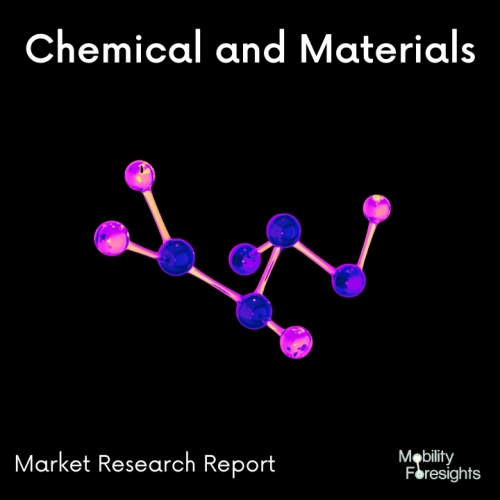
- Get in Touch with Us
Last Updated: Apr 25, 2025 | Study Period: 2024-2030
A class of high-performance stainless steels with an alloy composition that contains about 25% chromium are together referred to as super duplex. This family of alloys, which goes by the name duplex, has a microstructure made up of steel grains that are both austenitic and ferritic.
The distinct mix of physical and mechanical features that define Super Duplex is provided by its duplex nature. Sweden is where the original duplex stainless steel was created for use in sulfite paper manufacturing.
These early alloys were created to address corrosion issues that were prevalent in that industry due to cooling fluids that were high in chlorine.
The Global Super Duplex Stainless Steel Market accounted for $XX Billion in 2023 and is anticipated to reach $XX Billion by 2030, registering a CAGR of XX% from 2024 to 2030.
Osprey® 2507 components from Sandvik and BEAMIT, who introduced 3D printed super duplex to the market, outperformed multiple conventional counterparts.
One material family unquestionably stands out when it comes to withstanding hostile environments. Osprey 2507 is a super duplex alloy that was developed and optimised for additive manufacturing in-house by the foremost material experts at Sandvik Additive Manufacturing. It has great mechanical strength and good corrosion resistance.
Continuously introducing novel duplex and super duplex materials that, with their enhanced qualities, are undeniably a part of Sandvik's DNA, Sandvik has been at the forefront of the materials evolution for duplex stainless steels for decades.
Sandvik's super-duplex stainless steels have already been utilised effectively in corrosive situations like the offshore energy sector exposed to seawater and in difficult chemical processing.
Super-duplex steel, which is often utilised in the form of seamless tubes, plates, and bars, has proven difficult to work with in additive manufacturing up to this point.
They are delighted to state that Sandvik is the first company to bring 3D printed super duplex components to the market by leveraging nearly two centuries of materials expertise and sector-leading knowledge along the additive value chain.
They are quite happy to have discovered components printed to a standard that not only meets, but also outperforms that of several routinely manufactured counterparts, despite the fact that many have tried and failed.
The 8800DWT duplex stainless steel chemical tanker "JIAN HANG YUE DA '' was recently successfully launched. It was built by Taizhou Wuzhou Shipbuilding Industry Co., Ltd.
and inspected by China Classification Society (CCS). The tanker is 119.9 metres in length overall, 19.0 metres wide, 10.0 metres deep, and 7.7 metres deep structurally.
It is an unrestricted area liquid freight tanker propelled by a single machine, a single propeller, and a medium speed diesel engine. The heating temperature of commodities during transportation must not exceed 80°F for refined products and chemicals (IMO 2) with flash points lower than 60°F, in accordance with the CCS's Rules and the IBC Code for Type 2 chemical tankers.
In order to satisfy the demands of transporting various chemical liquid cargo and guarantee the quality of the goods, the tanker is outfitted with 6 pairs of liquid cargo tanks and 1 pair of filthy liquid tanks made of S32205 duplex stainless steel. A separate hydraulically operated immersion cargo pump is installed in each liquid cargo tank.
The Taizhou Office of CCS Zhejiang Branch gave thorough introductions and explanations to the relevant departments and on-site construction workers of the shipyard during the early stages of its construction, paying particular attention to the uniqueness of duplex stainless-steel materials.
These topics included mobilisation verification and storage, welding material control, welding quality control, in-process protection, and process optimisation.It received unanimity of acclaim from the pertinent parties from the shipyard and the on-site construction party, providing a strong foundation for on-time construction with guaranteed quality and quantity in the latter stage, and also ensuring the timely launch of ships.
Lean duplex stainless steels were developed as alternatives to more conventional duplex grades as well as austenitic stainless steels that are typically used in duplex stainless steel fabrication. In order to test for detrimental phases in lean duplex austenitic/ferritic stainless steels, a new standard known as A1084 has just been adopted.
