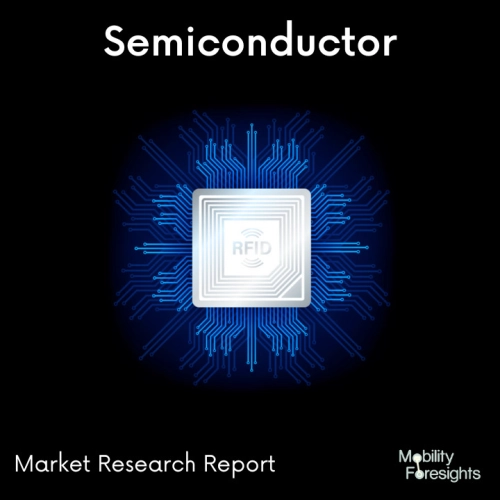
- Get in Touch with Us
Last Updated: Apr 25, 2025 | Study Period: 2023-2030
An automated SiC epitaxial film growth apparatus was created by integrating cutting-edge technologies from the semiconductor manufacturing equipment industry, including vacuum, transfer, and high-temperature control.
A silicon carbide (SiC) epitaxial layer could be created using the chemical vapour deposition (CVD) method. A common precursor for CVD of SiC with a wide range of acceptable deposition temperatures is methyltrichlorosilane (CH3SiCl3, MTS).The CVD process typically includes the kinetics of both gas-phase events and surface reactions.
Surface kinetic mechanisms of epitaxial SiC growth in the presence of the single precursor MTS diluted in H2 in a gaseous setting. The Si face with a surface site terminated by an open site or H atom is thought to be the deposition face.
Global SiC epitaxial CVD system accounted for $XX Billion in 2022 and is anticipated to reach $XX Billion by 2030, registering a CAGR of XX% from 2023 to 2030.
The G10-SiC high-temperature chemical vapour deposition (CVD) equipment has been introduced in Germany for the high-volume production of the newest silicon carbide (SiC) power devices on 150/200mm SiC wafers.
The G10-SiC system is based on the company's well-known G5 WW C 150mm platform and offers a versatile dual-wafer size configuration of 9x150mm and 6x200mm, which is thought to be crucial for the SiC industry's shift from 150mm (6-inch) to 200mm (8-inch) wafer diameter.
With sigma values of less than 2% for doping and thickness, the G10-SiC offers a wide range of device topologies, including single and double drift layer structures that adhere to strict 150mm uniformity standards. With minimal probability of particle defects due to the automated wafer loading, typical defect counts are less than 0.02/cm2.
The company's tried-and-true automated wafer cassette-to-cassette loading method with high-temperature wafer transfer serves as the foundation for the new platform. The G10-SiC is said to offer best-in-class wafer throughput and throughput per square metre when combined with high-growth-rate process capabilities, allowing semiconductor fabs to make the most of their limited cleanroom space.
This is a high-performance system of the most recent generation. The switch from current 150mm wafer technology is fully supported by the new dual wafer size arrangement, which also protects our customer's future investment.
Sl no | Topic |
1 | Market Segmentation |
2 | Scope of the report |
3 | Abbreviations |
4 | Research Methodology |
5 | Executive Summary |
6 | Introduction |
7 | Insights from Industry stakeholders |
8 | Cost breakdown of Product by sub-components and average profit margin |
9 | Disruptive innovation in the Industry |
10 | Technology trends in the Industry |
11 | Consumer trends in the industry |
12 | Recent Production Milestones |
13 | Component Manufacturing in US, EU and China |
14 | COVID-19 impact on overall market |
15 | COVID-19 impact on Production of components |
16 | COVID-19 impact on Point of sale |
17 | Market Segmentation, Dynamics and Forecast by Geography, 2023-2030 |
18 | Market Segmentation, Dynamics and Forecast by Product Type, 2023-2030 |
19 | Market Segmentation, Dynamics and Forecast by Application, 2023-2030 |
20 | Market Segmentation, Dynamics and Forecast by End use, 2023-2030 |
21 | Product installation rate by OEM, 2023 |
22 | Incline/Decline in Average B-2-B selling price in past 5 years |
23 | Competition from substitute products |
24 | Gross margin and average profitability of suppliers |
25 | New product development in past 12 months |
26 | M&A in past 12 months |
27 | Growth strategy of leading players |
28 | Market share of vendors, 2023 |
29 | Company Profiles |
30 | Unmet needs and opportunity for new suppliers |
31 | Conclusion |
32 | Appendix |