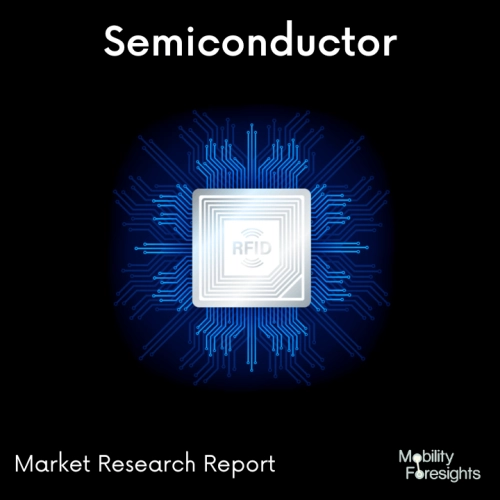
- Get in Touch with Us
Last Updated: Apr 25, 2025 | Study Period: 2024-2030
Permanent magnets made using a metallurgical process known as sintering, which entails heating and compacting (finely crushed) magnetic powder into the appropriate shape and size, are referred to as sintered magnets. The best method for creating permanent sintered magnets is liquid phase sintering. These magnets are machined after sintering to achieve dimensional correctness and make them ready for use.
Sintered magnets are strong and demonstrate the high magnetic strength needed for the majority of industrial applications. These magnets work well and produce a significant amount of output in devices including servo motors, electric motors, generators, alternators, and hard drives. They are transforming energy storage and power generating.
The Global Sintered magnet market accounted for $XX Billion in 2023 and is anticipated to reach $XX Billion by 2030, registering a CAGR of XX% from 2024 to 2030.
SURA MAGNETS produce sintered rare Earth magnets. Fine powders are compressed under high pressure in a magnetic field that is aligning, then they are sintering into solid shapes. The magnet shape will need to be machined to attain near tolerances because it is rough after sintering. The range of complex shapes that can be squeezed in this way is constrained.The strongest magnets available today are anisotropic sintered rare earth magnets made from NdFeB or SmCo.
The NEOREC55 line of NdFeB sintered magnets, developed by TDK Corporation, boasts the highest energy products in the market using current production techniques. To reduce oxidation throughout the production process and enhance saturation magnetization, TDK uses a unique low-oxygen technique. Without changing the current dry method. powder control technology is applied to increase the magnetic orientation of the compressed body and significantly improve magnetic properties. A sufficient magnetization has also been made possible by better magnetization in tiny magnetising fields.
Sl no | Topic |
1 | Market Segmentation |
2 | Scope of the report |
3 | Abbreviations |
4 | Research Methodology |
5 | Executive Summary |
6 | Introduction |
7 | Insights from Industry stakeholders |
8 | Cost breakdown of Product by sub-components and average profit margin |
9 | Disruptive innovation in the Industry |
10 | Technology trends in the Industry |
11 | Consumer trends in the industry |
12 | Recent Production Milestones |
13 | Component Manufacturing in US, EU and China |
14 | COVID-19 impact on overall market |
15 | COVID-19 impact on Production of components |
16 | COVID-19 impact on Point of sale |
17 | Market Segmentation, Dynamics and Forecast by Geography, 2024-2030 |
18 | Market Segmentation, Dynamics and Forecast by Product Type, 2024-2030 |
19 | Market Segmentation, Dynamics and Forecast by Application, 2024-2030 |
20 | Market Segmentation, Dynamics and Forecast by End use, 2024-2030 |
21 | Product installation rate by OEM, 2023 |
22 | Incline/Decline in Average B-2-B selling price in past 5 years |
23 | Competition from substitute products |
24 | Gross margin and average profitability of suppliers |
25 | New product development in past 12 months |
26 | M&A in past 12 months |
27 | Growth strategy of leading players |
28 | Market share of vendors, 2023 |
29 | Company Profiles |
30 | Unmet needs and opportunity for new suppliers |
31 | Conclusion |
32 | Appendix |