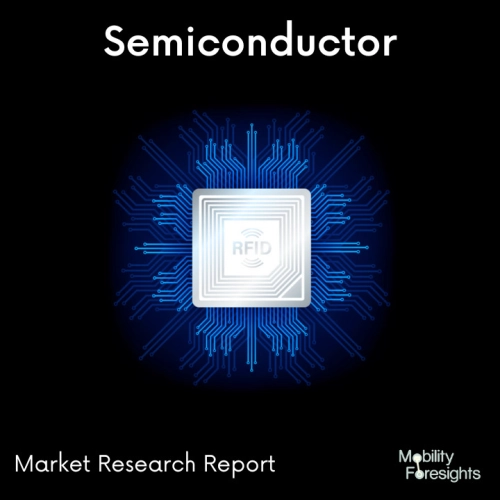
- Get in Touch with Us
Last Updated: Apr 25, 2025 | Study Period: 2024-2030
Because it is challenging to control doping and thickness in bulk growth, epitaxial growth is utilized to build active layers of SiC epitaxy equipment architectures with controlled doping density and thickness.
By using chemical vapor deposition, homoepitaxial growth technique has advanced significantly, enabling consistent control of a broad range of doping densities (1014â1019/cm3) in both n- and p-type materials.
Step-flow growth and regulating the carbon/silicon ratio, respectively, were used to achieve this. Even at a very high growth temperature (1600 °C), the gas phase and surface interactions may be accurately represented. Major extended and point defects in SiC epitaxial layers have been there and architectures, and the fundamental processes of defect creation and reduction during SiC epitaxy
The Global SiC epitaxy equipment Market accounted for $XX Billion in 2023 and is anticipated to reach $XX Billion by 2030, registering a CAGR of XX% from 2024 to 2030.
Incorporating cutting-edge technologies including vacuum technology, transfer technology, and high-temperature control technology that TEL has developed in the market for semiconductor manufacturing equipment, the Probus-SiC series is an automated SiC epitaxy equipment growth system.
TEL carefully considered the market needs that changed as the SiC industry grew before introducing the most cutting-edge technology into the machinery needed by the production site at all times. As a result, the equipment has the capabilities needed for mass production as well as process performance, including safety, maintenance, operability, and reliability. The performance of the equipment has been highly praised at mass production facilities across the world.
Coherent delivers SiC epitaxy equipment with best-in-class uniformity on wafers up to 200 mm in diameter. With the following capabilities, we provide a full SiC materials solution with flexible specifications:With or without buffer, thick epilayers; low-doped layers as thick as 150 m.P-n junctions, multilayer architectures, and different amounts of doping.
Structures buried or embedded and contact layers.a seamless flow of operations from R&D to mass production.utilizing effective buffer-layer technology, we achieve record-low defect density..prevents crystalline flaws from forming at the beginning of development.conversion rate from BPD to TED >99.8% 1 BPD per cm2.nables the technology of bipolar SiC devices.
.Layer homogeneity with LPE PE106 that is best in class.Latitudinally variable gas fluxe.TCS is used as a silicon precursor to achieve a high growth rate of 40 m/h..150 m and more formation of thick layers.very low doping levels
Sl no | Topic |
1 | Market Segmentation |
2 | Scope of the report |
3 | Abbreviations |
4 | Research Methodology |
5 | Executive Summary |
6 | Introduction |
7 | Insights from Industry stakeholders |
8 | Cost breakdown of Product by sub-components and average profit margin |
9 | Disruptive innovation in the Industry |
10 | Technology trends in the Industry |
11 | Consumer trends in the industry |
12 | Recent Production Milestones |
13 | Component Manufacturing in US, EU and China |
14 | COVID-19 impact on overall market |
15 | COVID-19 impact on Production of components |
16 | COVID-19 impact on Point of sale |
17 | Market Segmentation, Dynamics and Forecast by Geography, 2024-2030 |
18 | Market Segmentation, Dynamics and Forecast by Product Type, 2024-2030 |
19 | Market Segmentation, Dynamics and Forecast by Application, 2024-2030 |
20 | Market Segmentation, Dynamics and Forecast by End use, 2024-2030 |
21 | Product installation rate by OEM, 2023 |
22 | Incline/Decline in Average B-2-B selling price in past 5 years |
23 | Competition from substitute products |
24 | Gross margin and average profitability of suppliers |
25 | New product development in past 12 months |
26 | M&A in past 12 months |
27 | Growth strategy of leading players |
28 | Market share of vendors, 2023 |
29 | Company Profiles |
30 | Unmet needs and opportunity for new suppliers |
31 | Conclusion |
32 | Appendix |