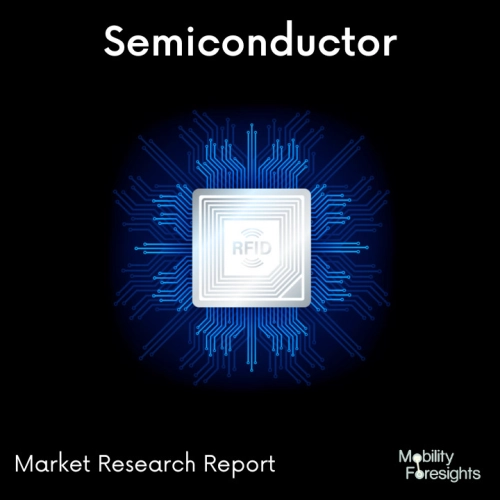
- Get in Touch with Us
Last Updated: Apr 25, 2025 | Study Period: 2023-2030
One of the key pieces of equipment for the post-process of making semiconductors, along with moulding equipment, is the singulation system. In order to provide the best singulation technique for each type of manufactured good, they develop dicers as a key component of singulation systems.
Additionally, the high throughput of singularized product handlers helps to increase customer productivity. Singulation systems keep cutting precision at its highest level by adjusting extremely warped moulded products before cutting them and monitoring products with a camera as they are being cut for misalignment that could be brought on by their expansion, contraction, or deformation.
The Global Singulation Machine market accounted for $XX Billion in 2022 and is anticipated to reach $XX Billion by 2030, registering a CAGR of XX% from 2023 to 2030.
New LED Package Singulation Blades are launched by Kulicke & Soffa. In addition to offering a "plug and play" solution for the majority of dicer spindle setups, the OptoTM blades significantly enhance CoO.
The hub-type design further increases machine productivity and machine use by allowing for a variety of dicer configurations for package singulation. By enhancing stability and extending blade life, OptoTM Hub and Hubless Blades dramatically increase the quality, precision, and productivity of LED package singulation.
The new OptoTM blades stand out for their appealing cost of ownership thanks to continuously extended blade life, 100% pre-dressed to reduce on-site dressing processes, and an optional kerf adjustment capability to satisfy specific application needs. Higher feed speeds have allowed for significant UPH improvement in several applications.
The innovative OptoTMceramic blade uses a special electroplating technique to provide a blade life that can be up to three times longer than that of conventional resin/metal bonded blades with little kerf change and blade wear.
The innovative design produces the best cut quality, reduces machine downtime for blade replacements, permits faster feed rates, and boosts productivity.
The new OptoTMPCB blade for PCB & composite material substrates features an improved design that delivers uniform vertical wear, retaining cutting power and constant sawn package dimensions, obviating the need for in-process dressing processes. High singulation quality is achieved without the usual whisker problems because of the optional "slits' ' feature, which enhances blade cooling.
Sl no | Topic |
1 | Market Segmentation |
2 | Scope of the report |
3 | Abbreviations |
4 | Research Methodology |
5 | Executive Summary |
6 | Introduction |
7 | Insights from Industry stakeholders |
8 | Cost breakdown of Product by sub-components and average profit margin |
9 | Disruptive innovation in the Industry |
10 | Technology trends in the Industry |
11 | Consumer trends in the industry |
12 | Recent Production Milestones |
13 | Component Manufacturing in US, EU and China |
14 | COVID-19 impact on overall market |
15 | COVID-19 impact on Production of components |
16 | COVID-19 impact on Point of sale |
17 | Market Segmentation, Dynamics and Forecast by Geography, 2023-2030 |
18 | Market Segmentation, Dynamics and Forecast by Product Type, 2023-2030 |
19 | Market Segmentation, Dynamics and Forecast by Application, 2023-2030 |
20 | Market Segmentation, Dynamics and Forecast by End use, 2023-2030 |
21 | Product installation rate by OEM, 2023 |
22 | Incline/Decline in Average B-2-B selling price in past 5 years |
23 | Competition from substitute products |
24 | Gross margin and average profitability of suppliers |
25 | New product development in past 12 months |
26 | M&A in past 12 months |
27 | Growth strategy of leading players |
28 | Market share of vendors, 2023 |
29 | Company Profiles |
30 | Unmet needs and opportunity for new suppliers |
31 | Conclusion |
32 | Appendix |