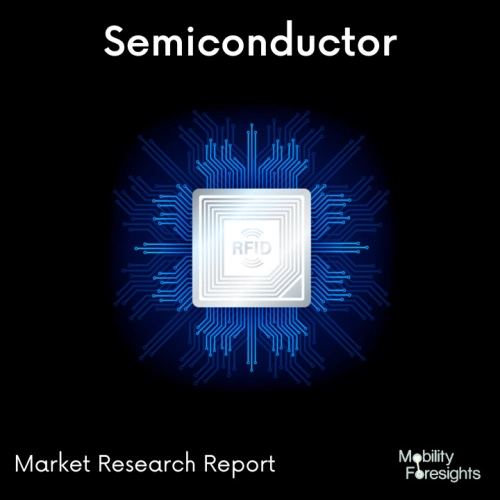
- Get in Touch with Us
Last Updated: Apr 26, 2025 | Study Period: 2024-2030
The semiconductor industry uses the thermo-compression bonding system, also known as thermocompression bonding or thermocompression bonding equipment, to make electrical connections between substrates and microchips or integrated circuit (IC) packages. It is a method of connecting chips to substrates that combines pressure and heat to create a solid, high-quality bond.
The following essential steps are involved in thermo-compression bonding:
Thermo-compression bonding has several benefits, including:
Advanced packaging techniques including flip chip bonding, chip-on-flex bonding, and chip-on-glass bonding all make use of thermo-compression bonding methods. Typically, specialized equipment vendors in the semiconductor sector design and produce these systems.
The Global Thermo-compression Bonding System market accounted for $XX Billion in 2023 and is anticipated to reach $XX Billion by 2030, registering a CAGR of XX% from 2024 to 2030.
A significant customer has received the first Fluxless Thermo-Compression Bonder (TCB) from Kulicke and Soffa Industries. The demand for advanced semiconductor assembly equipment is rising quickly as a result of the increased packaging complexity of high-volume generic semiconductors. New assembly methodologies are required for future logic, processor, mixed-signal, silicon photonics, and sensor applications using heterogeneous integration (HI), also known as chiplets and System-in-Package (SiP).
Through a distinct and integrated fluxless delivery module, the fluxless TCB method avoids contamination concerns while preserving connection integrity. This provides down to 10 m support for the majority of developing heterogeneous packaging needs.
Sl no | Topic |
1 | Market Segmentation |
2 | Scope of the report |
3 | Abbreviations |
4 | Research Methodology |
5 | Executive Summary |
6 | Introduction |
7 | Insights from Industry stakeholders |
8 | Cost breakdown of Product by sub-components and average profit margin |
9 | Disruptive innovation in the Industry |
10 | Technology trends in the Industry |
11 | Consumer trends in the industry |
12 | Recent Production Milestones |
13 | Component Manufacturing in US, EU and China |
14 | COVID-19 impact on overall market |
15 | COVID-19 impact on Production of components |
16 | COVID-19 impact on Point of sale |
17 | Market Segmentation, Dynamics and Forecast by Geography, 2024-2030 |
18 | Market Segmentation, Dynamics and Forecast by Product Type, 2024-2030 |
19 | Market Segmentation, Dynamics and Forecast by Application, 2024-2030 |
20 | Market Segmentation, Dynamics and Forecast by End use, 2024-2030 |
21 | Product installation rate by OEM, 2023 |
22 | Incline/Decline in Average B-2-B selling price in past 5 years |
23 | Competition from substitute products |
24 | Gross margin and average profitability of suppliers |
25 | New product development in past 12 months |
26 | M&A in past 12 months |
27 | Growth strategy of leading players |
28 | Market share of vendors, 2023 |
29 | Company Profiles |
30 | Unmet needs and opportunity for new suppliers |
31 | Conclusion |
32 | Appendix |