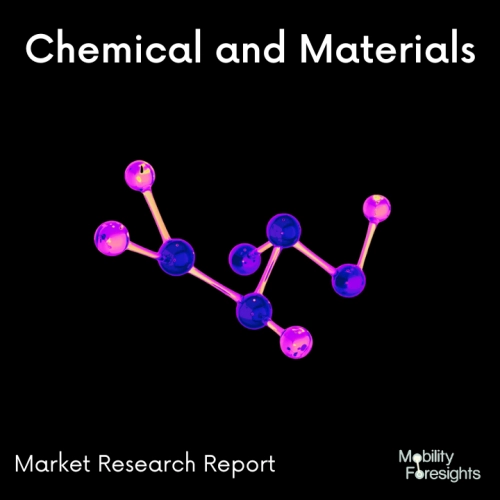
- Get in Touch with Us
Last Updated: Apr 25, 2025 | Study Period: 2024-2030
The weight of thermoplastic polymers reinforced with carbon fibre can be reduced by roughly 50% when compared to steel and 20% when compared to aluminium. Moulding techniques that are typically used to create CFRTPs include injection, rotational, extrusion, vacuum, and compression moulding.
In spite of the fact that CFRTP has recently drawn the attention of numerous researchers due to its superior mechanical and thermal properties, recyclability, flexibility, speed of production, and environmentally friendly manufacturing, it is still in the development stage for some applications, and there are current problems with high manufacturing costs that must be resolved.
The Global Thermoplastic Carbon Fiber Resin market accounted for $XX Billion in 2023 and is anticipated to reach $XX Billion by 2030, registering a CAGR of XX% from 2024 to 2030.
Industry-standard HexTow® carbon fibre from Hexcel and a cutting-edge thermoplastic resin system from Victrex can be used to develop composite materials that might potentially save energy, lighten aircraft, and increase aircraft durability.
Due to the advantages of materials that reduce aircraft weight and the corresponding fuel consumption, while also saving the airline money and reducing carbon emissions for the environment, the use of thermoplastic composites in the aerospace sector is increasing.
Victrex engaged in a procedure that lasted more than two years before VICTREX AETM 250-AS4 UDT was approved for the NCAMP allowables database.
Through NCAMP, Hexcel has a track record of validating composite materials solutions, and the newly released allowables database makes it simple for aircraft designers to adopt a world-class new composite system solution.
The industry's recommended carbon fibre for use in high performance thermoplastic composites is the unsized carbon fibre from Hexcel.
The melting temperature of the high-performance thermoplastic carbon fibre composite prepreg tape VICTREX AETM 250-AS4 UDT is 40°C lower than that of VICTREX PEEK standard.
The PolyAryletherKetone (PAEK) polymer family has special mechanical, physical, and chemical resistance features that make it a remarkable mix of performance and processability for aerospace applications.
Sl no | Topic |
1 | Market Segmentation |
2 | Scope of the report |
3 | Abbreviations |
4 | Research Methodology |
5 | Executive Summary |
6 | Introduction |
7 | Insights from Industry stakeholders |
8 | Cost breakdown of Product by sub-components and average profit margin |
9 | Disruptive innovation in the Industry |
10 | Technology trends in the Industry |
11 | Consumer trends in the industry |
12 | Recent Production Milestones |
13 | Component Manufacturing in US, EU and China |
14 | COVID-19 impact on overall market |
15 | COVID-19 impact on Production of components |
16 | COVID-19 impact on Point of sale |
17 | Market Segmentation, Dynamics and Forecast by Geography, 2024-2030 |
18 | Market Segmentation, Dynamics and Forecast by Product Type, 2024-2030 |
19 | Market Segmentation, Dynamics and Forecast by Application, 2024-2030 |
20 | Market Segmentation, Dynamics and Forecast by End use, 2024-2030 |
21 | Product installation rate by OEM, 2023 |
22 | Incline/Decline in Average B-2-B selling price in past 5 years |
23 | Competition from substitute products |
24 | Gross margin and average profitability of suppliers |
25 | New product development in past 12 months |
26 | M&A in past 12 months |
27 | Growth strategy of leading players |
28 | Market share of vendors, 2023 |
29 | Company Profiles |
30 | Unmet needs and opportunity for new suppliers |
31 | Conclusion |
32 | Appendix |