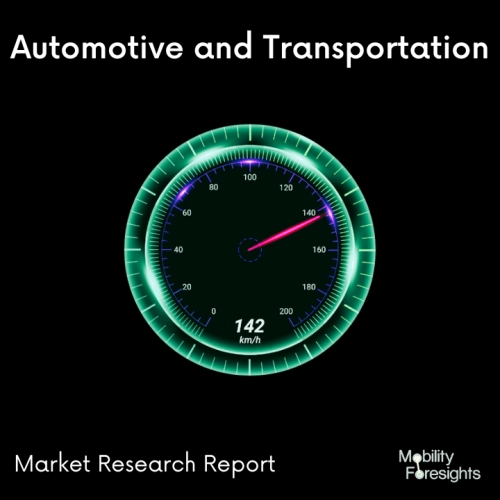
- Get in Touch with Us
Last Updated: Apr 25, 2025 | Study Period: 2024-2030
The magnets enable the generation of a highly superconducting magnet in a very small volume in an electric traction motor. Use of electromagnets, which produce a magnetic field by running current through a conducting coil, might be an alternative.
It can be demonstrated that the corresponding magnetic field is created by a piece of NdFeB magnet that is 3 mm thick. Magnetic motor and vehicle magnet applications can make use of ferrite (ceramic) magnets or rare earth (Samarium Cobalt and Neodymium) magnets. Rare Earth magnets typically have a strength of two to three times that of ceramic or ferrite permanent magnets.
Some of the drivers projected to propel market expansion include the rising demand for electric vehicles and the benefits of permanent magnet motors, such as the latter is ability to achieve accurate speed control without the need for a feedback sensor.
Neodymium magnets held the greatest market share, and throughout the course of the forecast period, it is anticipated that this market category will grow the fastest. Neodymium is a material of compulsive choice for industrial applications due to its high-energy product and high residual flux density.
When compared to a conventional motor, neodymium can produce greater performance and torque because it is available in both high- and low-grade types.
Rare earth magnets are increasingly being used in traction motors for automobiles. Neodymium Iron Boron (NdFeB), a hard magnetic material made from rare earths, in particular, has provided important performance advantages that were not feasible with alternative technologies, enabling the development of small, torque- and power-dense electric traction motors.
Although the price has lately increased to a level closer to historical levels, governments and many hybrid and electric vehicle manufacturers continue to be concerned.
Adams Magnetic is a leading mobiliser of the equipment in the market. The latest integration has been the use of samarium cobalt magnets in magnetic motors.
Due to its strong magnetic properties, outstanding temperature endurance, and dependable performance without oxidation protection, samarium cobalt (SmCo) magnets are the best choice for high temperature motor applications. Most uses do not require plating or surface coatings, which makes them useful for medical applications as well.
Curie temperatures range from 700 to 800 °C, while the Samarium Cobalt magnets operate between 250 and 550 °C.
Horizon Technology is part of the component manufacture trending companies in the current industry. With no need for expensive machining, the net-shape property of powder metal allows for the creation of the slots you can see in the aforementioned image on the powder metal rotor.
A powder metal rotor for a permanent magnet motor can reach strength comparable to competitive technologies by employing sintered soft magnetic material. The efficiency of this design is further increased by the fact that SMC losses are lower than those of laminated 3 percent silicon iron at the high switching frequencies anticipated.
Sl no | Topic |
1 | Market Segmentation |
2 | Scope of the report |
3 | Abbreviations |
4 | Research Methodology |
5 | Executive Summary |
6 | Introduction |
7 | Insights from Industry stakeholders |
8 | Cost breakdown of Product by sub-components and average profit margin |
9 | Disruptive innovation in the Industry |
10 | Technology trends in the Industry |
11 | Consumer trends in the industry |
12 | Recent Production Milestones |
13 | Component Manufacturing in US, EU and China |
14 | COVID-19 impact on overall market |
15 | COVID-19 impact on Production of components |
16 | COVID-19 impact on Point of sale |
17 | Market Segmentation, Dynamics and Forecast by Geography, 2024-2030 |
18 | Market Segmentation, Dynamics and Forecast by Product Type, 2024-2030 |
19 | Market Segmentation, Dynamics and Forecast by Application, 2024-2030 |
20 | Market Segmentation, Dynamics and Forecast by End use, 2024-2030 |
21 | Product installation rate by OEM, 2023 |
22 | Incline/Decline in Average B-2-B selling price in past 5 years |
23 | Competition from substitute products |
24 | Gross margin and average profitability of suppliers |
25 | New product development in past 12 months |
26 | M&A in past 12 months |
27 | Growth strategy of leading players |
28 | Market share of vendors, 2023 |
29 | Company Profiles |
30 | Unmet needs and opportunity for new suppliers |
31 | Conclusion |
32 | Appendix |