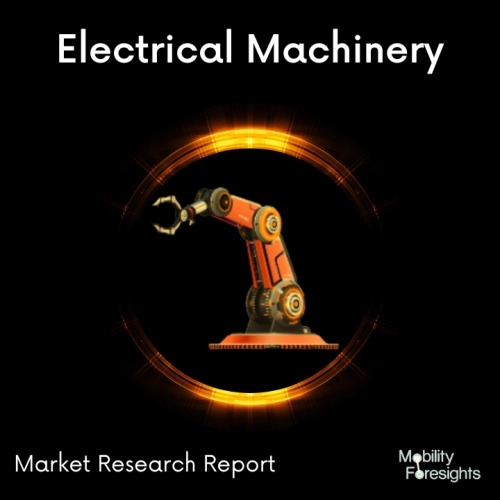
- Get in Touch with Us
Last Updated: Apr 25, 2025 | Study Period: 2024-2030
In the Rubber Extrusion Machine a rubber compound is put into the extruder to begin the rubber extrusion process. The rubber substance of choice is then placed into a feed hopper, which in essence feeds the substance into a rotating screw.
The rubber is fed into the die by the shearing screw, and as it approaches the die, pressure and temperature rise. The building pressure pushes the material through the openings as it approaches the die.
Depending on the hardness and compounds, the material will swell to varying degrees; as a result, some extruded pieces require plus or minus tolerances on their cross-sections.The extruded rubber will either expand or shrink in length or cross section during vulcanization (hardening rubber from heat and sulfur).
Using the rubber extrusion machine to make rubber has a number of advantages. The process is more effective in terms of decreased waste volumes, but it is also more cost-effective because production costs are typically lower than those of other manufacturing techniques.
The extruded rubber goods themselves also offer advantageous qualities. These items are perfect for usage in tough or extreme environments since they are incredibly long-lasting, sturdy, and highly resistant to chemicals, heat, cold, and abrasion.
The Global Rubber Extrusion Machine market accounted for $XX Billion in 2022 and is anticipated to reach $XX Billion by 2030, registering a CAGR of XX% from 2024 to 2030.
Conventional extrusion methods lose efficiency and dependability as dimensional tolerances become more stringent. The RMS Rubber Extrusion Machine, which combines the accuracy and dimensional control of a calendar with the flexibility and affordability of a basic extrusion head, is the answer to this issue.
The end result is a stable, high-quality product that consistently maintains exceptional dimensional features.Flexibility of a pressure head combined with calendar accuracy.
High degree of adaptability through simple, affordable, and flexible tooling.Reduced compound temperature and increased line speed are the effects of low pressure processes.Trimless die designs reduce waste and rework.
The Rubber Extrusion Machine , which RMS invented, employs the "pull" idea. The high pressure of the "push" mechanism is eliminated by moving the compound to the roll face where it is exposed to the environment.
On molecules that are sensitive to temperature, this enables increased productivity. With no die swell, the "pull" principle pulls the compound through the shaping die using the roll surface. The end result is a more affordable, stable, and accurate product in terms of dimensions.
Sustainable Intelligent Manufacturing of Plastic and Rubber Machines.With the rise of global environmental protection awareness, the improvement of process efficiency and pollution reduction of plastic products have become important issues for the rubber and plastic industry.
In response to the shortage of workers and the reduction of personnel contact, mechanical automation and cloud services have become the new normal in the industry.
Taiwan ranks sixth in the world for exports and has a full supply chain for plastic and rubber. The export value will surpass 30 billion Taiwan dollars in 2021.
The plastics and rubber industries in Taiwan have stayed steady despite a number of unfavourable circumstances, including the current pandemic crisis, changes in China's political climate, the war between Russia and Ukraine, and inflation. The globe has taken notice of the impressive performance.
The most significant trend in global smart manufacturing is net-zero carbon emissions.The objective of sustainable development is achieved by energy-efficient design, recycling, and smart manufacturing.
Understanding the technical development trend and commercial prospects in the plastic and rubber machinery sector, as well as implementing digital marketing to attack the global market, will be the focus of future market growth.
Manufacturers of machinery and equipment play an important role in assisting firms in increasing profits and lowering manufacturing costs while improving product quality and standards. The early adoption of the Industrial Internet of Things and environmentally friendly production techniques represents a new potential for the world's plastic equipment business.
The demand for net zero carbon emissions will spur a new wave of global investment, and it will be eliminated if it does not catch up, according to an analysis of the development trend of the global manufacturing industry based on the application trend and business opportunities of plastic and rubber machinery and equipment.
Additionally, research and development of various new materials to replace conventional rubber and plastic materials have turned into a required trend in the development of rubber and plastic goods in order to accomplish waste reduction, a circular economy, and accelerate net zero carbon emissions.
Future industrial upgrading will be aided by the development focus on the circular economy, quality enhancement, industry 4.0+ intelligence, and quick, ruthless, accurate + aesthetically pleasing designs.Smart Manufacturing in the Rubber and Plastic Industry evolution: The international trend of Industry 4.0 has changed the evolution of the Plastic Industry.
