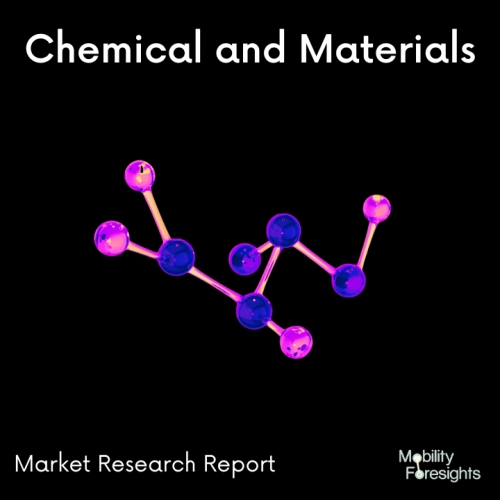
- Get in Touch with Us
Last Updated: Apr 25, 2025 | Study Period: 2024-2030
The spacecraft polyamide thermal control system's job is to keep the components' temperatures within acceptable ranges for particular orbits, power demands, operations, and other parameters.
Additionally, it ought to lessen temperature gradients throughout the spacecraft and certain components, such as lenses.
The Active Thermal Control System (ATCS) maintains a comfortable temperature within the ISS for the astronauts.
Three subsystems make up the ATCS: one to collect heat, one to transport heat, and one to reject heat. Around the ISS, a number of heat exchangers collect heat.
The polyamide thermal control system in the spacecraft is what makes it possible to keep the satellite's (or another space system's) temperatures within certain limits throughout its lifetime.
For instance, if a piece of equipment comes into contact with a temperature that is too high, it may become damaged or its performance may suffer greatly.
Because a component's performance or damage could be severely impacted if it is subjected to temperatures that are either too high or too low, thermal control is necessary to ensure the mission's success and optimal performance.
The Global spacecraft polyamide Thermal control system market accounted for $XX Billion in 2022 and is anticipated to reach $XX Billion by 2030, registering a CAGR of XX% from 2023 to 2030.
NEW PRODUCT LAUNCH
The spacecraft polyamide thermal control system of the Loujia satellite structure system is made of lightweight aluminum alloy and features a frame structure design.
It weighs approximately 22 kilograms. The coordinate system and the dimensions of the in-orbit status are 600 mm 920 mm 450 mm. The geometric center of the bottom surface of the +X panel is where the satellite coordinate system O's origin is.
Axis OZ is parallel to the satellite camera's optical axis and is located on the bottom surface of the +X panel. The Cartesian right-handed coordinate system determines axis OY, which is vertical to the +X panel's bottom surface. Several commercial terrestrial technologies that were initially developed for space applications still permeate our society today.
Solar cells, Global Positioning Systems, and less expensive methods of manufacturing carbon nanotubes are examples.
There may be opportunities for the transfer of modern spacecraft thermal control technologies to terrestrial HVAC&R applications given the long and successful history of spinoffs.
To begin, this paper provides a comprehensive overview of the thermal control of spacecraft. Following that, a look at a few of the most recent technologies for thermal control subsystems in spacecraft is provided, along with an evaluation of how well they might work in terrestrial settings.