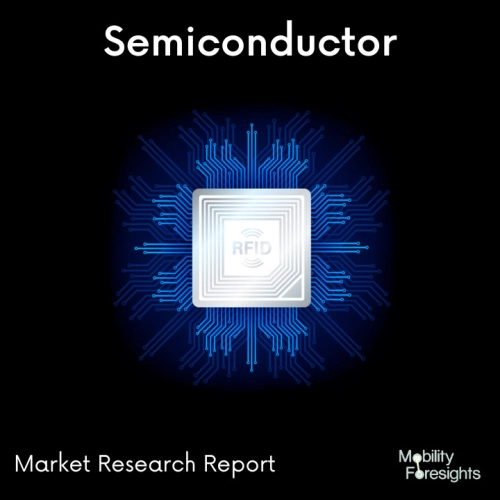
- Get in Touch with Us
Last Updated: Apr 26, 2025 | Study Period:
An epitaxial wafer is a semiconducting wafer grown epitaxially for application in photonics, microelectronics, spintronics, or photovoltaics. The epi layer can be made of the same material as the substrate, which is commonly monocrystalline silicon, or it can be made of silicon dioxide (Soi) or a more exotic material with certain desired properties.
The goal of epitaxy is to perfect the crystal structure over the bare substrate beneath and enhance the electrical properties of the wafer surface, making it suitable for extremely complicated microprocessors and memory devices.
When the epi-layer and substrate are made of the same material, ion implantation is used to deposit a thin layer of crystal impurity atoms and the associated mechanical stress at the precise depth of the desired epi layer thickness.
In the ensuing cleavage stage, the resultant localized stress offers a controlled channel for fracture growth. A controlled crack is driven by a temperature change at the epi/wafer interface purely by thermal stresses due to the mismatch in thermal expansion between the epi layer and substrate in the dry stress lift-off process.
This is applicable when the epi-layer and substrate are suitably different materials, without the need for any external mechanical force or tool to aid crack propagation. This technique was reported to produce single atomic plane cleavage, minimizing the requirement for post-lift-off polishing and allowing up to ten substrate reuses.
Silicon epitaxy is the technique of depositing an extra monocrystalline silicon layer on the polished crystal surface of a silicon wafer. This procedure allows for the selection of material qualities independent of the polished substrate, resulting in wafers with varied properties in the substrate and the epitaxial layer.
In many circumstances, this is required for the semiconductor component to perform properly.The epitaxial layers may be composed of compounds with favorable properties such as gallium nitride (Gan), gallium arsenide (GaAs), or a mixture of gallium, indium, aluminum, nitrogen, phosphorus, or arsenic.
Because the thermal expansion coefficients of silicon and Gan are so dissimilar, Gan epitaxy necessitates the formation of a buffer layer on the polished silicon wafer first. Mechanical tension between the two materials can therefore be reduced.
Furthermore, an Alga layer is formed on top of the Gan layer to generate a two-dimensional electron plasma at the interface of these two layers. Electrons may travel at very high speeds at the device level, making Gan superior to traditional silicon technology.
EPI stands for Epitaxial Growth. It is a process of growing a thin layer of semiconductor material on top of a substrate. The substrate is typically a silicon wafer, but other materials can also be used. The epitaxial layer can be of a different material than the substrate, or it can be the same material with different doping levels.
EPI wafer manufacturing is a complex process that involves several steps. The first step is to clean the substrate. This is done to remove any contaminants that could interfere with the growth of the epitaxial layer. The substrate is then heated to a high temperature and a gas containing the desired semiconductor material is introduced.
The gas reacts with the substrate and forms a thin layer of semiconductor material. The thickness of the layer can be controlled by the amount of time that the gas is exposed to the substrate.
Once the epitaxial layer has been grown, it is cooled and then processed further. This may include ion implantation, doping, and annealing. The final step is to test the wafer to make sure that it meets the desired specifications.
