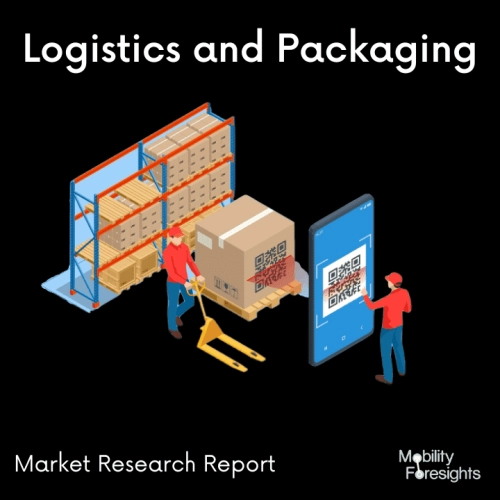
- Get in Touch with Us
Last Updated: Apr 25, 2025 | Study Period: 2024-2030
KEY FINDINGS
The global market for thermoplastic adhesive films is growing at a rapid pace due to excellent bonding performance properties, huge applications across industries, and incessant material science advancement. Among these, thin films bring numerous advantages over traditional adhesives, such as faster fixation times, low emissions of volatile organic compounds, and an array of substrates that can be bonded with the sameâlike metals, plastics, and composites.
Thermoplastic adhesive films find their application in industries for simple lightweight components through complex assemblies in basically all the applications that call for structural enhancement. Further growth of the market is fueled by the development of thermoplastic resin formulations, additives, and treatment technologies rearranging packaging in strength, flexibility, and environmental sustainability.
Yet another factor driving the market growth is the shift towards sustainable raw materials and the creation of eco-friendly coating solutions. The trend promotes geographical expansion and deeper market penetration in emerging economies, hence improving the overall growth of the global thermoplastic adhesive films market.
Thermoplastic adhesive film, commonly known as hot melt adhesive film, is typically presented in the form of a roll. This adhesive solution can be manufactured using different techniques, resulting in either monolayer or multilayer structures.
Examples include:
Two common methods for film extrusion are:
Protechnic and Bemis covers both types of film extrusion technologies, offering a diverse range of polymers including Coployamide, Copeslyester, Polyolefine, and TPU.
Thermoplastic adhesive films serve various functions and find applications in markets such as transportation, footwear, apparel, construction, leather goods, medical, composites, consumer electronic and industrial sectors.
The Global Thermoplastic Adhesive Films Market was valued at $XX billion in 2023 and is projected to reach $XX billion by 2030, with a compound annual growth rate (CAGR) of XX% from 2024 to 2030.
THERMOPLASTIC ADHESIVE FILMS MARKETTECHNOLOGICAL TRENDS
Advanced formulations
Advanced formulation in thermoplastic adhesive films is gaining significant momentum within the industry, where continued development of new products aims at improving adhesives' performance in a wide range of applications. These chemistries zero in on key features for adhesion strength, flexibility, and thermal resistance, and durability in hostile environmental conditions and focus on improving mechanics resins with structures that shall help optimize bond, efficiency, and reliability. In addition, developments include the introduction of additives and modifiers providing specific applications such as UV resistance, flame retardancy, or compatibility with different substrates like metals, plastics, and composites to be included.
Multi-material compatibility
A major development in thermoplastic adhesive films is multi-material compatibility, resulting from the necessity of efficiently binding disparate substrates in various industries. Safe bonding of material combinations such as metals, plastics, ceramics, and composites are developed by manufacturers, thereby crossing traditional boundaries through the development of adhesive formulae. Further innovations in multi-material compatibility, such as optimization of adhesive chemistries and surface treatments to ensure adhesion and achieve internal bonding that is robust, yet flexible and durable in a wide range of environments, are focused on enhancing the structural integrity and functionality of bonded assemblies.
