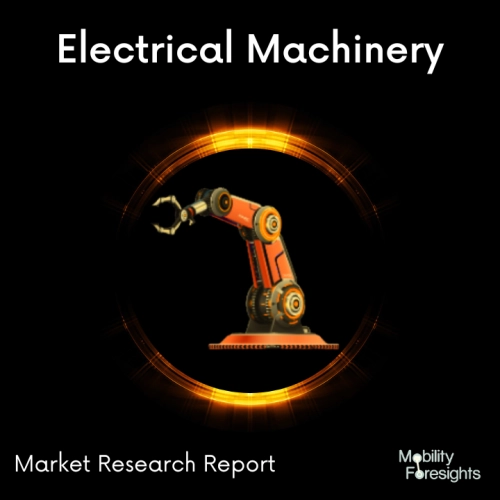
- Get in Touch with Us
Last Updated: Apr 25, 2025 | Study Period: 2024-2030
Rubber Crusher Machine Can crush rubber down to a minimum size by first cutting rubber into little pieces. During the crushing process, the rubber won't attach to the knife, allowing the machinery to run continuously for a considerable amount of time. Natural rubber NR, nitrile rubber NBR, styrene-butadiene rubber SBR, polybutadiene rubber BR, ethylene propylene rubber(EPDM), fluorine carbon rubber(FPM), silicone rubber(SI), urethane rubber(PU), and other raw materials are acceptable for this machine.
.
The Global Rubber Crusher Machine market accounted for $XX Billion in 2023 and is anticipated to reach $XX Billion by 2030, registering a CAGR of XX% from 2024 to 2030.
The Boston pyrolysis planâs Rubber Crusher Machine uses a stand-alone bearing, an overall foundation, and a horizontal structure, which makes installation, commissioning, and maintenance easy.
In the crushing chamber of the rough crusher, huge scrap rubber particles are crushed. The cutter positioned in two parallel shafts completes the crushing. The waste rubber is crushed by the relative movement of the jaws as the two axes rotate relative to one another in a specific ratio.
The rotating screen receives the pieces of crushed rubber. The pieces that meet the size criteria fall through the screen holes onto the conveyor belt and are then sent out, while the other non-standard pieces return with the screen to the crushing chamber to be crushed once more.
Special processing gives the cutter surface great hardness, stiffness, and wear resistance. When using a crusher, the motor is slowed down by the pulleys, followed by a deceleration of the transmission and reducer and rotation of the two spindles.
Compact design, sensible organization, efficient use of energy, quick and easy installation, and maintenance-free operation. The Rubber Crusher Machine has two different types of feeding devicesâa large conveyor belt and a tiny hoistâfrom which clients can select.
Customers have a choice based on the plant's location. The cutting edge is made of a unique hard alloy material and manufactured using a unique technique, giving it the benefits of a long service life, high efficiency, cutting-edge technology, and ease of replacement. The discharge screen has two options: a conventional round screen and a high-efficiency shaft linkage star screen mesh. It is set up to meet the needs of the customers.