The pressure decrease caused by the increased cavity created when the rotors pass the suction port causes the pumped medium to flow into the rotor case.
The same structural idea guides the design of all rotary lobe and circumferential piston pumps. The support of two displacement elements is provided by an external gearbox.With little radial and axial clearance, the two displacers rotate counterclockwise.
They don't make contact with the surrounding pump casing or one another. Spur gears synchronize the shafts.Because of their design, the displacers can be placed in any position to seal the suction chamber against the pressure chamber.
The gap alone does this sealing; no additional seals or valves are required. The detachable pump cover keeps the pump housing sealed and makes front access simple.
The Global Rotary Lobe Pump market accounted for $XX Billion in 2023 and is anticipated to reach $XX Billion by 2030, registering a CAGR of XX% from 2024 to 2030.
There are 12 different sizes in the Johnson-pump Rotary Lobe Pump series. There are single, double, and lip seal choices for shaft seals. Multiple feet for horizontal or vertical mounting. Front cover heating/cooling systems. As an alternative, built-in safety relief valves.
150 mm to 20 mm connections.Benefits-Construction that is straightforward, tidy, and durable is hygienic, has little risk of product entrapment, is simple to clean using CIP, SIP, or manually, and requires little downtime.Simple gearbox construction and easy servicing and maintenance make upkeep simple.
Product handling that is soft and capable of handling particles is made possible by the traditional tri-lobe design.a wide variety of shaft seals that are quickly interchangeable with different seal types.Oil-lubricated gearbox without shims: easier to maintain, longer lifespan.ATEX Certification CE Certification
Lead-free carbon brushes for automotive starters.Lead has historically been added to carbon brushes for vehicle starters. Increased starting performance without a rise in the copper to current-density ratio, which is directly connected to brush wear rate, is the intended outcome.
Toxic or potentially causing genetic alterations is lead dust, even in minute amounts. The easy oxidation of lead in air also causes the brushes' dimensions and resistivity to alter over time.
Lead's capacity to regulate the film and reduce temperature by dispersing heat through phase change has been linked to its function in the contact.
The criteria of non-toxicity, low melting point, and low oxide hardness are only met by zinc and tin. In order to avoid the additive's total migration into the copper and loss of its essential capabilities as a metal or oxide, tests were conducted, and it turned out that it was required to separate the additive from the copper.
Zinc was converted into a useful form to replace lead using a variety of techniques, and the finished product performs better while having a reduced wear rate.
Low voltage in automotive applications necessitates carbon brushes with extremely low contact resistance, which is especially important for high power starting motors with peak current densities of 1000 A/cm2.
Metal loaded carbon brushes are utilised to attain the desired low resistivity. Metal concentrations ranging from 50-95% are employed, depending on the provided voltage and the kind of starter. The rest is made up of agglomerated graphite and other solid lubricants and abrasives.
Lead's lubricating effect (for example, on intake valves in gasoline engines) is widely known, and it came to public attention when lead was banned as a gasoline additive in the early 1970s. Engine makers had to discover new materials for intake valves at the time. With the restriction on lead in its goods, the carbon brush business is facing a similar lubricating dilemma.
The addition of lead to carbon brushes has various advantages. A substantial proportion of lead boosts the strength and decreases the resistivity of brushes that are heat treated below the sintering temperature of copper. This is because the lead solders the copper particles together.
The mild abrasive effect of lead oxide stabilises the contact drop in high current applications, and lead permits for short-term overcharging of the contact, which is an important feature for starter applications. However, lead oxidation within the brush material can cause fractures and increased resistance over time.
Lead's importance in sliding contacts has been primarily attributed to two physical properties: its low melting point and the softness of its oxide. Because of the low melting point, the lead inside and around the contact region might go through a heat dissipating phase change.
This, in turn, keeps the contact region colder and more stable than it would be without the lead, allowing for larger current densities. The molten lead also inhibits copper welding [6]; without the lead, copper particles from the brush weld are drawn out of the brush by the sliding movement, producing greater wear. The soft lead oxide, on the other hand, works as a mild abrasive, assisting in the formation and maintenance of a stable, thin coating.
Materials that might potentially replace lead would need to be inexpensive, conductive, have a low melting temperature, a soft oxide, and have a low hazardous potential. Aluminium has a low melting point but cannot be used due to an extremely hard oxide. Tin and zinc are the only viable choices.
Tin and zinc both diffuse rapidly in copper. Even at room temperature, the diffusion rate of tin is so high that it is difficult to bring tin and copper in mechanical contact without an alloy developing within a few days. Unfortunately, because of their high melting points, these alloys cannot serve as heat sinks. With zinc, the situation is less urgent; still, diffusion must be controlled during the heat treatment.
Sl no | Topic |
1 | Market Segmentation |
2 | Scope of the report |
3 | Abbreviations |
4 | Research Methodology |
5 | Executive Summary |
6 | Introduction |
7 | Insights from Industry stakeholders |
8 | Cost breakdown of Product by sub-components and average profit margin |
9 | Disruptive innovation in the Industry |
10 | Technology trends in the Industry |
11 | Consumer trends in the industry |
12 | Recent Production Milestones |
13 | Component Manufacturing in US, EU and China |
14 | COVID-19 impact on overall market |
15 | COVID-19 impact on Production of components |
16 | COVID-19 impact on Point of sale |
17 | Market Segmentation, Dynamics and Forecast by Geography, 2024-2030 |
18 | Market Segmentation, Dynamics and Forecast by Product Type, 2024-2030 |
19 | Market Segmentation, Dynamics and Forecast by Application, 2024-2030 |
20 | Market Segmentation, Dynamics and Forecast by End use, 2024-2030 |
21 | Product installation rate by OEM, 2023 |
22 | Incline/Decline in Average B-2-B selling price in past 5 years |
23 | Competition from substitute products |
24 | Gross margin and average profitability of suppliers |
25 | New product development in past 12 months |
26 | M&A in past 12 months |
27 | Growth strategy of leading players |
28 | Market share of vendors, 2023 |
29 | Company Profiles |
30 | Unmet needs and opportunity for new suppliers |
31 | Conclusion |
32 | Appendix |