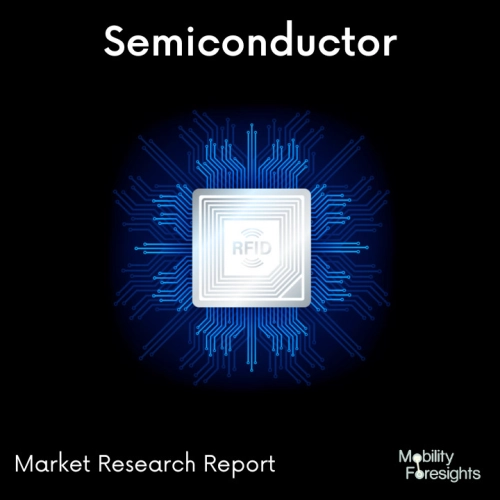
- Get in Touch with Us
Last Updated: Apr 25, 2025 | Study Period:
Silicon on insulator (SOI) technology in semiconductor manufacturing is the production of silicon semiconductor devices in a stacked silicon-insulator-silicon substrate to minimize parasitic capacitance inside the device and hence improve performance.
The silicon junction of SOI-based devices is located atop an electrical insulator, commonly silicon dioxide or sapphire, as opposed to traditional silicon-built devices. The choice of insulator is generally determined by the desired application, with sapphire utilized for high-performance radio frequency (RF) and radiation-sensitive applications and silicon dioxide used for reduced short-channel effects in other microelectronics devices.
The insulating layer and uppermost silicon layer vary greatly depending on the application. SOI technology is one of numerous manufacturing processes that allow for the continual miniaturization of microelectronic devices, sometimes known informally as Moore's Law extension.
SOI substrates are compatible with the vast majority of traditional fabrication techniques. In general, an SOI-based process may be established without the need for specialized equipment or extensive retooling of an existing plant.
Novel metrology needs to account for the buried oxide layer, as well as worries about differential stress in the uppermost silicon layer, are among the issues specific to SOI. The transistor's threshold voltage is affected by its history of operation and the voltage supplied to it, making modeling more difficult.
The biggest impediment to SOI deployment is the sharp rise in substrate costs, which adds to an anticipated increase in overall production costs.SOI MOSFETs are metal-oxide-semiconductor field-effect transistors (MOSFETs) in which a semiconductor layer, such as silicon or germanium, is produced atop an insulator layer, which may be a buried oxide (BOX) layer generated on a semiconductor substrate.
The computer industry has adopted SOI MOSFET transistors. SRAM designs can make use of the buried oxide layer. SOI MOSFETs are classified into two types: PDSOI (partially depleted SOI) and FDSOI (completely depleted SOI).
Because the sandwiched n-type film between the gate oxide (GOX) and buried oxide (BOX) is substantial in an n-type PD SOI MOSFET, the depletion area cannot cover the whole n region. As a result, PDSOI acts similarly to bulk MOSFETs.
TheGlobal Silicon-on-Insulator Substrate Marketaccounted for $XX Billion in 2023 and is anticipated to reach $XX Billion by 2030, registering a CAGR of XX% from 2024 to 2030.
Okmetic was one of the first silicon wafer providers to offer Silicon On Insulator technology and SOI wafers to the MEMS sector, and the business has now been mass manufacturing SOI wafers for years. SOI wafers are silicon wafers with a thin silicon coating on insulating oxide that demand a high level of technical ability to manufacture.
SOI wafers enable the production of cutting-edge MEMS, sensor, power, and RF devices used in automotive and healthcare applications, smart wristbands, smartphones, and tablets, as well as Internet of Things (IoT) applications that use sensor-provided data in device-to-device communication.
Bonding technique is used to make Okmetic's Silicon on Insulator (SOI) wafers. An insulating oxide layer separates two silicon wafers that are joined together. Sensing components and IC devices are often built on the top device layer. The buried oxide layer is a good electric insulator and etch-stop, but it may also be employed as a sacrificial layer.
The bottom handle wafer supports the structure but can also be used to seal it or as part of the sensing element or gadget. Okmetic's SOI wafers are wholly made in-house, allowing to closely control essential crystal and wafer characteristics to assure the finest quality SOI wafers.
1 | Market Segmentation |
2 | Scope of the report |
3 | Abbreviations |
4 | Research Methodology |
5 | Executive Summary |
6 | Introduction |
7 | Insights from Industry stakeholders |
8 | Cost breakdown of Product by sub-components and average profit margin |
9 | Disruptive innovation in the Industry |
10 | Technology trends in the Industry |
11 | Consumer trends in the industry |
12 | Recent Production Milestones |
13 | Component Manufacturing in US, EU and China |
14 | COVID-19 impact on overall market |
15 | COVID-19 impact on Production of components |
16 | COVID-19 impact on Point of sale |
17 | Market Segmentation, Dynamics and Forecast by Geography, 2024-2030 |
18 | Market Segmentation, Dynamics and Forecast by Product Type, 2024-2030 |
19 | Market Segmentation, Dynamics and Forecast by Application, 2024-2030 |
20 | Market Segmentation, Dynamics and Forecast by End use, 2024-2030 |
21 | Product installation rate by OEM, 2023 |
22 | Incline/Decline in Average B-2-B selling price in past 5 years |
23 | Competition from substitute products |
24 | Gross margin and average profitability of suppliers |
25 | New product development in past 12 months |
26 | M&A in past 12 months |
27 | Growth strategy of leading players |
28 | Market share of vendors, 2023 |
29 | Company Profiles |
30 | Unmet needs and opportunity for new suppliers |
31 | Conclusion |
32 | Appendix |