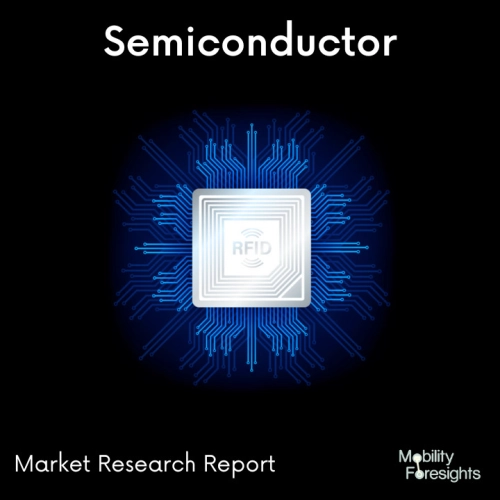
- Get in Touch with Us
Last Updated: Apr 25, 2025 | Study Period:
Due to its strength and resistance to acids and impurities like mould and mildew, high-density polyethylene sheet is frequently used as a semiconductor material.
Due to its adaptability and malleability, it can be utilised to produce plastic components and accessories that adhere to the strict standards for quality and purity set by the sector.
Along with being easier to machine, HDPE is also a more affordable alternative to classic materials like ceramics or quartz. Semiconductors are made using abrasive chemicals, sometimes even acids.
Along with many other qualities that are similar to those of HDPE, polypropylene also exhibits outstanding chemical and acid resistance, but it is also a more affordable choice that is very advantageous to the industry.
Polypropylene can be used to make plastic semiconductors and components including electrical insulators and integrated circuit chips, in addition to wet benches and workstations.
The Global semiconductor plastics market accountedfor $XX Billion in 2021 and is anticipated to reach $XX Billion by 2030, registering a CAGR of XX% from 2022 to 2030.
For semiconductor products like wafers and microchips, the industry requires strict environmental and production criteria.
Given the quantity of extremely corrosive chemicals that machinery like wet benches and workstations must be exposed to during the manufacturing process, such regulations might be challenging to meet.
Plastic for semiconductors aids in maintaining high purity standards during semiconductor fabrication, resulting in less time and resource waste and guaranteeing that electronics work exactly as intended.
It's crucial to understand the sort of facility semiconductors are created in in order to comprehend why plastic is the best material for semiconductors and semiconductor production.
The greatest benefit of plastic over conventional materials for semiconductors is its ability to withstand chemicals.
For instance, during procedures like acid etching and chemical rinsing and drying, wet benches are frequently exposed to extremely corrosive chemicals including nitric acid, hydrochloric acid, hydrofluoric acid, and ozone.
If metals were subjected to these kinds of conditions, they would corrode and release particulates into the clean manufacturing zone, contaminating it and leading to semiconductor failure.
Certain semiconductor production processes require high heat levels that could ignite other materials. Because semiconductor plastic is nonflammable and performs well in these high temperatures, fire accidents in your facility's clean room are less likely to happen.
Sl no | Topic |
1 | Market Segmentation |
2 | Scope of the report |
3 | Abbreviations |
4 | Research Methodology |
5 | Executive Summary |
6 | Introduction |
7 | Insights from Industry stakeholders |
8 | Cost breakdown of Product by sub-components and average profit margin |
9 | Disruptive innovation in the Industry |
10 | Technology trends in the Industry |
11 | Consumer trends in the industry |
12 | Recent Production Milestones |
13 | Component Manufacturing in US, EU and China |
14 | COVID-19 impact on overall market |
15 | COVID-19 impact on Production of components |
16 | COVID-19 impact on Point of sale |
17 | Market Segmentation, Dynamics and Forecast by Geography, 2024-2030 |
18 | Market Segmentation, Dynamics and Forecast by Product Type, 2024-2030 |
19 | Market Segmentation, Dynamics and Forecast by Application, 2024-2030 |
20 | Market Segmentation, Dynamics and Forecast by End use, 2024-2030 |
21 | Product installation rate by OEM, 2023 |
22 | Incline/Decline in Average B-2-B selling price in past 5 years |
23 | Competition from substitute products |
24 | Gross margin and average profitability of suppliers |
25 | New product development in past 12 months |
26 | M&A in past 12 months |
27 | Growth strategy of leading players |
28 | Market share of vendors, 2023 |
29 | Company Profiles |
30 | Unmet needs and opportunity for new suppliers |
31 | Conclusion |
32 | Appendix |