EPI wafer manufacturing is a critical process in the production of semiconductors. It is used to create a variety of semiconductor devices, including integrated circuits, transistors, and diodes.
The Global Semiconductor Epi Wafer Manufacturing Market accounted for $XX Billion in 2023 and is anticipated to reach $XX Billion by 2030, registering a CAGR of XX% from 2024 to 2030.
Resonate Corporation has begun mass production of a third generation of high-grade silicon carbide (Sic) epitaxial wafer (HGE-3G) for power semiconductors. HGE-3G has a higher quality than second-generation high-grade Sic epi-wafer (HGE-2G), which has been mass-produced up to now.
Sic power semiconductor lowers power loss during electricity conversion and emits less heat than conventional silicon-wafer-based power semiconductor, saving energy. As a result, demand for Sic power semiconductors is fast expanding, particularly in industrial applications such as electric vehicles (EVs) and renewable-energy-based power production.
Sic epi-wafers are created by depositing and growing an epitaxial Sic layer on the surface of a single crystal Sic substrate, and they are utilized as the primary material for Sic power. As the world's biggest independent provider of world-class Sic epi-wafers, Resonance is well-regarded by numerous device makers.
High-end versions of power semiconductors for use in high-priced EVs and railcars must transmit higher-density electric current to achieve high output while preserving space. To achieve high-density electric current conduction, Sic-epi-wafer producers must develop technology to avoid the growth of dislocation faults in the Sic substrate into the epitaxial Sic layer.
This time, Resonance created cutting-edge technology to generate epitaxial Sic layers, effectively resolving the aforementioned issue, and began mass-producing third-generation high-grade Sic epi-wafers. This HGE-3G offers outstanding reliability under high electric current density and will help Sic-based high-end power modules expand.
Showa Denko K.K. (SDK) will introduce the biggest size silicon carbide (Sic) epitaxial wafers currently available on the global market for usage in power devices. Next month, the business will also begin offering Sic epitaxial wafers with fewer flaws and more uniformity. SDK has previously produced and sold Sic epitaxial wafers.
Furthermore, SDK has worked to build next-generation Sic epitaxial wafers, which will lead to greater productivity, and has provided samples. The firm has planned to commence commercial shipments as soon as the volume manufacturing technology has been established and the product requirements have been finalized.
SDK will continue its efforts to improve product quality and boost manufacturing capacity following the development of product lines.
Sl no | Topic |
1 | Market Segmentation |
2 | Scope of the report |
3 | Abbreviations |
4 | Research Methodology |
5 | Executive Summary |
6 | Introduction |
7 | Insights from Industry stakeholders |
8 | Cost breakdown of Product by sub-components and average profit margin |
9 | Disruptive innovation in the Industry |
10 | Technology trends in the Industry |
11 | Consumer trends in the industry |
12 | Recent Production Milestones |
13 | Component Manufacturing in US, EU and China |
14 | COVID-19 impact on overall market |
15 | COVID-19 impact on Production of components |
16 | COVID-19 impact on Point of sale |
17 | Market Segmentation, Dynamics and Forecast by Geography, 2024-2030 |
18 | Market Segmentation, Dynamics and Forecast by Product Type, 2024-2030 |
19 | Market Segmentation, Dynamics and Forecast by Application, 2024-2030 |
20 | Market Segmentation, Dynamics and Forecast by End use, 2024-2030 |
21 | Product installation rate by OEM, 2023 |
22 | Incline/Decline in Average B-2-B selling price in past 5 years |
23 | Competition from substitute products |
24 | Gross margin and average profitability of suppliers |
25 | New product development in past 12 months |
26 | M&A in past 12 months |
27 | Growth strategy of leading players |
28 | Market share of vendors, 2023 |
29 | Company Profiles |
30 | Unmet needs and opportunity for new suppliers |
31 | Conclusion |
32 | Appendix |