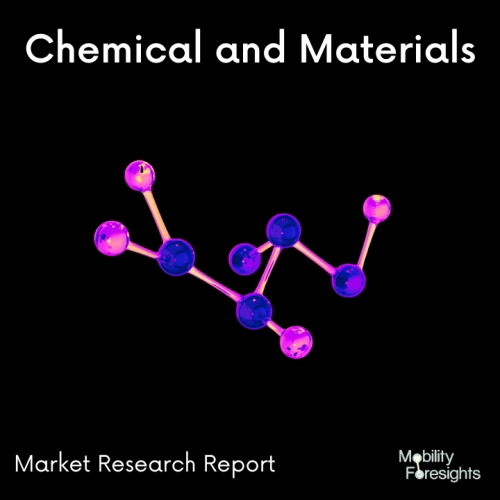
- Get in Touch with Us
Last Updated: Apr 25, 2025 | Study Period: 2024-2030
Titanium Aluminide (TiAl) is an intermetallic alloy that is composed of titanium and aluminum. This alloy has a high strength-to-weight ratio, making it an attractive material for use in various industries, such as aerospace, automotive, and energy.
TiAl is known for its excellent heat resistance and exceptional fatigue strength, making it a great choice for components that are exposed to high temperature and stress. Additionally, TiAl has a low density, which contributes to its lightweight properties. This makes it ideal for applications where weight savings are desired, such as in aircraft and spacecraft.
TiAl is produced by several methods, including vacuum arc melting, powder metallurgy, and hot pressing. Each method has its own benefits and drawbacks; for example, powder metallurgy is often used for small parts, as it is a cost-effective process. Vacuum arc melting is often used to create larger ingots, which are then machined into the desired shape.
TiAl alloys can be further strengthened through a variety of heat treatments, such as age hardening and surface treatments. This can improve their wear resistance and strength. Additionally, TiAl alloys can be tailored to have different properties, such as corrosion resistance and electrical conductivity.
The use of TiAl alloys has a number of advantages, such as reduced cost and weight, improved fatigue strength, and enhanced thermal and electrical properties. However, TiAl alloys are difficult to machine, as they are sensitive to heat.
This can make it difficult to achieve the desired shape and finish. Additionally, they are prone to corrosion, and require special coatings or treatments to protect them from the elements. Despite these challenges, TiAl alloys remain a popular material for many applications, due to their attractive combination of strength, light weight, and resistance to heat.
The Global Titanium Aluminide Market accounted for $XX Billion in 2023 and is anticipated to reach $XX Billion by 2030, registering a CAGR of XX% from 2024 to 2030.
Leading Ukrainian titanium company Velta LLC revealed that it has created the highly sought-after intermetallic compound titanium aluminide (TiAl) through the use of its exclusive closed-cycle manufacturing technique.
This accomplishment will enable new and more reliable uses of intermetallic compounds across commercial and defense sectors at a fraction of the carbon footprint of conventional approaches.
It also represents a significant leap for titanium technology. Titanium metal and its alloys, including titanium aluminide, require a lot of energy and time to produce conventionally.
The superior product produced by the novel Velta Ti Process, which turns ilmenite concentrate into titanium alloy powders, has a carbon footprint that is five to ten times smaller than that of products generated using the conventional Kroll process.
Intermetallic materials are becoming more and more valuable in the automotive, aerospace, and civil infrastructure sectors. Titanium aluminides may be able to compete with superalloys because of the ground-breaking, innovative Velta Ti Process.
Weight is sacrificed to achieve the heat resistance offered by superalloys based on nickel, iron-chromium-nickel, cobalt, or mixed bases. Titanium aluminide is perfect for aerospace engines like the Airbus A320neo, Boeing 737 MAX, Boeing 777, and Boeing 787 since it is lightweight and extremely heat resistant. Gas turbine blades for power generation and orthopedic and dental implants are further used.
Techniques for producing sheets and sheet-metal components from an alloy generated by a powder-metal (PM) process, specifically γ titanium aluminide, have been developed.
When combined, the alloy and manufacturing processes should be able to meet the demand for reasonably priced, lightweight, high-temperature-resistant parts for propulsion systems, control surfaces, and overall aircraft and spaceship structures.
The alloy has a specific strength that is comparable to superalloys' specific strengths, but it has a higher specific stiffness and a lower density. This alloy can be used in place of superalloys for applications where the temperature range is 500 to 800 °C, allowing component weights to be reduced by up to 50%.
One method that was created in tandem with this alloy and the previously described procedure is sheet-rolling, which enables the alloy to be produced in sheets at a comparatively low cost.
An alternative method that does away with the requirement for hot presses in environmental chambers is hot forming at relatively low temperatures. Innovative laser welding and brazing transient-liquid-phase bonding techniques were also developed.
Sl no | Topic |
1 | Market Segmentation |
2 | Scope of the report |
3 | Abbreviations |
4 | Research Methodology |
5 | Executive Summary |
6 | Introduction |
7 | Insights from Industry stakeholders |
8 | Cost breakdown of Product by sub-components and average profit margin |
9 | Disruptive innovation in the Industry |
10 | Technology trends in the Industry |
11 | Consumer trends in the industry |
12 | Recent Production Milestones |
13 | Component Manufacturing in US, EU and China |
14 | COVID-19 impact on overall market |
15 | COVID-19 impact on Production of components |
16 | COVID-19 impact on Point of sale |
17 | Market Segmentation, Dynamics and Forecast by Geography, 2024-2030 |
18 | Market Segmentation, Dynamics and Forecast by Product Type, 2024-2030 |
19 | Market Segmentation, Dynamics and Forecast by Application, 2024-2030 |
20 | Market Segmentation, Dynamics and Forecast by End use, 2024-2030 |
21 | Product installation rate by OEM, 2023 |
22 | Incline/Decline in Average B-2-B selling price in past 5 years |
23 | Competition from substitute products |
24 | Gross margin and average profitability of suppliers |
25 | New product development in past 12 months |
26 | M&A in past 12 months |
27 | Growth strategy of leading players |
28 | Market share of vendors, 2023 |
29 | Company Profiles |
30 | Unmet needs and opportunity for new suppliers |
31 | Conclusion |
32 | Appendix |