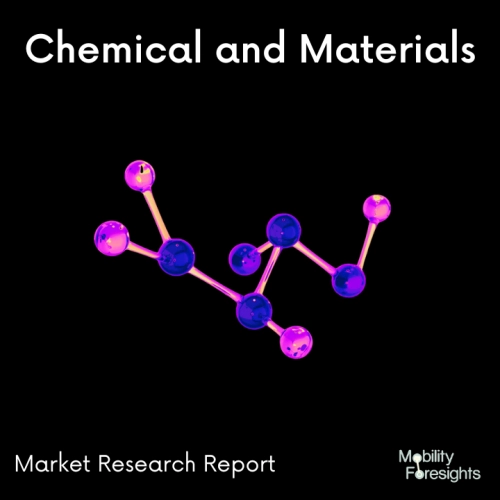
- Get in Touch with Us
Last Updated: Apr 25, 2025 | Study Period: 2023-2030
The emergence of new technology, such as smartphones, has revolutionized the way we communicate and receive information. New adhesive products must keep up with the ever-changing advancements, and local tech companies are continuing to develop new magnet bonding adhesive solutions that meet the demands of the industry.
This type of adhesive is becoming increasingly popular among smartphone producers, due to its clear advantages over traditional adhesives. A magnet bonding adhesive is a combination of a polymer and magnetic particles, making it incredibly attractive to manufacturers.
The magnetic effect of the adhesive allows it to stick to a surface without using any additional fasteners, meaning that there is no need to pre-drill or tap holes. Additionally, the unique feature of this adhesive makes re-positioning and removal much easier than with traditional adhesives, substantially reducing time and resources spent on production.
These adhesives also have improved thermal resistance versus traditional adhesives, making them especially helpful in the harsh environments that many mobile phone components must endure. With the development of high-temperature resistant adhesive products, manufacturers can take on heat-sensitive components without worrying about the adhesive.
This means that components with larger magnetic properties can be used with greater reliability and in turn enhance the device's performance.
With the push of the smartphone industry being to make devices lighter, smaller and more functional, magnet bonding adhesive products offer the perfect solution.
As the development of adhesives continues to improve and the smartphone industry continues to grow, magnet bonding adhesives have set the new standard in terms of mobility and performance.
The Global smartphone magnet bonding adhesives market accounted for $XX Billion in 2022 and is anticipated to reach $XX Billion by 2030, registering a CAGR of XX% from 2023 to 2030.
Krylex Performance Adhesives for Bonding Magnets and Batteries in Mobile Devices. The number of battery cells and magnets utilised in mobile and wearable device components as well as related accessories like wireless charging pads and charge cases has significantly increased as a result of the ongoing rise in these devices.
As a result, in order to successfully bond magnets and batteries, adhesives must meet strict performance standards for bond strength and related reliability upgrades. A battery and a magnet can be bonded using adhesives that meet very similar key requirements.
If adhesives are used in magnets or batteries, their performance may be affected if the temperatures reached during the thermal cure cycles are higher than 60 to 80 degrees Celsius. Adhesives must therefore offer strong, dependable attachment while staying below this temperature threshold. There has never been more need for portable power with high density.
The most common type of battery used in modern portable and mobile electronics is lithium-ion technology. The manufacturers of these devices select these batteries because of their high cycle life and large energy capacity, which allow for repeated charging and discharging without deterioration.
While research into new battery technology is being driven by huge investment. For the foreseeable future, lithium-ion batteries are probably going to continue to be the most popular technology. However, attempts are still being made to advance current Li-ion technology to the next level.
Thus, going forward, adhesive products that satisfy the specifications for bonding Lithium-ion batteries will be essential. If temperatures are outside of a specified manufacturing window, lithium-ion batteries will suffer.
It is preferable that the batteries experience temperature excursions of no more than 60C during assembly and fixing. When using an adhesive, there is a genuine danger of damage to the lithium plating and significant degradation of the battery life cycle if the upper-temperature limit is exceeded.Neodymium magnets are the most popular kind of magnet utilised in electronic device assemblies.
Usually, plating is needed on neodymium magnets to prevent corrosion. The magnet will quickly oxidise without the coating, which will have a detrimental effect on performance.
Sl no | Topic |
1 | Market Segmentation |
2 | Scope of the report |
3 | Abbreviations |
4 | Research Methodology |
5 | Executive Summary |
6 | Introduction |
7 | Insights from Industry stakeholders |
8 | Cost breakdown of Product by sub-components and average profit margin |
9 | Disruptive innovation in the Industry |
10 | Technology trends in the Industry |
11 | Consumer trends in the industry |
12 | Recent Production Milestones |
13 | Component Manufacturing in US, EU and China |
14 | COVID-19 impact on overall market |
15 | COVID-19 impact on Production of components |
16 | COVID-19 impact on Point of sale |
17 | Market Segmentation, Dynamics and Forecast by Geography, 2023-2030 |
18 | Market Segmentation, Dynamics and Forecast by Product Type, 2023-2030 |
19 | Market Segmentation, Dynamics and Forecast by Application, 2023-2030 |
20 | Market Segmentation, Dynamics and Forecast by End use, 2023-2030 |
21 | Product installation rate by OEM, 2023 |
22 | Incline/Decline in Average B-2-B selling price in past 5 years |
23 | Competition from substitute products |
24 | Gross margin and average profitability of suppliers |
25 | New product development in past 12 months |
26 | M&A in past 12 months |
27 | Growth strategy of leading players |
28 | Market share of vendors, 2023 |
29 | Company Profiles |
30 | Unmet needs and opportunity for new suppliers |
31 | Conclusion |
32 | Appendix |