Fast curing and processability
Fast curing and processability are two of the major developments in the area of thermoplastic adhesive films; these meet industrial requirements for efficiency and assembly. With the new technologies to cure, manufacturing companies cut down their processing time drastically and offer solutions with low temperatures or by induction heatingâmicrowave. These technologies cure through fast curing methods like -curing or UV-curing and offer solutions that raise production processes faster, improve efficiency due to downtime reduction, and increase productivity. Fast-cure adhesive films are used in a wide array of industries where parts are to be assembled together quickly, such as the automotive industry, aerospace applications, and electronic assembly and manufacturing.
Prepreg Products
PRF Composite Materials Ltd of Poole. Dorset,. UK. has introduced a range of new primer and adhesive foils strengthening its prepreg product range. The new products are RFA570 eXpress cure adhesive foil and RF Primer. The adhesive foil known as RFA570 has been developed to work in conjunction with the new PRF RP570 and RP570 FR innovative eXpress cure epoxy prepregs, mostly for core bonding application. Critically, it can be cured in a press to 140°C in just 4 minutes, thus causing a much shorter cure timing when using Nomex or aluminum honey sandwich panels, and is also compatible for autoclave curing, which typically requires a 4-minute cycle be used after the instrument heats up to 140°C si. The adhesive film is completely compatible with all of PRF's epoxy prepreg systems.
T-Link
L&L Products has unveiled T-Link, an advancement technology with a higher thermoplastic resin, renowned for unique adhesive properties, to give its consumers productivity and ease of use. The intention from the start has been to put together resin adhesive capabilities with thermoplastic's unique properties in industrial thermoplastics: recyclability, repairability, and manufacturability. The combination at once not only decreases production cycle times but also permits much smaller, more efficient processes. Thermoforming property in the thermoplastic nature of T-Link allows it to easily fit to the depth of drawn parts. Good for irregular manufacturing. L&L Products has T-Link in all different formatsâresin tablet, film, yarn, powder, fiber veil, and unidirectional composite tapeâto meet the variety of application requirements.
Vantage One
One Sales launched Vantage One, the newly developed inexpensive membrane whose ambition is to give the greatest output and lowest cost possible. Unlike their flagship, Top Like 4 T, Vantage One uses cost-effective, adhesive-free membrane technology through protective taffeta fabric and thermoplastic film in combination with load-bearing materials like carbon, dyneema, or black tvaron layered together. Vacuum laminating these along with the fibers, something resembling a vacuumed sealed meat processing technique, ensures that they will be stronger and will be lighter in weight. The lines are expected to be dim but still durable, ranging from 260 to 280 grams per square meter for boats between 35 feet and 55 feet and 410 to 450 grams per meter every square foot for big boats over 90 feet in diameter. Attached features such as pockets for multiplication and the baton without the extra weight
By Geography
By Product Type
By Technology
By Application
Sr.N | Topic |
1 | Market Segmentation |
2 | Scope of the report |
3 | Research Methodology |
4 | Executive Summary |
5 | Average B2B by price |
6 | Introduction |
7 | Insights from Industry stakeholders |
8 | Key Drivers for thermoplastic adhesive films market |
9 | Disruptive Innovation in the Industry |
10 | Overview of thermoplastic adhesive films market |
11 | Major impact on Technological advancements |
12 | Consumer trends in the industry |
13 | Recent technological trends in thermoplastic adhesive films market |
14 | SWOT Analysis of Key Market Players |
15 | New product development in the past 12 months |
16 | Market Size, Dynamics, and Forecast by Geography , 2024-2030 |
17 | Market Size, Dynamics, and Forecast by Product Type , 2024-2030 |
18 | Market Size, Dynamics, and Forecast By Technology, 2024-2030 |
19 | Market Size, Dynamics, and Forecast by Application, 2024-2030 |
20 | Competitive landscape |
21 | Gross margin and average profitability of suppliers |
22 | Merger and Acquisition in the past 12 months |
23 | Growth strategy of leading players |
24 | Market share of vendors, 2023 |
25 | Market Company Profiles |
26 | Unmet needs and opportunities for new suppliers |
27 | Conclusion |