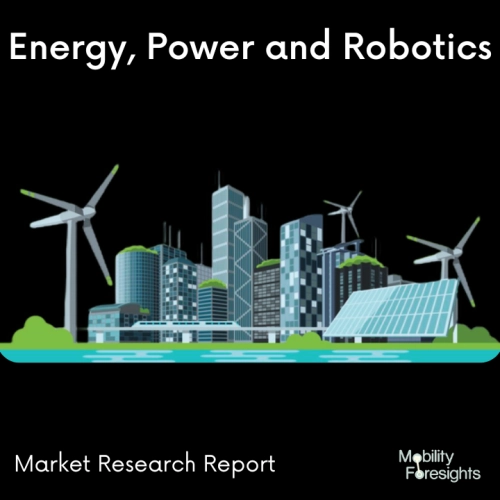
- Get in Touch with Us
Last Updated: Apr 26, 2025 | Study Period: 2023-2030
Heat shrink tubing is a type of tubing that shrinks when heat is applied. It is primarily used to insulate wires, providing abrasion resistance and environmental protection for stranded and solid wire conductors, connections, and joints.
Heat shrink tubing is also commonly used to repair and replace existing insulation as well as to make new insulation connections.
Heat shrink tubing is made from either polyolefin or PVC materials, and is available in a variety of colors, diameters, and wall thicknesses.
A heat gun, heat lamp, or torch is typically used to shrink the tubing. Once the tubing is heated, it shrinks to a snug fit around the wire or component being covered. The heat-shrink tubing then conforms to the shape of the wire and creates a protective and airtight covering around it.
The benefits of using heat shrink tubing in South Korea include its durability, versatility, and low cost, making it the ideal choice for many industries. In aviation, heat shrink tubing is used for strain relief, and to protect wires and cables from the harsh conditions of the skies.
In the automotive, medical, and industrial sectors, it can be used to protect against vibrations, corrosion, abrasion, and adverse environmental factors. And in the telecommunications industry, shrink tubing is used to create seals that protect against moisture and dust.
Heat shrink tubing helps to improve system performance, increase safety, and prolong the life of wires and components. It is also cost-effective and easy to use in comparison to other forms of insulation.
The South Korea Heat shrink tubing market accounted for $XX Billion in 2022 and is anticipated to reach $XX Billion by 2030, registering a CAGR of XX% from 2023 to 2030.
In today's world, reliable and affordable electricity distribution is essential. Many organisational configurations, technology, regulatory supervision mechanisms, and economic forces make up the transmission and distribution (T&D) industry in the United States. These systems include state, local, federal, and customer-owned cooperatives.
The transmission and distribution networks, as well as the generating units, that supply power to their clients are owned by these fully integrated utilities. While deregulation in certain jurisdictions has changed the sector, this was once one of the prevalent models. Deregulated areas allow for the handling of distribution, generation, and transmission by various companies.
The creation of heat shrink tubing involves two steps. A secondary procedure that makes the tubing heat-shrinkable comes after the initial step of conventional extrusion. Heat and force are employed to expand the tubing's diameter in this subsequent process, the details of which are kept private.
The materials used for developing AI's heat shrink tubing solutions are specially formulated and improved by radiation cross-linking, a technology that offers a repeatable, dependable, shrink-to-fit installation that is compatible with a variety of manufacturing processes.
Automotive, telecommunications, power distribution, aerospace, defence, industrial, and commercial applications use these devices all over the world. Further expanding the application capabilities in the automotive industry are tubing applications in under bonnet cable protection, hoses, brake pipes, air conditioning, diesel injection clusters, connectors, inline splice, wire bundles, ring terminals, seat belt stalks, gas springs, antennas, and others.
The tube goods are manufactured using specially designed materials that have been improved through a process known as radiation cross-linking.
Sl no | Topic |
1 | Market Segmentation |
2 | Scope of the report |
3 | Abbreviations |
4 | Research Methodology |
5 | Executive Summary |
6 | Introduction |
7 | Insights from Industry stakeholders |
8 | Cost breakdown of Product by sub-components and average profit margin |
9 | Disruptive innovation in the Industry |
10 | Technology trends in the Industry |
11 | Consumer trends in the industry |
12 | Recent Production Milestones |
13 | Component Manufacturing in US, EU and China |
14 | COVID-19 impact on overall market |
15 | COVID-19 impact on Production of components |
16 | COVID-19 impact on Point of sale |
17 | Market Segmentation, Dynamics and Forecast by Geography, 2023-2030 |
18 | Market Segmentation, Dynamics and Forecast by Product Type, 2023-2030 |
19 | Market Segmentation, Dynamics and Forecast by Application, 2023-2030 |
20 | Market Segmentation, Dynamics and Forecast by End use, 2023-2030 |
21 | Product installation rate by OEM, 2023 |
22 | Incline/Decline in Average B-2-B selling price in past 5 years |
23 | Competition from substitute products |
24 | Gross margin and average profitability of suppliers |
25 | New product development in past 12 months |
26 | M&A in past 12 months |
27 | Growth strategy of leading players |
28 | Market share of vendors, 2023 |
29 | Company Profiles |
30 | Unmet needs and opportunity for new suppliers |
31 | Conclusion |
32 | Appendix |