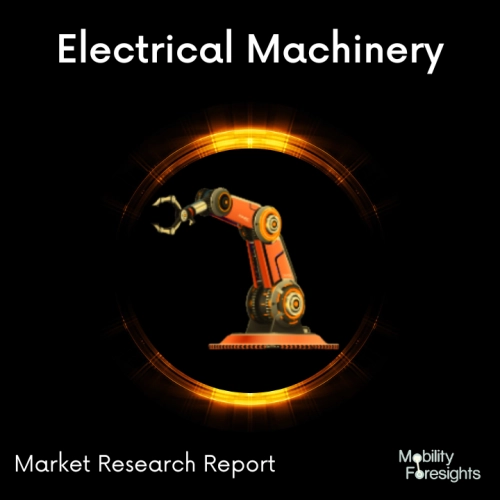
- Get in Touch with Us
Last Updated: Apr 25, 2025 | Study Period: 2022-2030
One separate type of bearing is the single-row cylindrical roller bearing.A single-row cylindrical roller ring typically consists of the following four main components:rollers, cage, inner ring, and outer ring Two bearing ring ribs typically act as guides for the rollers.
In contrast to ball bearings, which employ balls as their rolling parts, cylindrical roller bearings use cylinders. As a result, the outer ring and rollers have a larger (linear) contact area, which allows for the distribution of loads across a larger surface.
As a result, they are appropriate for high speeds and have a reasonably large radial load capacity. Double-row cylindrical roller bearings are utilised largely in precision machine tools and have a high radial stiffness.
Cylindrical roller bearings can be found in a variety of designs on the market.They differ based on the number of roller rows (typically one, two, or four) and whether or not a cage is present.The bearing can't have more rows because it doesn't have a cage, which helps it support even heavier radial loads.
TheGlobal Single-Row Cylindrical Roller Bearings marketaccounted for $XX Billion in 2021 and is anticipated to reach $XX Billion by 2030, registering a CAGR of XX% from 2022 to 2030.
Roller bearings are manufactured by SKF company, the roller bearings are used in rotary applications to replace sliding movement with low friction, rolling motion. The principal types of roller bearings are cylindrical, spherical, and tapered.
the inner ring-shaped double edge cannot be separated from the two free edges like roller separation does; NU form: The outer ring has two edges, unlike the inner ring, which has only one edge and cannot be separated from either side; NF:
The outer ring has a single file and only one free fall from in a double ring-shaped edge without roller separation; NJ form: The inner roller cannot separate the outer ring, which has a double edge and can only be removed from the freedom side;
The inner side of a single file can be detached from the side of freedom, but the inner edge side of a locating ring can be removed. The outer ring of the NUP shape has a double edge and does not have roller separation.
Double row, NN, NNU, and four row cylindrical roller bearings are examples of cylindrical roller bearings. Cylindrical roller bearing with bolt holder and stamping steel cage, large size or for high-speed rotation with brass turning cage, double row or four row, to extend the bearing's service life.
A new production line for Single-Row Cylindrical Roller Bearings was introduced by ZKL GROUP in the Czech Republic last year. This line creates single-row cylindrical roller bearings with a wide range of hole sizes (d = 50 to 250 mm) and outer diameters (D = 120 to 350 mm), as well as full complement cylindrical roller bearings with the N, NJ, NU, and NUP designations. Additionally, the ZKL Group produces sealed cylindrical roller bearing units in addition to cylindrical roller bearings for wagon axles.
With the aid of new technologies, cylindrical roller bearings may now be produced with an internal design known as NEW FORCE that has been optimized for improved longevity, operational accuracy, reduced noise, and reduced energy loss. These qualities are attained by refining the bearing's internal geometry and utilizing materials that adhere to the exacting requirements of the NEW FORCE design.
To enhance their mechanical and fatigue characteristics, metallurgical techniques have been developed in collaboration with suppliers. Years of collaboration with reputable suppliers ensure a constant process of material parameter improvement. Internal regulations that outline the chemical makeup, purity, and microstructure of ZKL bearings guarantee the materials' quality.
The greater dynamic and static load capacities of NEW FORCE cylindrical roller bearings are similar to those of the top bearing producers in the world. Following this advancement, dynamic load ratings improved over older ZKL cylindrical roller bearings by an average of 25â30%.
This outcome was made possible by a completely new internal bearing shape design and optimization technique that makes use of a sophisticated computational method based on finite element techniques. Above all, the raceway of the bearing rings, the rollers' rolling surface, and the front retaining collars all contribute to the load capacity of the bearings by restricting their rotational speed and attenuating their noise.
The suggested internal bearing geometry profiles guarantee an ideal distribution of stress where different bearing components come into contact with one another. New manufacturing techniques have improved the structure of the contact surfaces, allowing for better lubrication film development that lessens bearing wear. As a result, operational life is significantly increased.
Cylindrical roller bearings made by ZKL NEW FORCE are typically produced with steel and solid brass cages. For wagon axles, cylindrical roller bearings are installed with solid brass or cages made of a specifically designed composite material (PA66-GF25), which exhibits exceptional strength and stability while in use.
Cylindrical roller bearings made by ZKL NEW FORCE often have greater radial and axial load-carrying capacities, less power loss, quieter operation, and longer service lives.
Sl no | Topic |
1 | Market Segmentation |
2 | Scope of the report |
3 | Abbreviations |
4 | Research Methodology |
5 | Executive Summary |
6 | Introduction |
7 | Insights from Industry stakeholders |
8 | Cost breakdown of Product by sub-components and average profit margin |
9 | Disruptive innovation in the Industry |
10 | Technology trends in the Industry |
11 | Consumer trends in the industry |
12 | Recent Production Milestones |
13 | Component Manufacturing in US, EU and China |
14 | COVID-19 impact on overall market |
15 | COVID-19 impact on Production of components |
16 | COVID-19 impact on Point of sale |
17 | Market Segmentation, Dynamics and Forecast by Geography, 2022-2030 |
18 | Market Segmentation, Dynamics and Forecast by Product Type, 2022-2030 |
19 | Market Segmentation, Dynamics and Forecast by Application, 2022-2030 |
20 | Market Segmentation, Dynamics and Forecast by End use, 2022-2030 |
21 | Product installation rate by OEM, 2022 |
22 | Incline/Decline in Average B-2-B selling price in past 5 years |
23 | Competition from substitute products |
24 | Gross margin and average profitability of suppliers |
25 | New product development in past 12 months |
26 | M&A in past 12 months |
27 | Growth strategy of leading players |
28 | Market share of vendors, 2022 |
29 | Company Profiles |
30 | Unmet needs and opportunity for new suppliers |
31 | Conclusion |
32 | Appendix |