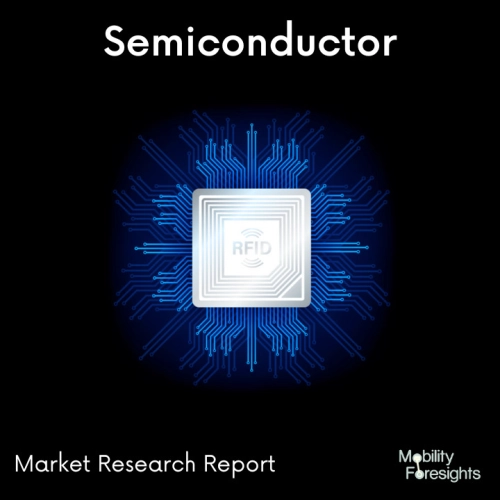
- Get in Touch with Us
Last Updated: Apr 27, 2025 | Study Period: 2023-2030
A silicon-based semiconductor known as a SiC wafer. The crystal is etched to create a silicon carbide wafer, which is a crystalline substance. Usually, it can be utilised for power semiconductor devices because it is thin enough.
The other kind is a specific kind of insulator. In power semiconductors, the temperature range has a significant impact on the electrical and magnetic fields. A silicon carbide wafer is bidirectionally conductible.
A semiconductor with superior electrical and thermal characteristics is a SiC wafer. It is a powerful semiconductor that is suitable for a wide range of uses. In addition to having a very high level of hardness, it has strong thermal resistance.
The Global Single crystal SiC wafers market accounted for $XX Billion in 2021 and is anticipated to reach $XX Billion by 2030, registering a CAGR of XX% from 2022 to 2030.
Both the supply and demand sides of the semiconductor manufacturing business were impacted by the COVID -19 pandemic. The global lockdowns and semiconductor facility closures added to the scarcity of supplies.
The SiC wafer market also showed negative repercussions. Many of these symptoms, though, are most likely to disappear quickly. Governments throughout the world may resurrect industrial growth by taking measures to promote the automobile and semiconductor sectors.
SiC wafers with a diameter of 6 inches (150 mm), which would be processed and integrated into SiC-based power semiconductors, were first produced in bulk by Showa Denko KK.
The SiC single-crystal wafer, which has a six-inch diameter and may be utilised in large-area power devices for use in automobiles and rapid-transit railways, has been successfully developed by Nippon Steel Corporation.
The six-inch diameter silicon carbide single-crystal wafer, created by Nippon Steel Corporation, is a crucial component for the future mass manufacture and widespread use of high-performance, high-power semiconductor devices.
When utilized in various electronic devices, SiC wafer can reduce the power-conversion loss to less than half when compared to silicon wafer, which is the material used to make diode, transistor, and other semiconductor devices.
It is appropriate for high-voltage, high-temperature uses in solar power generation, automotive (EV, HEV, etc.), and other power electronics applications because it has outstanding high-voltage and heat resistance capabilities.
The six-inch SiC wafer is anticipated to lower manufacturing costs and boost production efficiency for SiC devices.
The sublimation-recrystallization process is typically used to create SiC single crystals.The development of SiC single crystals is accomplished in manufacturing equipment heated to temperatures over 2500 degrees Celsius by causing vapor evaporated from SiC material in powder form to recrystallize on top of seed crystals.
The goal is to complete the sale of Nippon Steel Materials' 6-inch SiC single crystal wafer products and contribute to the global adoption of SiC technology on a large scale.The six-inch SiC wafer is anticipated to lower manufacturing costs and boost production efficiency for SiC devices.
More high-quality SiC substrates are anticipated due to the rising demand for them, which is being driven by the adoption of EVs. One single-crystal SiC substrate can yield 10 times more high-quality SiC substrates to SmartCut SiC technology.
A high surface quality (lower amount of particles) to the particular engineering techniques performed to the final surface that are related with improved defect metrology, in addition to the 10 reuse, is the strength of the SmartCut SiC technology.
These enhancements reduce the density of induced epi-grown defects, increasing the yield of devices larger than 20 mm by more than 10%. Additionally, SmartCut, a PolySiC handling wafer, is intended to have ultra-high conductivity onto which a thin layer of single-crystal SiC is bonded.
A single crystal SiC ingot is used to make a SiC wafer. The focal point of a pulsed laser beam with a transmission wavelength to the ingot is placed inside the ingot at a predefined depth from the ingot's flat surface, the predetermined depth matching to the thickness of the wafer to be manufactured.
The pulsed laser beam is applied to the ingot, forming a separation layer that allows the wafer to be separated from the ingot.
The wafer is separated from the ingot along the separation layer, and a flat surface is made by grinding a rough separation surface remaining after separating the wafer, reducing the roughness of the upper surface of the ingot to flatten it.
The current invention relates to a technique for creating a SiC wafer from a single crystal SiC ingot. A single crystal SiC ingot, in particular, has a high hardness, making it difficult to cut with a wire saw. As a result, considerable time is required for ingot cutting, resulting in a decrease in output.
Sl no | Topic |
1 | Market Segmentation |
2 | Scope of the report |
3 | Abbreviations |
4 | Research Methodology |
5 | Executive Summary |
6 | Introduction |
7 | Insights from Industry stakeholders |
8 | Cost breakdown of Product by sub-components and average profit margin |
9 | Disruptive innovation in the Industry |
10 | Technology trends in the Industry |
11 | Consumer trends in the industry |
12 | Recent Production Milestones |
13 | Component Manufacturing in US, EU and China |
14 | COVID-19 impact on overall market |
15 | COVID-19 impact on Production of components |
16 | COVID-19 impact on Point of sale |
17 | Market Segmentation, Dynamics and Forecast by Geography, 2022-2030 |
18 | Market Segmentation, Dynamics and Forecast by Product Type, 2022-2030 |
19 | Market Segmentation, Dynamics and Forecast by Application, 2022-2030 |
20 | Market Segmentation, Dynamics and Forecast by End use, 2022-2030 |
21 | Product installation rate by OEM, 2022 |
22 | Incline/Decline in Average B-2-B selling price in past 5 years |
23 | Competition from substitute products |
24 | Gross margin and average profitability of suppliers |
25 | New product development in past 12 months |
26 | M&A in past 12 months |
27 | Growth strategy of leading players |
28 | Market share of vendors, 2022 |
29 | Company Profiles |
30 | Unmet needs and opportunity for new suppliers |
31 | Conclusion |
32 | Appendix |