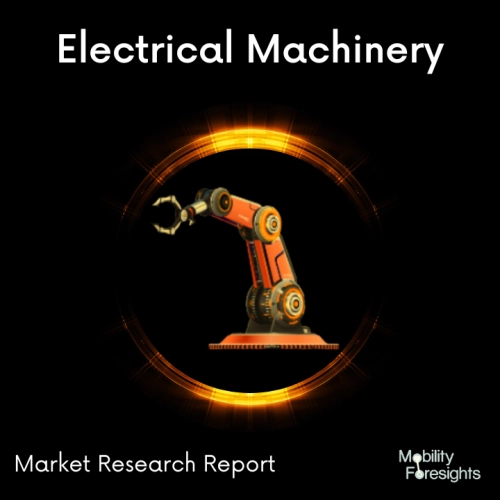
- Get in Touch with Us
Last Updated: Apr 25, 2025 | Study Period: 2024-2030
The measurement of cell efficiency is the most basic method for characterizing solar cells. The comparison of devices produced at various businesses and laboratories using various technologies is made possible by standard testing.
Building a system that simultaneously satisfies all the aforementioned requirements is challenging and expensive. The modest, custom-built testers used in the majority of research labs only closely resemble the aforementioned conditions. Results from "in-house" testing are frequently only rough estimates.
The Global Solar Cell Testing Machine market accounted for $XX Billion in 2023 and is anticipated to reach $XX Billion by 2030, registering a CAGR of XX% from 2024 to 2030.
Only by improving quality, creating them more cheaply, and making them safer will solar cells withstand the steep price decline in recent years.
Every day, solar cells are subjected to harsh environmental conditions. Storms, hail, rain, and extreme temperature changes shouldn't have an impact on how well the product works.
If they are to have the intended life expectancy of 40 years without being harmed, they must be able to endure the weight of snow, ice, and installation. Both electrical and mechanical qualities must meet these high demands.
However, there are no test standards for component mechanical requirements. Standardised quality assurance rules for solar cells do not exist, other than internal individual contract clauses between suppliers and manufacturers.
Examples of production control for the various stages of production of thick-film cells testing applications are introduced in order to better understand how destructive material testing is utilised in the manufacture of solar cells and modules.
Electrical parts known as solar cells or photovoltaic cells transform the radiant energy present in light directly into electrical energy.
Silicon, either monocrystalline or polycrystalline, is used to make thick-film solar cells. They have a high efficiency (above 20%), which is why they are commonly used in Central Europe.
They are distinguished by a high level of efficiency per surface area unit as well. Depending on the type of solar cell, testing requirements may change significantly because the various technologies in use may result in fundamentally different designs.
Sl no | Topic |
1 | Market Segmentation |
2 | Scope of the report |
3 | Abbreviations |
4 | Research Methodology |
5 | Executive Summary |
6 | Introduction |
7 | Insights from Industry stakeholders |
8 | Cost breakdown of Product by sub-components and average profit margin |
9 | Disruptive innovation in the Industry |
10 | Technology trends in the Industry |
11 | Consumer trends in the industry |
12 | Recent Production Milestones |
13 | Component Manufacturing in US, EU and China |
14 | COVID-19 impact on overall market |
15 | COVID-19 impact on Production of components |
16 | COVID-19 impact on Point of sale |
17 | Market Segmentation, Dynamics and Forecast by Geography, 2024-2030 |
18 | Market Segmentation, Dynamics and Forecast by Product Type, 2024-2030 |
19 | Market Segmentation, Dynamics and Forecast by Application, 2024-2030 |
20 | Market Segmentation, Dynamics and Forecast by End use, 2024-2030 |
21 | Product installation rate by OEM, 2023 |
22 | Incline/Decline in Average B-2-B selling price in past 5 years |
23 | Competition from substitute products |
24 | Gross margin and average profitability of suppliers |
25 | New product development in past 12 months |
26 | M&A in past 12 months |
27 | Growth strategy of leading players |
28 | Market share of vendors, 2023 |
29 | Company Profiles |
30 | Unmet needs and opportunity for new suppliers |
31 | Conclusion |
32 | Appendix |