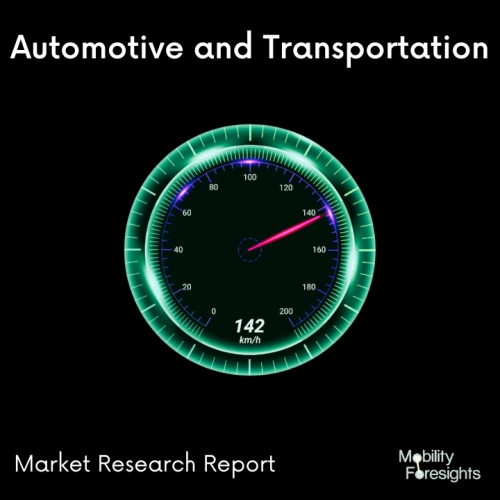
- Get in Touch with Us
Last Updated: Apr 25, 2025 | Study Period: 2024-2030
TPO bumper recycle is a 100% recyclable material, but the recycling stream isn't as strong as it should be because of the material's nature and the long life cycle applications it typically has.
The only practical way to repurpose a vehicle's bumper is to shred and recycle it because reselling and reapplying a used fascia is impractical and potentially dangerous (most auto body shops don't do it anyway).
A plastic granulator can be used to process scrap plastic car bumpers into new plastic pellets. By combining the recycled raw material from scrap vehicle bumpers with 7% fiberglass and a certain percentage of PBT material, it can also be transformed into new vehicle bumpers.
Ethylene-propylene rubber and fillers like carbon fiber, talc, and fiberglass are used to produce each thermoplastic polyolefin layer. The TPO's strength and adaptability are enhanced by these fillers.
TheGlobal TPO bumper recycling marketaccounted for $XX Billion in 2023 and is anticipated to reach $XX Billion by 2030, registering a CAGR of XX% from 2024 to 2030.
Ultra-Poly Corp., based in Portland, Pennsylvania, has collaborated with the Plastics Industry Association on a project to collect and recycle automotive bumper covers made of thermoplastic polyolefin (TPO).
A case study about the project has been published by the Washington-based trade association and the recycling company.
According to the two organizations, the demonstrated method has the potential to direct approximately 500 tons of plastic toward recycling outcomes.
According to a press release issued by Ultra-Poly and the Plastics Industry Association, the study also revealed that recycled material possesses between 85% and 90% of the flexibility and elasticity of virgin material. This makes recycled material ideal for a variety of applications in final products.
The bumper covers are not collected and preprocessed by third parties in the way that Ultra-Poly's process does. Instead, Ultra-Poly collects used covers directly from body shops, where they have already been removed from automobiles and their reusable connected parts salvaged.
This project shows that true post-consumer material doesn't have to be collected at the curb and preprocessed by materials recovery facilities.
It can also be sourced directly at the point of production, resulting in recycled products that are more consistent and lower in carbon footprint.
Additionally, point-of-generation collection ensures a constant supply of material. Each month, a single body shop can produce up to 30 scrap bumper covers.
According to the organizations, the body shop itself saves money on dumpster space and is relieved of the concern that damaged covers might be sold incorrectly as replacement parts.
The Plastics Industry Association's larger New End Market Opportunities (NEMO) program, which focuses on developing novel strategies for the recovery, recycling, and repurposing of plastic products, includes the Ultra-Poly case study.
NEMO focuses particularly on difficult issues like plastic grocery store bags. This recycled polyethylene film has been successfully used to produce asphalt for road construction in another NEMO project.
Sl no | Topic |
1 | Market Segmentation |
2 | Scope of the report |
3 | Abbreviations |
4 | Research Methodology |
5 | Executive Summary |
6 | Introduction |
7 | Insights from Industry stakeholders |
8 | Cost breakdown of Product by sub-components and average profit margin |
9 | Disruptive innovation in the Industry |
10 | Technology trends in the Industry |
11 | Consumer trends in the industry |
12 | Recent Production Milestones |
13 | Component Manufacturing in US, EU and China |
14 | COVID-19 impact on overall market |
15 | COVID-19 impact on Production of components |
16 | COVID-19 impact on Point of sale |
17 | Market Segmentation, Dynamics and Forecast by Geography, 2024-2030 |
18 | Market Segmentation, Dynamics and Forecast by Product Type, 2024-2030 |
19 | Market Segmentation, Dynamics and Forecast by Application, 2024-2030 |
20 | Market Segmentation, Dynamics and Forecast by End use, 2024-2030 |
21 | Product installation rate by OEM, 2023 |
22 | Incline/Decline in Average B-2-B selling price in past 5 years |
23 | Competition from substitute products |
24 | Gross margin and average profitability of suppliers |
25 | New product development in past 12 months |
26 | M&A in past 12 months |
27 | Growth strategy of leading players |
28 | Market share of vendors, 2023 |
29 | Company Profiles |
30 | Unmet needs and opportunity for new suppliers |
31 | Conclusion |
32 | Appendix |