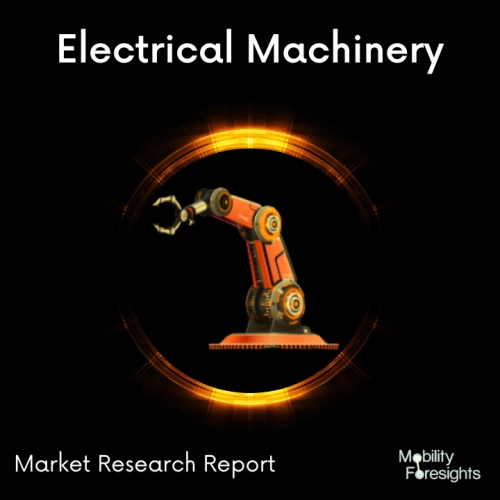
- Get in Touch with Us
Last Updated: Apr 25, 2025 | Study Period: 2024-2030
A surface grinder is a device used to shave or polish a metallic surface using a stationary, revolving abrasive wheel. Incorrect use of surface grinders can be harmful. Carefully read the owner's manual. Make sure that every component, switch, and plug is in good functioning order. Due to the extensive surface area of the grinding wheel in contact with the workpiece, rotary surface grinding is a very productive technique.
The whole surface to be ground makes touch with the grinding wheel surface during each rotation of the rotary table. Many applications could call for specialized alternatives or work-holding that is electromagnetic, mechanical, vacuum-sealed, pneumatic, or hydraulic.
In order to create work-holding devices that match your process' requirements for repeatable quality, precision, and productivity, our design team excels at working in tandem with your manufacturing or engineering organization. Rotary tables with variable speed, an electronic sensing Demag, and an electromagnetic chuck with variable force are typical.
On the majority of rotary surface grinders, configuration elements include through spindle vacuum, pneumatic, or hydraulic. The finishing step is when the Surface Grinder is primarily used. It is an extremely accurate instrument that is used to shave or finish a metallic surface that is fixed in place by a vice using a stationary, rotating abrasive wheel. Under the abrasive wheel, this vice, which is a component of a table or carriage, is moved back and forth.
The Global Rotary Surface Grinding Machine market accounted for $XX Billion in 2023 and is anticipated to reach $XX Billion by 2030, registering a CAGR of XX% from 2024 to 2030.
Motets launched the Rotary Surface Grinding Machine, the precise sensors and controls used in rotary surface grinders enable consistently tighter dimensional tolerances, flatness, parallelism, and surface polish.
Flat metals, alloys, and ceramics can be precisely ground before polishing using the equipment. With the new automated grinders, operator control over the process is unmatched. The user can specify the precise specifications, such as: a spindle speed of 712 RPMs, a table speed of 22 RPMs, a down-feed rate of.003 inches per minute, and a specified dwell cycle. In essence, the machine may be programmed to satisfy almost any need.
Sl no | Topic |
1 | Market Segmentation |
2 | Scope of the report |
3 | Abbreviations |
4 | Research Methodology |
5 | Executive Summary |
6 | Introduction |
7 | Insights from Industry stakeholders |
8 | Cost breakdown of Product by sub-components and average profit margin |
9 | Disruptive innovation in the Industry |
10 | Technology trends in the Industry |
11 | Consumer trends in the industry |
12 | Recent Production Milestones |
13 | Component Manufacturing in US, EU and China |
14 | COVID-19 impact on overall market |
15 | COVID-19 impact on Production of components |
16 | COVID-19 impact on Point of sale |
17 | Market Segmentation, Dynamics and Forecast by Geography, 2024-2030 |
18 | Market Segmentation, Dynamics and Forecast by Product Type, 2024-2030 |
19 | Market Segmentation, Dynamics and Forecast by Application, 2024-2030 |
20 | Market Segmentation, Dynamics and Forecast by End use, 2024-2030 |
21 | Product installation rate by OEM, 2023 |
22 | Incline/Decline in Average B-2-B selling price in past 5 years |
23 | Competition from substitute products |
24 | Gross margin and average profitability of suppliers |
25 | New product development in past 12 months |
26 | M&A in past 12 months |
27 | Growth strategy of leading players |
28 | Market share of vendors, 2023 |
29 | Company Profiles |
30 | Unmet needs and opportunity for new suppliers |
31 | Conclusion |
32 | Appendix |