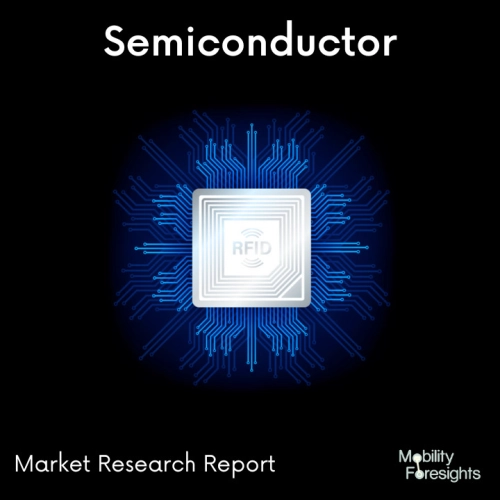
- Get in Touch with Us
Last Updated: Apr 25, 2025 | Study Period: 2023-2030
Spin coating is a method for using centrifugal force to evenly distribute thin films on flat substrates. A spinner or spin coater is the device used for spin coating. A wafer is spun quickly after having a material solution sprayed onto its core.
A mixture of SiO2 and dopants (either boron or phosphorous) floating in a solvent solution is known as spin on glass (SOG). (Actually, the processes are the same even though our boron source is based on a boron polymer and therefore slightly different.)
The primary benefits of spin coating are: It is suitable for both research and rapid prototyping because of how simple and relatively simple it is to set up a process and because it can produce thin, homogeneous coatings at a range of thicknesses.
Prior to toxicity concerns, trichloropropane was a conventional solvent frequently used in spin coating. Nowadays, cyclohexanone is favoured and creates coatings of equivalent quality. Additionally, more polar solvents like N,N-dimethylformamide (DMF) are frequently employed.
In contrast to a paramagnet, which has both averages equal to zero, a spin glass is a disordered magnetic state where the time average of the orientation of any given spin is non-zero and the spatial average of the magnetization over the sites is zero.
The Global spin-on dielectric Coating system market accounted for $XX Billion in 2022 and is anticipated to reach $XX Billion by 2030, registering a CAGR of XX% from 2023 to 2030.
Accumax India, In multilayer metal integrated circuit (IC) designs, planarization of inter-level dielectrics is optimised using spin-on dielectric materials. When employed before the last passivation stage, they can be used to greatly enhance topside planarity.
The materials DuPont provides in this field have no carbon and a low dielectric constant (low-K). With a 1.2-micron film thickness, low moisture absorption, and good gapfill and planarity in a single coat, our flowable oxide (FOx) materials melt and flow.
A number of important advantages are provided by these materials, including high planarization, which lowers process complexity and expense, low moisture uptake, which makes integration easier, and low dielectric constant, which lessens parasitic delay in metal layers.
Sl no | Topic |
1 | Market Segmentation |
2 | Scope of the report |
3 | Abbreviations |
4 | Research Methodology |
5 | Executive Summary |
6 | Introduction |
7 | Insights from Industry stakeholders |
8 | Cost breakdown of Product by sub-components and average profit margin |
9 | Disruptive innovation in the Industry |
10 | Technology trends in the Industry |
11 | Consumer trends in the industry |
12 | Recent Production Milestones |
13 | Component Manufacturing in US, EU and China |
14 | COVID-19 impact on overall market |
15 | COVID-19 impact on Production of components |
16 | COVID-19 impact on Point of sale |
17 | Market Segmentation, Dynamics and Forecast by Geography, 2023-2030 |
18 | Market Segmentation, Dynamics and Forecast by Product Type, 2023-2030 |
19 | Market Segmentation, Dynamics and Forecast by Application, 2023-2030 |
20 | Market Segmentation, Dynamics and Forecast by End use, 2023-2030 |
21 | Product installation rate by OEM, 2023 |
22 | Incline/Decline in Average B-2-B selling price in past 5 years |
23 | Competition from substitute products |
24 | Gross margin and average profitability of suppliers |
25 | New product development in past 12 months |
26 | M&A in past 12 months |
27 | Growth strategy of leading players |
28 | Market share of vendors, 2023 |
29 | Company Profiles |
30 | Unmet needs and opportunity for new suppliers |
31 | Conclusion |
32 | Appendix |