As a subcommittee of ASTM International Committee A01 on Steel, Stainless Steel, and Related Alloys, A01.14 on Methods of Corrosion Testing established A1084, it is a standard.
With the use of A1084, consumers and manufacturers can determine whether a product manufactured of a lean duplex alloy has harmful phases that result from inappropriate heat treatment.
When used, A1084 will provide additional details and comfort outside of currently accepted standard specifications that the material ordered and delivered is free from harmful amounts of unwanted phases, which, if present in significant amounts, frequently will degrade both the materials' corrosion resistance and toughness properties.
Steel Authority of India Limited (SAIL) has developed the ability to produce Super Duplex Stainless Steel in the SS 32205 grade at its Salem Steel Plant (SSP), which represents a significant technological advancement.
By doing this, SAIL has joined the select group of Indian steel producers who have created this grade of steel. So far, the majority of this stainless steel grade has been imported.
The Super Duplex Stainless Steel is stronger and more formable, and it offers improved corrosion resistance. These qualities allow it to be used successfully in a variety of applications in corrosion-prone environments, particularly in the chemical processing equipment (transport and storage, pressure vessels, tanks, piping, and heat exhaust), oil and gas exploration (process equipment, pipes, tubing, marine, and other high chloride environments), and pulp and paper industries (digesters and bleaching).
Super Duplex Stainless Steel (SS 32205 grade) with 3% molybdenum can meet the demands of all these applications, which call for high strength and corrosion resistance steel.
Duplex stainless steel (SS 3220 2 grade) with a 0.4% molybdenum content was previously created by SAIL-SSP and is currently being used to fulfil orders.
SAIL's product offering has been further enriched with the addition of the ability to produce Super Duplex Stainless Steel (SS 32205 grade), allowing it to meet the nation's high-end steel demand. In this new grade, the inclusion of chromium, molybdenum, and nitrogen in the steel gives the steel better corrosion resistance, strength, and formability attributes.
Additionally, this stainless steel has a yield strength that is approximately twice as high as conventional austenitic steel, giving users the option to use it in thinner gauges while maintaining the same strength. SAIL has been working tirelessly to produce steel that can be crucial to these goals, spurred on by the government's call for "Atma Nirbhar Bharat" and a "Vocal for Local."
A step in that direction has been taken with the creation of this high-end grade. We are confident in our ability to actively participate in "Making For India" and "Make in India," as well as to actively supply the steel needed for the country's infrastructure to grow.
Austenitic-ferritic duplex stainless steel, or SuperDuplex, was developed by EOS StainlessSteel for use in harsh environments. Alloying with high levels of chromium, molybdenum, and nitrogen provides exceptional corrosion resistance in a variety of challenging conditions. While keeping super duplex qualities, the product is optimised for additive manufacturing.
The product can be used in numerous use cases in its as-manufactured state thanks to phase balance optimisation. When it comes to the three main technical components of the production processâthe system, the material, and the processâEOS employs a methodology that is unmatched in the additive manufacturing (AM) sector.
Each combination's data is given a Technology Readiness Level (TRL), which makes the predicted performance and production capacity of the solution clear.
Sl no | Topic |
1 | Market Segmentation |
2 | Scope of the report |
3 | Abbreviations |
4 | Research Methodology |
5 | Executive Summary |
6 | Introdauction |
7 | Insights from Industry stakeholders |
8 | Cost breakdown of Product by sub-components and average profit margin |
9 | Disruptive innovation in theIndustry |
10 | Technology trends in the Industry |
11 | Consumer trends in the industry |
12 | Recent Production Milestones |
13 | Component Manufacturing in US, EU and China |
14 | COVID-19 impact on overall market |
15 | COVID-19 impact on Production of components |
16 | COVID-19 impact on Point of sale |
17 | Market Segmentation, Dynamics and Forecast by Geography, 2024-2030 |
18 | Market Segmentation, Dynamics and Forecast by Product Type, 2024-2030 |
19 | Market Segmentation, Dynamics and Forecast by Application, 2024-2030 |
20 | Market Segmentation, Dynamics and Forecast by End use, 2024-2030 |
21 | Product installation rate by OEM, 2023 |
22 | Incline/Decline in Average B-2-B selling price in past 5 years |
23 | Competition from substitute products |
24 | Gross margin and average profitability of suppliers |
25 | New product development in past 12 months |
26 | M&A in past 12 months |
27 | Growth strategy of leading players |
28 | Market share of vendors, 2023 |
29 | Company Profiles |
30 | Unmet needs and opportunity for new suppliers |
31 | Conclusion |
32 | Appendix |