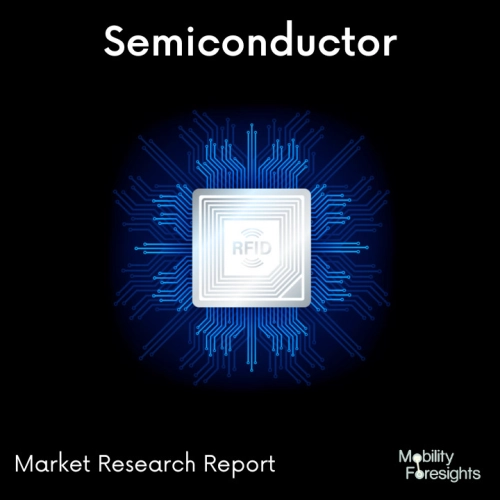
- Get in Touch with Us
Last Updated: Apr 25, 2025 | Study Period: 2023-2030
The goal of the wafer cleaning procedure is to eliminate chemical and particle contaminants while preserving the substrate or wafer surface. The wafer surface must be kept in good condition so that roughness, corrosion, or pitting do not undermine the effects of the wafer cleaning procedure.
Silicon wafers are cleaned to eliminate organic contaminants. In the process, the silicon is oxidised, leaving a thin layer of oxide on the wafer's surface that needs to be removed if a pure silicon surface is sought.
This level-1 procedure calls for a minimal degree of INRF safety certification. To remove particulates, metallics, and other contaminants, a batch of wafers was simply submerged in the cleaning chemistry in an exposed wet bench.
Cryogenic technology is utilised in the semiconductor industry's single wafer cryokinetic cleaning systems to clean wafers, which are thin discs of material used in the production of electronics.
It entails thoroughly rinsing the wafers to eliminate all residue before blasting them with cold, high-pressure gases to clear them of impurities and contaminants.
The Global Single Wafer Cryokinetic Cleaning System market accounted for $XX Billion in 2022 and is anticipated to reach $XX Billion by 2030, registering a CAGR of XX% from 2023 to 2030.
For processing 200/300mm wafers, the ANTARES family of fully automated single-wafer CryoKinetic equipment is used. Cryogenic aerosol technology is used by each system to securely eliminate nanoscale particles from device surfaces.
This all-dry method removes flaws without harming the wafer surface, even on metal and low-k coatings, in contrast to typical wet technologies. The ANTARES series offers proven yield-enhancing defect elimination without wafer charging, metal corrosion, or watermarks on hydrophobic surfaces. The method works with all types of materials.
Low surface tension alcohol solutions have historically been used in semiconductor cleaning to speed up the drying process. Pattern collapse during drying has become a significant problem, nevertheless, as a result of continuing semiconductor scaling and the usage of multi-layer architectures in extremely advanced devices.
In response, TEL created a technique for drying without pattern collapse that makes use of a supercritical fluid, bringing the technology to the market as machinery for mass manufacturing.
Sl no | Topic |
1 | Market Segmentation |
2 | Scope of the report |
3 | Abbreviations |
4 | Research Methodology |
5 | Executive Summary |
6 | Introduction |
7 | Insights from Industry stakeholders |
8 | Cost breakdown of Product by sub-components and average profit margin |
9 | Disruptive innovation in the Industry |
10 | Technology trends in the Industry |
11 | Consumer trends in the industry |
12 | Recent Production Milestones |
13 | Component Manufacturing in US, EU and China |
14 | COVID-19 impact on overall market |
15 | COVID-19 impact on Production of components |
16 | COVID-19 impact on Point of sale |
17 | Market Segmentation, Dynamics and Forecast by Geography, 2023-2030 |
18 | Market Segmentation, Dynamics and Forecast by Product Type, 2023-2030 |
19 | Market Segmentation, Dynamics and Forecast by Application, 2023-2030 |
20 | Market Segmentation, Dynamics and Forecast by End use, 2023-2030 |
21 | Product installation rate by OEM, 2023 |
22 | Incline/Decline in Average B-2-B selling price in past 5 years |
23 | Competition from substitute products |
24 | Gross margin and average profitability of suppliers |
25 | New product development in past 12 months |
26 | M&A in past 12 months |
27 | Growth strategy of leading players |
28 | Market share of vendors, 2023 |
29 | Company Profiles |
30 | Unmet needs and opportunity for new suppliers |
31 | Conclusion |
32 | Appendix |