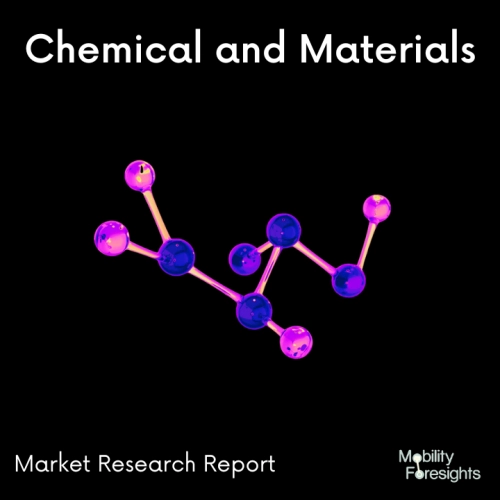
- Get in Touch with Us
Last Updated: Apr 25, 2025 | Study Period: 2024-2030
A low-lead brass alloy called silicon bronze typically contains 96% copper. The remaining portion can be created using silicon and a variety of different alloys, including those containing manganese, tin, iron, or zinc. Silicon bronze is renowned for its simple pouring characteristics, appealing surface quality, and high corrosion resistance capabilities, even when submerged in liquids and chemicals.
Because of its excellent casting qualities, silicon bronze was initially developed for the chemical industry. In addition to silicon's inherent self-lubricity, silicon bronze offers increased strength for superior load and bearing qualities. This is especially helpful when silicon bronze is used to make bearing cages, raceways, and spacers specifically for the aerospace sector.
The Global Silicon Bronze Market accounted for $XX Billion in 2023 and is anticipated to reach $XX Billion by 2030, registering a CAGR of XX% from 2024 to 2030.
Due to their outstanding mechanical strength, thermal characteristics, and tribological performance, silicon-bronze alloys are one of the most promising automotive materials for the development of rolling element bearings. The wear resistance of silicon-bronze alloys under dry sliding conditions is one of its key characteristics, and this is because the alloy surface develops a protective layer of tough particles.
The results of the experimental analysis demonstrated that adding MD to quicklime (CaO) reinforced silicon-bronze alloy composites and varying the weight percentages as 0, 2.5, 5, 7.5, and 10 for bearing material using a high temperature vacuum casting machine significantly improves the coefficient of friction and wear performance. For the purpose of creating samples, different weight percentages of MD as reinforcement (0, 2.5, 5, 7.5, and 10) were added to the base silicon-bronze alloy.
The high temperature furnace includes a heating element with a graphite crucible, a plunger with an 8 mm diameter tip, and a sensor for measuring temperature in infrared light. The silicon-bronze matrix alloy and marbled dust filler were initially warmed to 150°C in a separate furnace to ease internal tensions. As a result, the preheated basic silicon-bronze alloy was poured into a heated graphite crucible linked to the high temperature vacuum furnace above its melting temperature, which is 1100°C.
Sl no | Topic |
1 | Market Segmentation |
2 | Scope of the report |
3 | Abbreviations |
4 | Research Methodology |
5 | Executive Summary |
6 | Introduction |
7 | Insights from Industry stakeholders |
8 | Cost breakdown of Product by sub-components and average profit margin |
9 | Disruptive innovation in the Industry |
10 | Technology trends in the Industry |
11 | Consumer trends in the industry |
12 | Recent Production Milestones |
13 | Component Manufacturing in US, EU and China |
14 | COVID-19 impact on overall market |
15 | COVID-19 impact on Production of components |
16 | COVID-19 impact on Point of sale |
17 | Market Segmentation, Dynamics and Forecast by Geography, 2024-2030 |
18 | Market Segmentation, Dynamics and Forecast by Product Type, 2024-2030 |
19 | Market Segmentation, Dynamics and Forecast by Application, 2024-2030 |
20 | Market Segmentation, Dynamics and Forecast by End use, 2024-2030 |
21 | Product installation rate by OEM, 2023 |
22 | Incline/Decline in Average B-2-B selling price in past 5 years |
23 | Competition from substitute products |
24 | Gross margin and average profitability of suppliers |
25 | New product development in past 12 months |
26 | M&A in past 12 months |
27 | Growth strategy of leading players |
28 | Market share of vendors, 2023 |
29 | Company Profiles |
30 | Unmet needs and opportunity for new suppliers |
31 | Conclusion |
32 | Appendix |