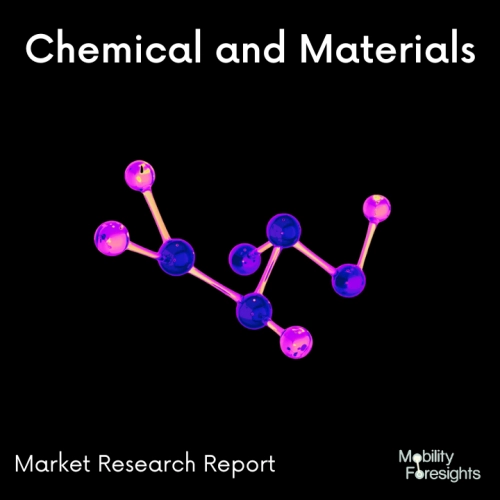
- Get in Touch with Us
Last Updated: Apr 25, 2025 | Study Period: 2023-2030
Plastics can trap teeny-tiny pockets of gas during the extrusion or injection moulding processes. These trapped gas bubbles can develop and blow tiny holes in the surface of the plastic with the help of heat, sunlight, and time, releasing the gas and outgassing.
In regions with delicate electronics, lenses (optics), mirrors, and windows, the outgassing performance of a material is crucial for preventing damage to those components. In regions with delicate electronics, lenses (optics), mirrors, and windows, the outgassing performance of a material is crucial for preventing damage to those components.
Outgassing in the clean room for semiconductors. The process of outgassing involves the discharge of trapped or stored gas from a solid material. It's a regular worry with high-frequency circuit boards and electronic equipment, the very goods that semiconductors are used to make work.
The global semiconductor Low outgassing plastics market accounted for $XX Billion in 2022 and is anticipated to reach $XX Billion by 2030, registering a CAGR of XX% from 2023 to 2030.
A standard test for detecting outgassing in adhesives and other materials, known as ASTM E595, created by NASA, is one of the stringent methods for testing products prior to their usage in space.
The phrase "A Standard Test Method for Total Mass Loss and Collected Volatile Condensable Materials from Outgassing in a Vacuum Environment" is what it is called in its entirety. According to ASTM International, a reputable organisation that develops materials standards, ASTM E595 measures important material characteristics like total mass loss (TML) and collected volatile condensable materials (CVCM) to assess how the mass of various materials would change in a vacuum environment as a result of semiconductor low outgassing.
In a heated vacuum chamber, material samples are deposited, and the test determines the volatile content of those samples. Prior to being weighed, samples are preconditioned at 50% relative humidity for 24 hours.
They then spend a further 24 hours in the test chamber with the temperature set to 125° C and the vacuum set to at least 5 x 10-5 torr (by way of comparison, so-called deep space is 10-14 torr). Volatiles from the sample that outgas while it is in the test chamber escape through a port and condense on a cooled (25° C) collector plate.
The TML by the sample and the amount of CVCM on the collecting plate are then calculated by weighing the sample and condensate on the plate. These TML and CVCM measures determine whether a material passes or fails the test.
Sl no | Topic |
1 | Market Segmentation |
2 | Scope of the report |
3 | Abbreviations |
4 | Research Methodology |
5 | Executive Summary |
6 | Introduction |
7 | Insights from Industry stakeholders |
8 | Cost breakdown of Product by sub-components and average profit margin |
9 | Disruptive innovation in the Industry |
10 | Technology trends in the Industry |
11 | Consumer trends in the industry |
12 | Recent Production Milestones |
13 | Component Manufacturing in US, EU and China |
14 | COVID-19 impact on overall market |
15 | COVID-19 impact on Production of components |
16 | COVID-19 impact on Point of sale |
17 | Market Segmentation, Dynamics and Forecast by Geography, 2023-2030 |
18 | Market Segmentation, Dynamics and Forecast by Product Type, 2023-2030 |
19 | Market Segmentation, Dynamics and Forecast by Application, 2023-2030 |
20 | Market Segmentation, Dynamics and Forecast by End use, 2023-2030 |
21 | Product installation rate by OEM, 2023 |
22 | Incline/Decline in Average B-2-B selling price in past 5 years |
23 | Competition from substitute products |
24 | Gross margin and average profitability of suppliers |
25 | New product development in past 12 months |
26 | M&A in past 12 months |
27 | Growth strategy of leading players |
28 | Market share of vendors, 2023 |
29 | Company Profiles |
30 | Unmet needs and opportunity for new suppliers |
31 | Conclusion |
32 | Appendix |