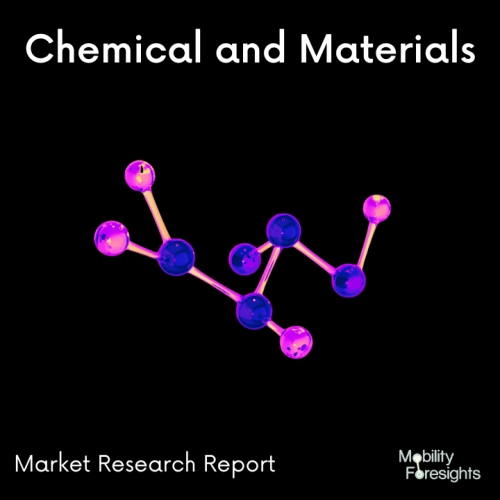
- Get in Touch with Us
Last Updated: Apr 25, 2025 | Study Period: 2024-2030
Compound made of silicone that can be used in thermosetting transfer moulding systems for electrical and electronic components. On the basis of silicone resin, it incorporates a variety of fillers and additives.
The material is extremely resistant to heat, cold, and deterioration. Because its characteristics remain constant under a range of temperatures and frequencies, it offers stable electrical insulation.
Mould releaseability is also quite good. It reacts to the moulding of materials that demand great heat resistance. The majority of moulding compounds are composite materials made of phenolic hardeners, silicas, catalysts, pigments, and mould release agents.
The Global Silicone molding compounds market accounted for $XX Billion in 2023 and is anticipated to reach $XX Billion by 2030, registering a CAGR of XX% from 2024 to 2030.
Silicone and plastic are both included in equal measure in silicone moulding compositions. It is used in place of rubber to create items like gaskets, seals, bearings, and even insulation around wires to shield them from the elements.
The ability to mould this type of material into various shapes without the use of extra hardening agents like waxesâjust time and heatâis a significant advantage. They can endure temperatures up to 250 degrees Celsius, which is greater than most rubbers can.
Silicone moulding compounds are utilised in electrical applications, such as to insulate an electric circuit or component from outside influences.Silicone has a great resistance to electrical breakdown, making it an excellent material for insulating electrical components from outside influences such as water vapour, pressure changes, etc.
Since silicone is one of the few plastics that can survive a wide range of circumstances without degrading chemically (a process known as thermal ageing), this substance will not deteriorate even when exposed to extremely high or low temperatures.
Due to their strong corrosion resistance in situations with low relative humidity levels and moisture exposure, silicone moulding compounds. Press moulding is an injection moulding technique where molten polymer is pressed into a prefabricated metal die while being subjected to high pressure and temperature.
Sl no | Topic |
1 | Market Segmentation |
2 | Scope of the report |
3 | Abbreviations |
4 | Research Methodology |
5 | Executive Summary |
6 | Introdauction |
7 | Insights from Industry stakeholders |
8 | Cost breakdown of Product by sub-components and average profit margin |
9 | Disruptive innovation in theIndustry |
10 | Technology trends in the Industry |
11 | Consumer trends in the industry |
12 | Recent Production Milestones |
13 | Component Manufacturing in US, EU and China |
14 | COVID-19 impact on overall market |
15 | COVID-19 impact on Production of components |
16 | COVID-19 impact on Point of sale |
17 | Market Segmentation, Dynamics and Forecast by Geography, 2024-2030 |
18 | Market Segmentation, Dynamics and Forecast by Product Type, 2024-2030 |
19 | Market Segmentation, Dynamics and Forecast by Application, 2024-2030 |
20 | Market Segmentation, Dynamics and Forecast by End use, 2024-2030 |
21 | Product installation rate by OEM, 2023 |
22 | Incline/Decline in Average B-2-B selling price in past 5 years |
23 | Competition from substitute products |
24 | Gross margin and average profitability of suppliers |
25 | New product development in past 12 months |
26 | M&A in past 12 months |
27 | Growth strategy of leading players |
28 | Market share of vendors, 2023 |
29 | Company Profiles |
30 | Unmet needs and opportunity for new suppliers |
31 | Conclusion |
32 | Appendix |