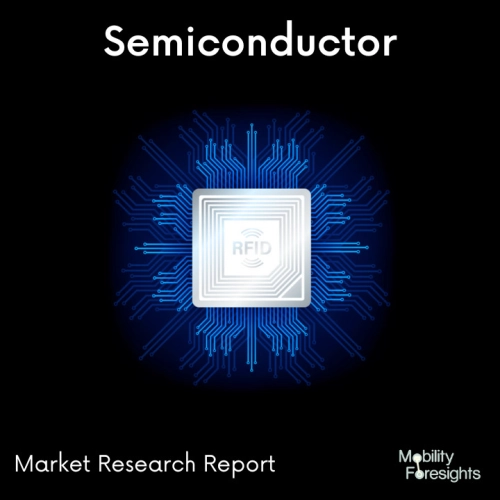
- Get in Touch with Us
Last Updated: Apr 25, 2025 | Study Period: 2024-2030
High-quality silicon carbide crystals are made using specialised machinery called a SiC (silicon carbide) Crystal Growth Furnace System. With its remarkable thermal, electrical, and mechanical qualities, silicon carbide is a compound semiconductor that may be used in a wide range of industries, including the power electronics, aerospace, and automotive sectors.
Physical vapour transport (PVT) is a technique used by the SiC Crystal Growth Furnace System to create massive silicon carbide single crystals. The procedure requires heating silicon carbide source material in a controlled setting (often referred to as a seed crystal).
Carbon and silicon atoms are moved to a colder area as the source material vaporises, where they condense and create a single crystal.
The growth furnace system is made up of a number of essential parts, including:
Reaction Chamber: This is the primary container in which crystal formation takes place. It is made to keep the precise temperature and gas composition needed for crystal formation.
Heating System: The source material is carefully heated by the heating system until the desired vaporisation temperature is reached.
Cooling system: To produce a heat gradient inside the growth chamber, a cooling system is used. It makes it possible for vaporised silicon and carbon to condense onto the seed crystal, which promotes crystal development.
Gas Control System: The gas control system manages the growth chamber's pressure and gas composition. It guarantees the ideal crystal growth conditions and may entail the addition of reactive gases that facilitate silicon carbide production.
A pedestal known as the "seed holder" keeps the seed crystal in place while it grows. It enables the crystal orientation to be positioned and controlled precisely.
Vacuum system: To create and maintain the desired pressure inside the growth chamber, a vacuum system is used. The physical vapour transport process requires a low-pressure environment, which is created via this technique.
The careful control of temperature, pressure, and gas composition is necessary for SiC Crystal Growth Furnace Systems to produce high-quality single crystals. These crystals can subsequently be refined and utilised in a variety of applications, including innovative materials, high-temperature sensors, and power electrical devices.
The Global SiC Crystal Growth Furnace System market accounted for $XX Billion in 2022 and is anticipated to reach $XX Billion by 2030, registering a CAGR of XX% from 2024 to 2030.
Introducing the SiCloneTM100 silicon carbide (SiC) manufacturing furnace is GT Advanced Technologies.
The SiClone100 employs sublimation growth technology that can produce bulk SiC crystals of excellent semiconducting quality that can be polished into wafers with a diameter of up to 100 millimetres.
The SiClone100's initial offering is geared at clients who have established their own hot zones, qualified a bulk crystal manufacturing recipe, and are prepared to start volume production.
The power electronics sector needs more high-quality SiC material for use in cutting-edge, high-power, high-frequency devices, and GT's new SiClone100 furnace fills that need.
The SiClone100 serves as the cornerstone for our SiC product roadmap, which will eventually give clients access to a full production environment with recipes, hot zones, and consumables that can produce SiC wafers up to eight inches in diameter.
GT has taken use of its in-depth domain experience in crystal growth technology to provide customers wishing to transition from "the lab to the fab" with a highly dependable and tested platform to start producing SiC bulk crystal in large quantities.
The SiClone100 furnace has a cutting-edge control system that, by incorporating the furnace electronics into the human-machine interface (HMI) control, aids in automating the growing process.
Sl no | Topic |
1 | Market Segmentation |
2 | Scope of the report |
3 | Abbreviations |
4 | Research Methodology |
5 | Executive Summary |
6 | Introduction |
7 | Insights from Industry stakeholders |
8 | Cost breakdown of Product by sub-components and average profit margin |
9 | Disruptive innovation in the Industry |
10 | Technology trends in the Industry |
11 | Consumer trends in the industry |
12 | Recent Production Milestones |
13 | Component Manufacturing in US, EU and China |
14 | COVID-19 impact on overall market |
15 | COVID-19 impact on Production of components |
16 | COVID-19 impact on Point of sale |
17 | Market Segmentation, Dynamics and Forecast by Geography, 2024-2030 |
18 | Market Segmentation, Dynamics and Forecast by Product Type, 2024-2030 |
19 | Market Segmentation, Dynamics and Forecast by Application, 2024-2030 |
20 | Market Segmentation, Dynamics and Forecast by End use, 2024-2030 |
21 | Product installation rate by OEM, 2023 |
22 | Incline/Decline in Average B-2-B selling price in past 5 years |
23 | Competition from substitute products |
24 | Gross margin and average profitability of suppliers |
25 | New product development in past 12 months |
26 | M&A in past 12 months |
27 | Growth strategy of leading players |
28 | Market share of vendors, 2023 |
29 | Company Profiles |
30 | Unmet needs and opportunity for new suppliers |
31 | Conclusion |
32 | Appendix |