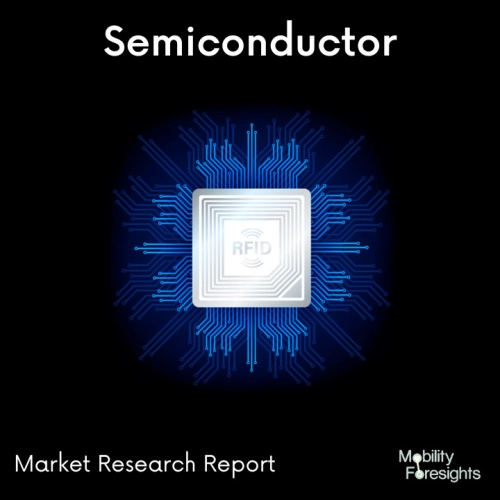
- Get in Touch with Us
Last Updated: Apr 25, 2025 | Study Period: 2024-2030
A Semiconductor Chemical Delivery System (CDS) is a specialized apparatus used in semiconductor manufacturing processes to transport and manage the numerous chemicals necessary for the production of integrated circuits and other semiconductor devices. These substances are necessary for the cleaning, etching, deposition, and other steps in the production of semiconductors.
The CDS is in charge of precisely and safely delivering the necessary chemicals to the semiconductor production equipment, as well as preserving the purity of the chemicals and guaranteeing accurate process control. Storage tanks, chemical filters, valves, flow meters, pressure regulators, and control systems are some of the common components found in it.
Here are some of a semiconductor chemical delivery system's essential characteristics and features:Chemical Storage: The system has tanks or other storage units for the various chemicals used in the production of semiconductors. These tanks are made to hold chemicals and keep them at the desired purity levels.
Before the chemicals are transported to the process equipment, contaminants and particles are removed from them using chemical filters. This helps prevent contamination throughout the fabrication process and preserves the cleanliness and integrity of the chemicals.
Chemical Delivery: To regulate the flow rate and pressure of the chemicals being given to the process equipment, the CDS uses a variety of delivery techniques, including pumps, pressure regulators, and flow meters. For accurate and reliable chemical delivery, precise control is required.
Safety and monitoring: To avoid any dangerous conditions and guarantee operator safety, semiconductor CDSs integrate safety measures such as leak detection systems, pressure and temperature sensors, and alarms. Systems for monitoring keep track of the use, concentrations, and conditions of the chemicals, enabling effective upkeep and restocking.
System Control: A control system that oversees the automation, operation, and monitoring of the chemical delivery process is often installed in the CDS. It makes it possible to precisely manage chemical flow rates, pressure, and other variables to produce results that are dependable and repeatable.
By providing precise and controlled distribution of the chemicals required for various fabrication steps, semiconductor chemical delivery systems, in general, play a crucial role in the semiconductor manufacturing process. While ensuring the safety of people, property, and equipment in this semiconductor manufacturing environment, they assist in maintaining process integrity, yield, and product quality.
The Global Semiconductor Chemical Delivery System Market accounted for $XX Billion in 2023 and is anticipated to reach $XX Billion by 2030, registering a CAGR of XX% from 2024 to 2030.
Tempe (Ariz.) For high-volume semiconductor production, Ver sum Materials recently unveiled their CHEMGUARD Gen III high-purity liquid delivery system. The systems, which have been created to guarantee 100 percent tool uptime, are single-reservoir bulk chemical delivery cabinets for fab-wide chemical distribution. The liquid delivery systems handle aggressive chemistries in challenging conditions and are in compliance with Division II.
Since the technology was introduced, the company has installed 200 units. The Schumacher brand served as the launchpad for the CHEMGUARD product line. The company has established a multi-disciplinary team that evaluates new compounds as they ramp and achieves market acceptability, capitalizing on its knowledge of materials and delivery systems.
By striving to develop delivery systems that are prepared for technological ramps, the team examines chemical safety and process needs, assisting in shortening the time it takes to market new compounds and processes.
1 | Market Segmentation |
2 | Scope of the report |
3 | Abbreviations |
4 | Research Methodology |
5 | Executive Summary |
6 | Introduction |
7 | Insights from Industry stakeholders |
8 | Cost breakdown of Product by sub-components and average profit margin |
9 | Disruptive innovation in the Industry |
10 | Technology trends in the Industry |
11 | Consumer trends in the industry |
12 | Recent Production Milestones |
13 | Component Manufacturing in US, EU and China |
14 | COVID-19 impact on overall market |
15 | COVID-19 impact on Production of components |
16 | COVID-19 impact on Point of sale |
17 | Market Segmentation, Dynamics and Forecast by Geography, 2024-2030 |
18 | Market Segmentation, Dynamics and Forecast by Product Type, 2024-2030 |
19 | Market Segmentation, Dynamics and Forecast by Application, 2024-2030 |
20 | Market Segmentation, Dynamics and Forecast by End use, 2024-2030 |
21 | Product installation rate by OEM, 2023 |
22 | Incline/Decline in Average B-2-B selling price in past 5 years |
23 | Competition from substitute products |
24 | Gross margin and average profitability of suppliers |
25 | New product development in past 12 months |
26 | M&A in past 12 months |
27 | Growth strategy of leading players |
28 | Market share of vendors, 2023 |
29 | Company Profiles |
30 | Unmet needs and opportunity for new suppliers |
31 | Conclusion |
32 | Appendix |