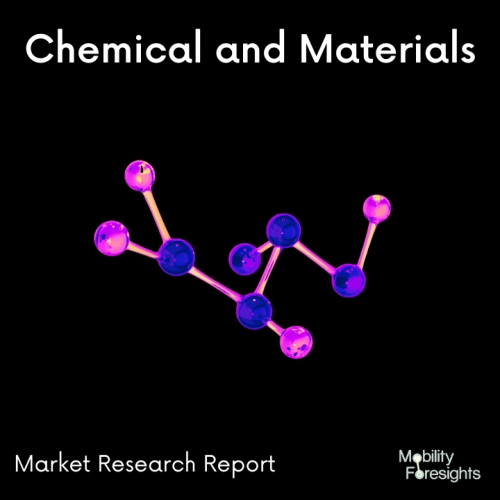
- Get in Touch with Us
Last Updated: Apr 25, 2025 | Study Period: 2024-2030
A class of metallic alloys known as titanium alloys have titanium as its main component. These alloys are renowned for their outstanding strength-to-weight ratio, resistance to corrosion, and performance at high temperatures. They have a wide range of uses in sectors including aerospace, automotive, medicine, and marine where lightweight, robust, and long-lasting materials are needed.
All you need to know about titanium alloys is as follows:
Titanium alloys often contain titanium as well as alloying substances including iron, aluminum, vanadium, nickel, molybdenum, and others. These elements are added to an alloy to improve certain attributes and allow for customization of the alloy's features to satisfy particular needs.
Strength-to-Weight Ratio: Titanium alloys offer significant strength while being lightweight thanks to their exceptional strength-to-weight ratio. As a result, they are especially well suited for uses like aeronautical components, sporting goods, and automotive parts where weight reduction is crucial.
Seawater, chloride solutions, acidic or alkaline conditions, and other environmental factors do not readily cause titanium alloys to corrode. They create a shielding oxide layer on the surface, which guards against corrosion and promotes longevity and dependability.
Titanium alloys perform well at high temperatures and have good qualities including strength retention, creep resistance, and oxidation resistance. These alloys are appropriate for use in gas turbines, exhaust systems, and other high-temperature situations because they can preserve their mechanical characteristics and structural integrity at high temperatures.
Titanium alloys are commonly utilized in medical and dental applications because they are biocompatible, which means the human body tolerates them well. Due to their non-toxicity, superior corrosion resistance, and capacity to integrate with bone tissue, they are frequently used in implants, prostheses, surgical tools, and medical equipment.
The Global Titanium Alloys Market accounted for $XX Billion in 2022 and is anticipated to reach $XX Billion by 2030, registering a CAGR of XX% from 2023 to 2030.
For several crucial applications in the aerospace, chemical, medical, and energy industries, titanium alloys are preferred due to their distinctive mix of mechanical and physical qualities.
Microstructure (Alpha and Near-alpha Alloy, Alpha-beta Alloy, and Beta Alloy), End-user Industry (Aerospace, Automotive and Shipbuilding, Chemical, Power and Desalination, and Other End-user Industries), and Geography (Asia-Pacific, North America, Europe, South America, and Middle-East and Africa) are the main categories used to segment the titanium alloy market.
The Aerospace Industry's Demand for Titanium Alloys is Growing. One of the most crucial raw materials for the aerospace sector is titanium. The aerospace raw material market is dominated by titanium alloys, with aluminum alloys coming in second.
When comparing the weight of raw materials, titanium alloys rank as the third-most significant raw material utilized in the aircraft sector. The aerospace sector uses around 75% of the high-grade titanium sponge available. In addition to uses for aircraft's airframe (landing gear, fasteners, and wing beams), it is employed in their engines, blades, and shafts.
Furthermore, titanium alloys are useful in aviation engine casings and other applications due to their ability to function at extreme temperatures ranging from sub-zero to over 600°C.
Due to rising demand from the chemical, high-end aircraft, medical, and environmental protection industries, China currently holds a monopoly on the titanium alloy market in the Asia-Pacific region, a trend that is anticipated to continue during the projected period.
Titanium output is anticipated to increase significantly as a result of the opening of new facilities by Xinjiang New Material Co. Ltd. and Chaoyang Baisheng Co. Ltd in China.
The country's expanding industrial activity in the aerospace sector are the key factors driving China's demand for titanium alloy. The government has prioritized the aerospace sector and is investing heavily to expand domestic production capacity.
One of the most comprehensive initiatives to reach the pinnacle of aerospace development and production may be seen in the Chinese aerospace strategy. A memorandum of understanding (MOU) was signed by PTC Industries and Defence PSU Mishra Dhatu Nigam (MIDHANI) for a technology alliance.
According to the terms of their MOU, PTC Industries and Midhani will utilize one another's technological capabilities to produce titanium alloy plates and sheets, manufacture titanium alloy pipes and tubes using locally processed raw materials, and fabricate critical parts and LRUs for the defense and aerospace industries using PTC's advanced machining facility and Midhani's forged and rolled products.
The Houston, Pennsylvania-based Perryman Company intended to dramatically increase its titanium melting capacity by adding more electron beam and vacuum arc remelt furnaces. They were to be located in Pennsylvania's Washington County.
Ti-6Al-4V is the universal designation for commercially manufactured pure titanium and titanium alloys. These are mostly employed in the production of aircraft airframes and engine components. Aviation gasoline is quickly used by aircraft engines.
The weight of the airplane and its engine should be below to save fuel consumption. To reduce weight and increase fuel economy, airplanes employ titanium and its alloys. Aircraft are manufactured for commercial purposes using cutting-edge technology and superior management techniques.
Because it is lightweight, commercially accessible pure titanium is frequently used to build airplanes and the parts that go inside them. Additionally, it has good corrosion resistant qualities as well as strong compressive and tensile strengths. Tiny quantities of aluminum and vanadium are alloyed with titanium for the majority of uses.
Sl no | Topic |
1 | Market Segmentation |
2 | Scope of the report |
3 | Abbreviations |
4 | Research Methodology |
5 | Executive Summary |
6 | Introduction |
7 | Insights from Industry stakeholders |
8 | Cost breakdown of Product by sub-components and average profit margin |
9 | Disruptive innovation in the Industry |
10 | Technology trends in the Industry |
11 | Consumer trends in the industry |
12 | Recent Production Milestones |
13 | Component Manufacturing in US, EU and China |
14 | COVID-19 impact on overall market |
15 | COVID-19 impact on Production of components |
16 | COVID-19 impact on Point of sale |
17 | Market Segmentation, Dynamics and Forecast by Geography, 2023-2030 |
18 | Market Segmentation, Dynamics and Forecast by Product Type, 2023-2030 |
19 | Market Segmentation, Dynamics and Forecast by Application, 2023-2030 |
20 | Market Segmentation, Dynamics and Forecast by End use, 2023-2030 |
21 | Product installation rate by OEM, 2023 |
22 | Incline/Decline in Average B-2-B selling price in past 5 years |
23 | Competition from substitute products |
24 | Gross margin and average profitability of suppliers |
25 | New product development in past 12 months |
26 | M&A in past 12 months |
27 | Growth strategy of leading players |
28 | Market share of vendors, 2023 |
29 | Company Profiles |
30 | Unmet needs and opportunity for new suppliers |
31 | Conclusion |
32 | Appendix |