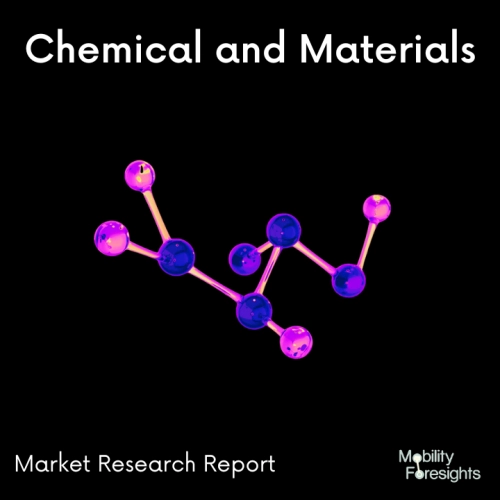
- Get in Touch with Us
Last Updated: Apr 25, 2025 | Study Period: 2024-2030
Molding is the technique of molding liquid or malleable raw material using a rigid frame known as a mold or matrix. This might have been created using a pattern or model of the finished thing.
Rubber molding is the process of converting uncured rubber or an elastomer into a useful product by the transfer, compression, or injection of raw rubber material into a metal mold cavity. Injection, compression, and transfer are the three most popular procedures for rubber molding.
Rubber molding is the act of moving, compressing, or injecting raw rubber material into a metal mold cavity in order to turn uncured rubber or an elastomer into a useful product. When pressure is applied when heat is present, a chemical process, such as curing or vulcanization, occurs that causes the material's polymer chains to cross-link.
Rubber injection molding may be done using a number of rubber compounds, such as silicone, neoprene, nitrile, and EPDM, and has allowed producers to make a wide range of molded rubber items. Rubber injection molding is a technique that involves injecting uncured rubber into a mold.
The rubber remains in the mold for a certain period of time before vulcanizing into its final shape. While injection molding is a sort of rubber molding, it may also be used with a variety of other materials, including metals and glass. Uncured rubber is turned into a usable product through the manufacturing process known as rubber molding.
Different procedures that include heating and molding rubber in a metal cavity are used to accomplish this. Injection molding, compression molding, and transfer molding are the three primary forms of molding.
Rubber compression molding is accomplished by inserting prepared forms of uncured rubber into the cavities of a heated mold, which is then sealed shut with hydraulic pressure. The heated cavity holds the rubber until it is molded to its final shape.
In order to do rubber transfer molding, a transfer pot is filled with a certain volume of uncured rubber. The preform is then pushed through the runner and gate system and into the part cavity as the ram is then closed. To cure the rubber into its final shape, it must remain in the heated cavity for a predetermined period of time.
Rubber is a special kind of material that enables it to be strong, long-lasting, flexible, abrasion-resistant, and very waterproof. The latex of rubber trees is used to make natural rubber. Making incisions in the bark of these trees enables the latex (sticky, milky colloid) to be pulled out while collecting the liquid in containers.
The rubber created from the purified latex is then suitable for industrial processing. There are many different rubber kinds to choose from, and each of these rubber types has unique features that vary from electrical insulation to vibration reduction.
Heat and pressure are used by all rubber producers to create their goods. Injection, compression, and transfer are the three most often used techniques for rubber molding. Rubber mold manufacturers are constantly changing their goods to fulfill the rising need for grommets, gaskets, o-rings, and seals.
The Global rubber molding market accounted for $XX Billion in 2023 and is anticipated to reach $XX Billion by 2030, registering a CAGR of XX% from 2024 to 2030.
Structur3D Launches Inj3ctor Platform, a New Solution for Desktop Injection Moulding of Rubber Parts.A new option for desktop injection molding rubber parts, the Inj3ctor Platform, was made available by Structur3D, a global leader in sophisticated additive manufacturing for soft materials.
By enhancing its material capabilities to produce new goods using factory-grade rubber materials, such silicones and polyurethanes, the firm is improving and securing the position of 3D printing inside industrial production.
The Inj3ctor is the first product on the market to integrate 3D printing technology with injection molding principles. The Inj3ctor is a turnkey, small-batch rubber material manufacturer that uses 3D-printed molds to mix and inject 2-component (2K) flexible polymers into any customisable form.
With this, manufacturers may accept 3D printing more easily than before. Because rubber 3D printing currently falls short of required production requirements, the rubbers sector has struggled to gain a genuine place at the table in advanced manufacturing.
The Inj3ctor platform combines desktop injection with 3D printing to provide an effective method for producing useful parts. These methods, along with the materials of professional quality, make the models suitable for all stages of manufacturing, from prototype to production.
Since it also lowers the cost and procurement risks associated with the production of rubber parts, the solution is a pioneer in small-batch manufacturing. If manufacturers didn't opt to omit the element entirely from the design, they would have either hand-cast the parts or purchased expensive mass production methods to accomplish this.
This is crucial as bigger manufacturers start looking at the possibility of producing consumer goods on-demand and in bespoke forms in the future.
This has the potential to have an influence on a wide range of businesses, including those in the automotive, industrial goods, aerospace, academic, energy, and medical fields, as well as diverse consumer items where the customer can customize certain aspects of the design, as is common with footwear.
Sl no | Topic |
1 | Market Segmentation |
2 | Scope of the report |
3 | Abbreviations |
4 | Research Methodology |
5 | Executive Summary |
6 | Introduction |
7 | Insights from Industry stakeholders |
8 | Cost breakdown of Product by sub-components and average profit margin |
9 | Disruptive innovation in the Industry |
10 | Technology trends in the Industry |
11 | Consumer trends in the industry |
12 | Recent Production Milestones |
13 | Component Manufacturing in US, EU and China |
14 | COVID-19 impact on overall market |
15 | COVID-19 impact on Production of components |
16 | COVID-19 impact on Point of sale |
17 | Market Segmentation, Dynamics and Forecast by Geography, 2024-2030 |
18 | Market Segmentation, Dynamics and Forecast by Product Type, 2024-2030 |
19 | Market Segmentation, Dynamics and Forecast by Application, 2024-2030 |
20 | Market Segmentation, Dynamics and Forecast by End use, 2024-2030 |
21 | Product installation rate by OEM, 2023 |
22 | Incline/Decline in Average B-2-B selling price in past 5 years |
23 | Competition from substitute products |
24 | Gross margin and average profitability of suppliers |
25 | New product development in past 12 months |
26 | M&A in past 12 months |
27 | Growth strategy of leading players |
28 | Market share of vendors, 2023 |
29 | Company Profiles |
30 | Unmet needs and opportunity for new suppliers |
31 | Conclusion |
32 | Appendix |