The primary objective of Industry 4.0 is to combine existing industrial technology, sales, and product experience in order to create a smart industrial world with product customisation and service-oriented supply capabilities.
One of the pillars of Industry 4.0 is smart manufacturing, which combines information technologies such as advanced manufacturing technology, the Internet of Things (IoT), cloud computing, and artificial intelligence (AI).
The intelligent manufacturing line provides several advantages to rubber and plastic industries. Consider rubber and plastic injection moulding techniques.
When the completed product to be injected is a complicated component, it is often required to rely on expert processors to provide high-quality and high-efficiency output in the conventional manufacturing and processing business.
Smart manufacturing, on the other hand, is to create and manufacture by gathering large data from various sensing devices and batches of output and performing real-time analysis and feedback, which is known as know-how digitization.
This may provide product quality stability and uniformity, which will not be affected by processor changes or flow. Factory managers may more precisely plan maintenance and repair plans to raise and maintain the maximum output capacity of the production line thanks to the real-time monitoring data of the whole manufacturing system.
Additionally, the production process used in smart manufacturing raises consumer satisfaction. After the customer and the manufacturer sign a formal production agreement, the client factory may, at any time, use the real-time monitoring system of the smart manufacturing system to keep track of the schedule of ordered items and the most recent information regarding the status of production.
The Transformation of the Plastic and Rubber Industry is Facilitated by Smart Machinery Cloud Platform:The multiple intelligent functions of the cloud platform can be used by the rubber and plastics sector to solve the back-end integration and communication delays that plague industrial equipment, hasten the transition to smart manufacturing, and help plastic machinery become more globally competitive.
To get international orders, cut the time it takes to integrate information by 50% using a cloud platform. Additionally, create intelligent manufacturing production lines, implement online quality monitoring, reduce the complete inspection cycle, and effectively land orders for lightweight components from abroad.
The rising worldwide epidemic has altered the industrial supply networks of many different nations. Smart manufacturing and supply chain resilience are problems that all sectors deal with on a regular basis. Value-added software services, software and hardware integration services, and system solutions are employed through cloud-based APPs to support equipment companies in upgrading their facilities intelligently and resolving numerous challenges.
Develop a smart cloud service settlement, expand the smart machine cloud platform, and aid business in creating smart manufacturing and boosting digital competitiveness.
The production of plastics and rubber throughout the world is now hampered by a severe labour shortage as well as the problem of international carbon levies.
Unavoidably, the plastics and rubber sector will need to improve its understanding of machine energy usage. The machines were previously adjusted by seasoned masters, and manual testing was used to determine the quality of the final result.
The establishment of a compliant information and communication interface on existing equipment by the smart machinery cloud offers a comprehensive solution. and utilising standardised communication protocols to resolve equipment connection communication issues.
Additionally, it may speed up the process of integrating with the back-end management system, provide a real-time detection mechanism, and enable online comprehension of the important quality.
Create a machine network to track and manage completed product quality in real-time, improving equipment value and boosting global competitiveness. Additionally, establishing a smart manufacturing production line and switching to online quality inspection would minimise waste production by 20% and shorten the complete inspection cycle time.
in response to current industry and forthcoming market developments in the area of applications for a sustainable environment. Together with advantages from cross-disciplinary research and development in electronics, information communication, and AI, a smart machine cloud platform is developed, allowing for a swift transition to smart manufacturing.
Sl no | Topic |
1 | Market Segmentation |
2 | Scope of the report |
3 | Abbreviations |
4 | Research Methodology |
5 | Executive Summary |
6 | Introduction |
7 | Insights from Industry stakeholders |
8 | Cost breakdown of Product by sub-components and average profit margin |
9 | Disruptive innovation in the Industry |
10 | Technology trends in the Industry |
11 | Consumer trends in the industry |
12 | Recent Production Milestones |
13 | Component Manufacturing in US, EU and China |
14 | COVID-19 impact on overall market |
15 | COVID-19 impact on Production of components |
16 | COVID-19 impact on Point of sale |
17 | Market Segmentation, Dynamics and Forecast by Geography, 2024-2030 |
18 | Market Segmentation, Dynamics and Forecast by Product Type, 2024-2030 |
19 | Market Segmentation, Dynamics and Forecast by Application, 2024-2030 |
20 | Market Segmentation, Dynamics and Forecast by End use, 2024-2030 |
21 | Product installation rate by OEM, 2022 |
22 | Incline/Decline in Average B-2-B selling price in past 5 years |
23 | Competition from substitute products |
24 | Gross margin and average profitability of suppliers |
25 | New product development in past 12 months |
26 | M&A in past 12 months |
27 | Growth strategy of leading players |
28 | Market share of vendors, 2022 |
29 | Company Profiles |
30 | Unmet needs and opportunity for new suppliers |
31 | Conclusion |
32 | Appendix |